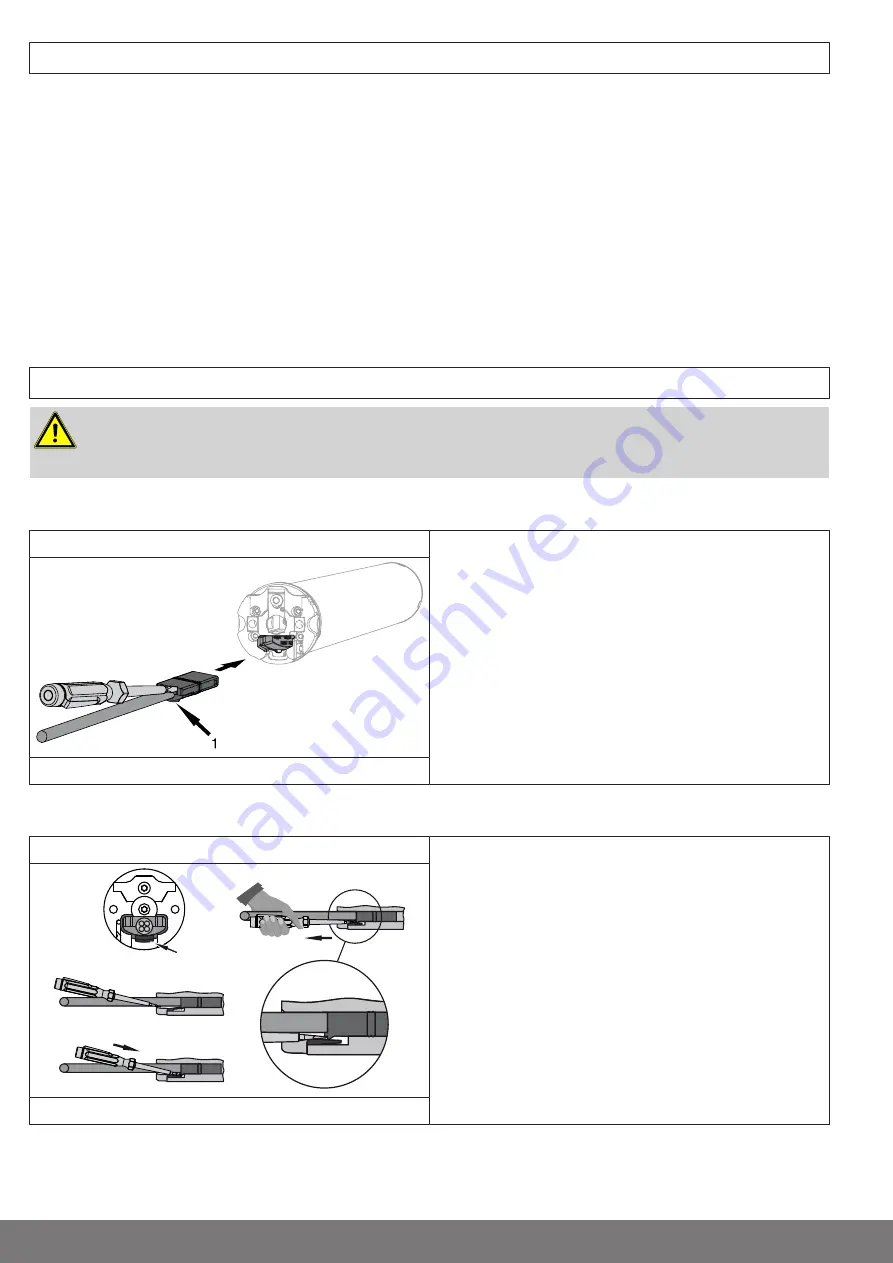
Intended use
The type of tubular drive described in these instructions is intended solely for the operation of sun protection systems with locking
systems . To function properly, these tubular drives need a fixed stop in the upper limit position (retracted blind).
When mounting connection parts on the drive dia. 35 mm PXX/XX, only use screws EJOT Delta PT 40x12 WN 5454 Torx (9900 000
545 4).
It may only be used in networked systems if all the individual drives are exactly synchronised and reach the upper limit position at
the same time.
For roller shutter applications, please use only the types of tubular drive designed for this purpose.
This type of tubular drive is designed for use in single systems (one drive per barrel).
The tubular drive must not be used in potentially explosive areas.
The connecting cable is not suitable for transporting the drive. Always carry the drive by the housing tube.
Other applications, uses and modifications are not permitted in order to protect the safety of the users and others, since these ac-
tions can impair the system’s safety and carry the risk of personal injury and property damage. The drive manufacturer does not
accept liability for damages or injury arising from such actions.
Always observe the information in these instructions when operating or repairing the system. The drive manufacturer does not ac-
cept liability for damage or injury resulting from improper usage.
Assembling and disassembling the plug-in connecting cable
Caution
The power supply to the connecting cable must be disconnected prior to assembly/disas-
sembly.
Assembling the plug-in connecting cable
Ø35/Ø45/Ø58
Insert the
dead
connecting cable into the drive head until the
locating lug clicks into place in the drive. If necessary, use a
suitable flathead screwdriver to assist with insertion. Set the
screwdriver into one of the two plug grooves provided for this
purpose.
Check that the cable is properly engaged.
1 = locating lug
Disassembling the plug-in connecting cable for tubular drives
Ø35
Insert a suitable flathead screwdriver between the locating lug
and the snap-in pin, so that the snap-in pin releases the locat-
ing lug from the plug.
Now you can pull out the connecting cable along with the flat-
head screwdriver.
1.
2.
3.
A
A = snap-in pin
6 - en
Содержание C16
Страница 21: ...Declaration of conformity 21 en ...
Страница 22: ...22 ...
Страница 23: ...23 ...
Страница 24: ......