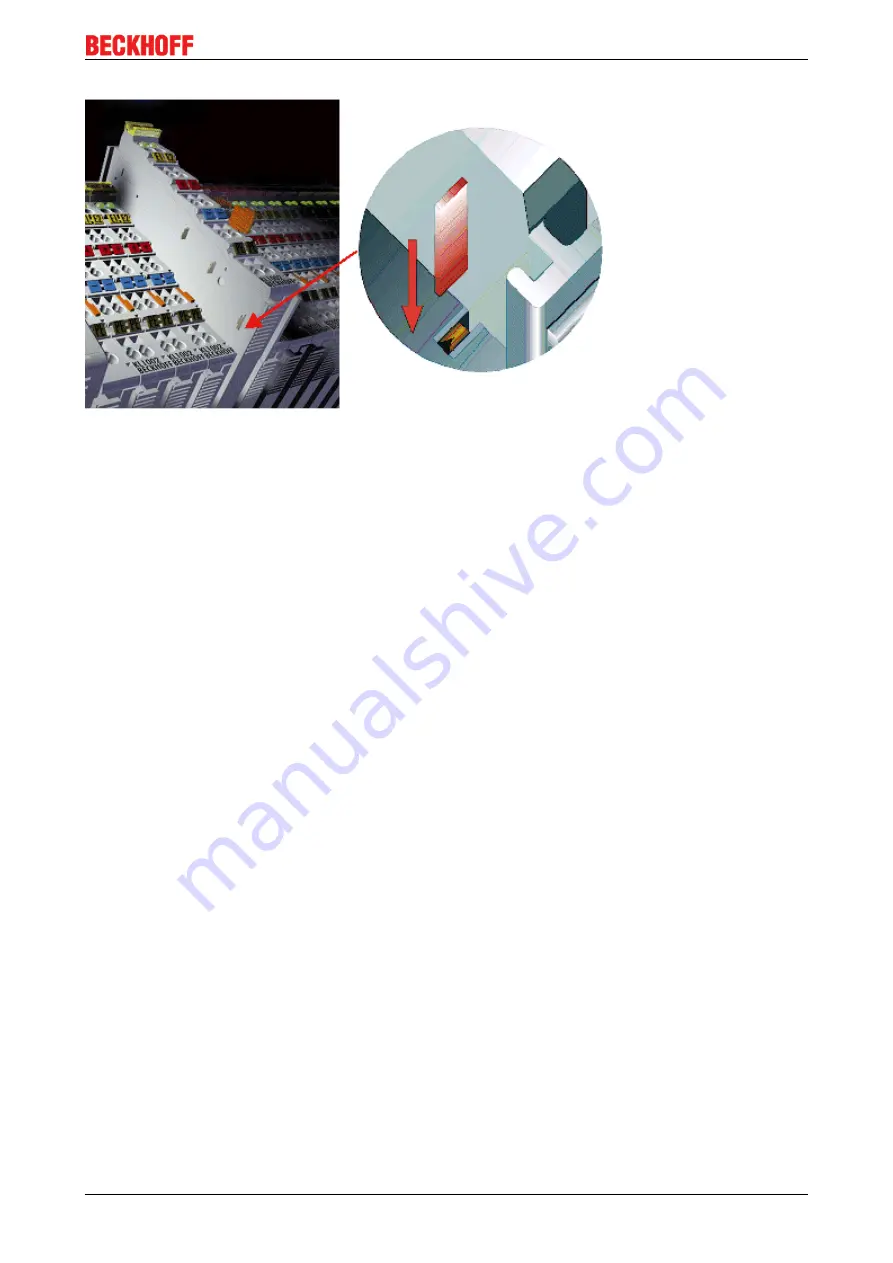
Mounting and wiring
BC5250
19
Version: 2.0.0
Fig. 7: Power contact on the left
It should be noted that, for reasons of electromagnetic compatibility, the PE contacts are capacitively
coupled to the mounting rail. This can both lead to misleading results and to damaging the terminal during
insulation testing (e.g. breakdown of the insulation from a 230 V power consuming device to the PE
conductor). The PE supply line at the Bus Coupler / Bus Terminal Controller must be disconnected for an
insulation test. In order to uncouple further feed locations for the purposes of testing, the feed terminals can
be pulled at least 10 mm out from the connected group of other terminals. In that case, the PE conductors do
not have to be disconnected.
The power contact with the label PE must not be used for other potentials.