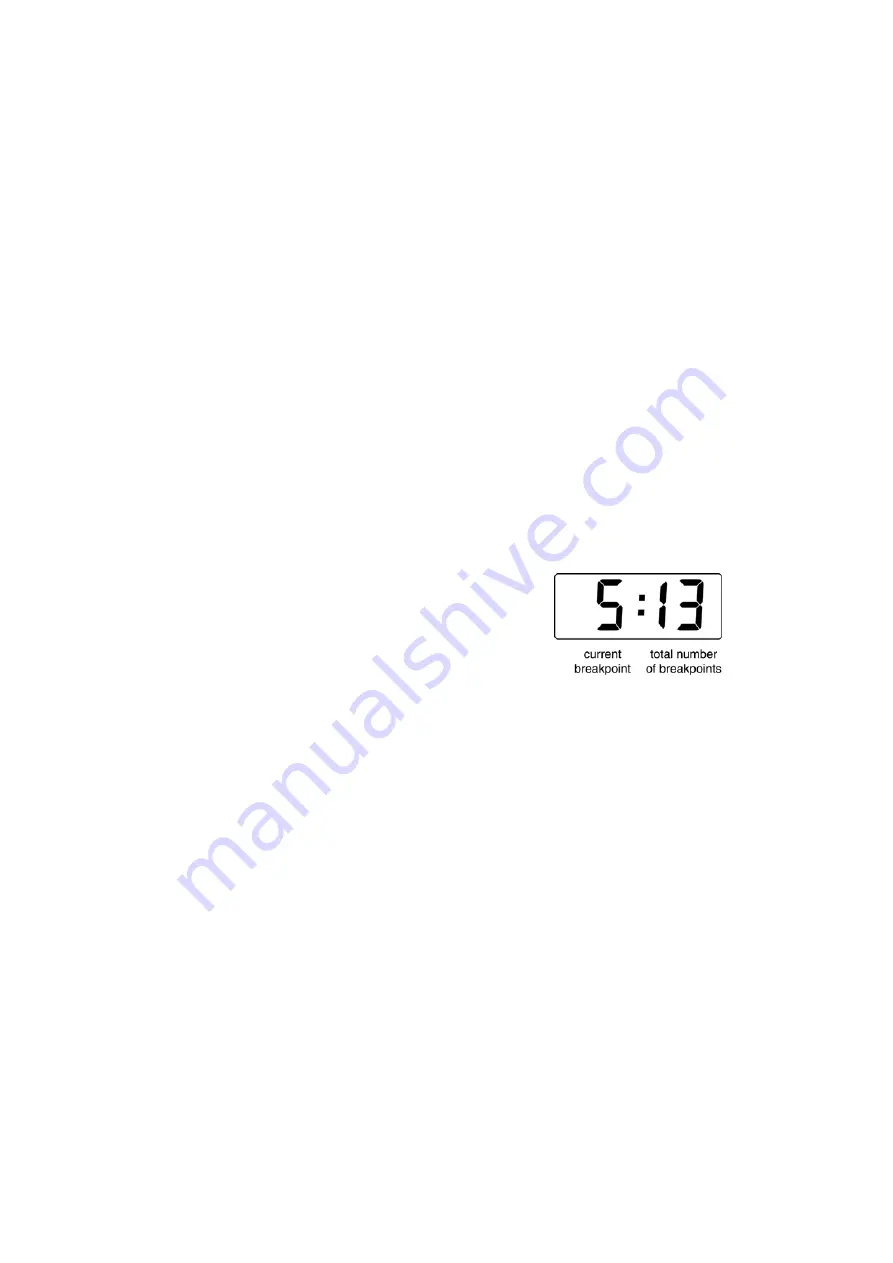
14
When the required number of linearising break-
points have been entered, return to the
linearisation sub-menu by pressing
E
.
The
indicator will display the 'Add' or 'dEL' prompt
depending upon the last function used.
Now that the the number of break-points has been
entered, the input current at which each occurs
and the corresponding indicator display can be
defined by th ‘Pts’ sub-function.
Using the
▲
or
▼
button select 'PtS' from the sub-
menu and press
P
which will select the starting
point for the first segment '0 : n', where n is the
total number of linearising break-points entered.
The selected linearising break-point can be
changed using the
▲
and
▼
buttons. When the
required linearising break-point has been selected
set the indicator input current to the exact value at
which the break-point is required and press
P
.
Using the
▲
and
▼
buttons and the
P
button to
move between digits, enter the required indicator
display at this break-point.
When set as required, press the
E
push-button
to
enter the required indicator display and return to
the sub-menu from which the next beak-point can
be selected.
When all the break-points have been calibrated
pressing
E
twice will return the indicator to the
‘CAL’ function in the configuration menu.
Note:
The indicator input current must be adjusted
to the required value before the
P
button is
operated to enter the required indicator display.
6.2 Lineariser calibration using the internal
reference.
The ‘SEt’ function enables the lineariser to be
calibrated without the need for an accurate
external current source. Throughout the
calibration the indicator input current may be any
value between 4 and 20mA.
The ‘SEt’ functions contains four sub-functions.
Display Description of function
'Add'
Add a break-point
Adds a new break-point before the
displayed break-point. The calibration
of existing break-points is not changed,
but the identification number of all
subsequent break-point is increased by
one.
'dEL'
Remove a break-point
Removes the displayed break-point
and joins the preceding segment to the
following segment with a straight line.
The identification number of all
subsequent break-points is decreased
by one.
'in'
Defines the current at which break-
point occurs.
Enables the required current at each
break-point to be defined without
having to input an accurate input
current to the indicator.
'diSP'
Defines indicator display at break-
point.
Enables the indicator display at each
break-point to be defined.
The number of break-point required should first be
entered using the 'Add' and 'dEL' sub-functions.
In both these sub-functions the indicator initially
displays the current break-point and the total
number of break-point being used as shown below.
To add a break-point using the
▲
or
▼
button
select 'SEt' from the configuration menu and press
P
which will result in the
'Add' sub-function prompt
being displayed. To enter the sub-function press
P
which will reveal the current break-point and the
total number of break-point which have already
been entered. Each subsequent operation of the
P
push-button will introduce an additional break-
point up to the maximum of 17 (breakpoint 16).
When adding a break-point to a calibrated
indicator, the insertion position for the new
segment can be selected using the
▲
and
▼
push-buttons.
The delete break-point, sub-function 'dEL' operates
in exactly the same way as the 'Add' sub-function
described above. Once within the ‘dEL’ function
each time the
P
button is pressed a break-point is
removed. When deleting a break-point from a
calibrated indicator, the break-point to be deleted
can be selected using the
▲
and
▼
push-buttons.
The minimum number of break-point is 2, break-
points 0 and 1.