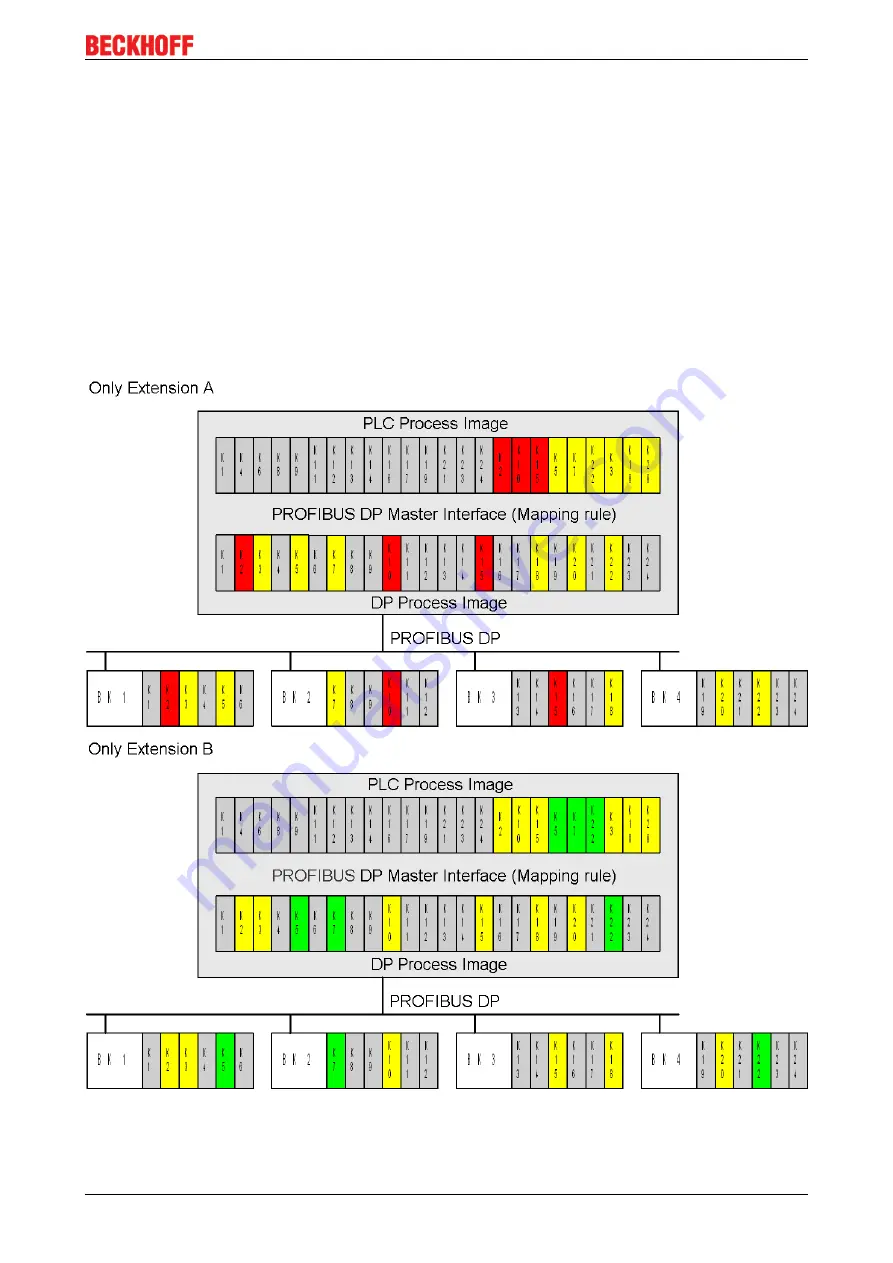
Extended functions
BK3xx0
81
Version: 4.3.0
If the Bus Coupler is not already being operated with the maximum Bus Terminal implementation level, the
PROFIBUS DP configuration will not agree with the Bus Terminal structure that it finds. So that the Bus
Coupler can nevertheless represent the process signals from the connected Bus Terminals in the process
image that is to be exchanged with the PROFIBUS DP master, the mapping rule is now required.
Because the Bus Coupler maps the process signals from the Bus Terminals into the DP process image
according to a fixed algorithm (first complex, then digital terminals, each in the sequence in which they are
plugged in), the only information that is missing is that of which of the Bus Terminals that are included in the
PROFIBUS DP configuration are indeed truly present. This information can be transmitted via the acyclic
DPV1 Write, or through the 2-byte PLC interface for those PROFIBUS DP master interfaces that do not
support PROFIBUS DPV1. The acyclic DPV1 Write is usually available through function blocks (TwinCAT:
ADS-Write, S7 400: SFB 52 (read) and SFB53 (write)) from the controller program. The 2-byte PLC interface
of the Bus Coupler is mapped directly into the controller's process image. As soon as a machine extension is
activated or deactivated, the controller program can therefore activate or deactivate the associated Bus
Terminals.
Example as above, where deactivated terminals are marked in yellow:
Fig. 49: Process images of the two different machine configurations with deactivated terminals
Содержание BK3 0 Series
Страница 1: ...Documentation BK3xx0 Bus Coupler for PROFIBUS DP 4 3 0 2019 04 03 Version Date...
Страница 2: ......
Страница 11: ...Product overview BK3xx0 11 Version 4 3 0 2 2 BK3150 Technical data Fig 2 BK3150 Bus Coupler for PROFIBUS DP...
Страница 83: ...Extended functions BK3xx0 83 Version 4 3 0 Fig 50 State transitions in the Bus Coupler...