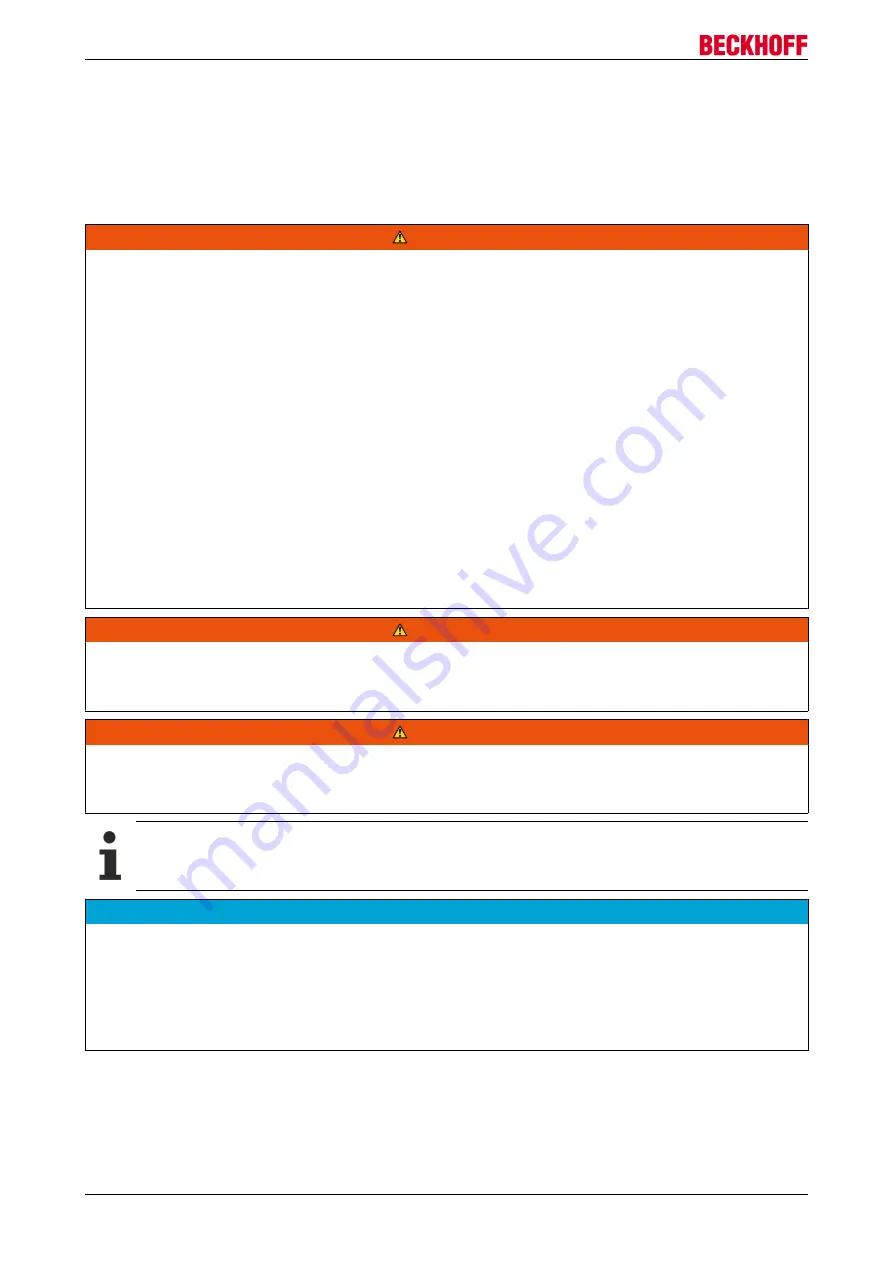
For your safety
AL225x Connector-Box
10
Version: 1.9
3.3
Special safety instructions for the connector box
The safety instructions are designed to avert danger and must be followed during installation,
commissioning, production, troubleshooting, maintenance and trial or test assemblies. The connector boxes
of the AL225x series are not designed for stand-alone operation and are always installed in a machine or
system. After installation, the documentation the documentation and the safety instructions provided by the
machine manufacturer must be read and applied.
WARNING
Serious risk of injury through high electrical voltage!
• Negligent, improper handling of the connector boxes and bypassing of the safety facilities of the system
or machine may result in personal injury or death through electric shock.
• When installing and working on the connector boxes, all machine components and assemblies MUST be
de-energized and secured against unintentional restoration of electrical power.
• The machine manufacturer must prepare a hazard analysis for the machine, and must take appropriate
measures to ensure that unexpected movements cannot lead to injury to persons or to objects.
• Power connections may be live, even if machine components don't move. Never undo the electrical con-
nections to the motor when it is live. Under unfavorable conditions arcing may occur, resulting in injury
and damage to contacts.
• Disconnect the linear motor from the servo drive and secure it against reconnection before working on
electrical parts with a voltage > 50 V.
• Due to the DC link capacitors, the DC link contacts "ZK+ and ZK- (DC+ and DC-)" and "RB+ and RB-"
may be subject to dangerous voltages exceeding 890V
DC
, even after the servo drive was disconnected
from the mains supply. Wait 5 minutes for the AX5101 - AX5125 and AX520x; 15 minutes for the
AX5140/AX5160/AX5172; 30 minutes for the AX5190/AX5191; 45 minutes for the AX5192/AX5193 after
disconnecting, and measure the voltage at the DC links "ZK+ and ZK- (DC+ and DC-)". The device is
safe once the voltage has fallen below 50 V.
WARNING
Risk of injury through failure of the drive system!
Electronic equipment is not fail-safe. The machine manufacturer is responsible for ensuring that the con-
nected motors and the machine are brought into a safe state in the event of a fault in the drive system.
WARNING
Caution – Risk of injury through electric shock!
Remove the motor and feedback lines from the connector box to the servo drive when you open the con-
nector box.
Selection of motor and feedback cables!
For connecting linear drives, we recommend drag chain-capable, highly dynamic motor and feed-
back cables.
NOTE
Danger for persons, the environment or equipment
• Please read this manual carefully before using the connector boxes. Follow all safety instructions.
Should anything be unclear, please contact the sales office for your area and refrain from any further
work on the system.
• Only well trained, qualified electricians with sound knowledge of drive equipment may work on the de-
vice.
Содержание AL-2255-0001
Страница 2: ......
Страница 4: ...Contents AL225x Connector Box 4 Version 1 9...