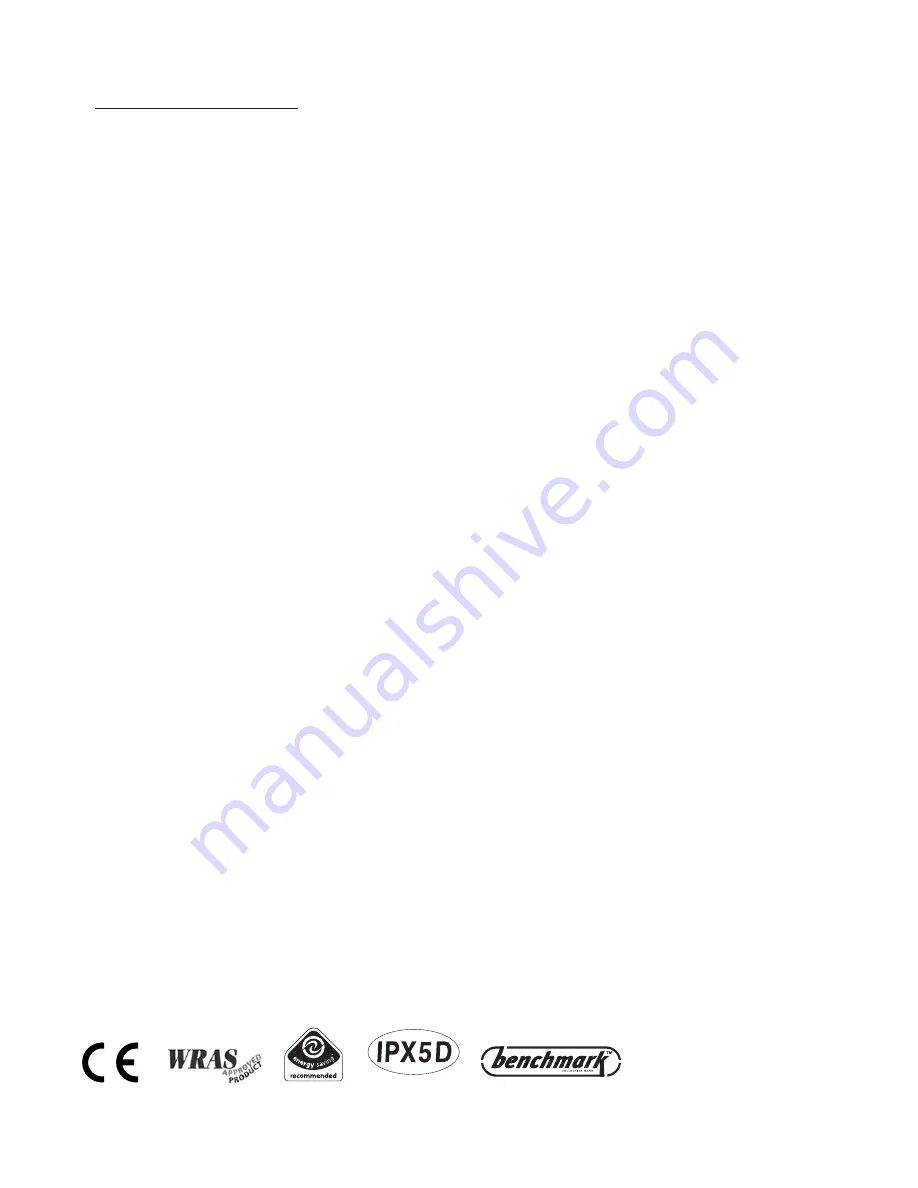
2
© Baxi Heating UK Ltd 2008
Propane
Baxi Duo-tec Combi 28 HE LPG
G.C.N
o
47 075 39
Building Regulations and the Benchmark Commissioning
Checklist
Building Regulations (England & Wales) require notification of
the installation of a heating appliance to the relevant Local
Authority Building Control Department. From 1 April 2005 this
can be achieved via a Competent Persons Self Certification
Scheme as an option to notifying the Local Authority directly.
Similar arrangements will follow for Scotland and will apply in
Northern Ireland from 1 January 2006.
CORGI operate a Self Certification Scheme for gas heating
appliances.
These arrangements represent a change from the situation
whereby compliance with Building Regulations was accepted as
being demonstrated by completion of the Benchmark Logbook
(which was then left on site with the customer).
With the introduction of Self Certification Schemes, the
Benchmark Logbook is being withdrawn. However, a similar
document in the form of a commissioning checklist and service
interval record is incorporated at the back of these instructions.
This company is a member of the Benchmark initiative and fully
supports the aims of the programme. Its aim is to improve the
standards of installation and commissioning of central heating
systems in the UK and to encourage the regular servicing of all
central heating systems to ensure safety and efficiency.
Building Regulations require that installations should comply
with manufacturer's instructions. It is therefore important that
the commissioning checklist is completed by the installer. The
relevant section of Building Regulations only relates to
dwellings. Therefore the checklist only applies if the appliance is
being installed in a dwelling or some related structure.
The flowchart opposite gives guidance for installers on the
process necessary to ensure compliance with Building
Regulations.
Baxi Heating UK Ltd is a
BS-EN ISO 9001 Accredited Company
The code of practice for the installation,
commissioning & servicing of central
heating systems.
“Baxi” supports
© Baxi Heating UK Ltd 2008
All rights reserved. No part of this publication may
be reproduced or transmitted in any form or by any means, or stored in any
retrieval system of any nature (including in any database), in each case whether
electronic, mechanical, recording or otherwise, without the prior written
permission of the copyright owner, except for permitted fair dealing under
Copyrights, Designs and Patents Act 1988.
Applications for the copyright owner’s permission to reproduce or make other
use of any part of this publication should be made, giving details of the proposed
use, to the following address:
The Company Secretary, Baxi Heating UK Ltd, The Wyvern Business Park,
Stanier Way, Derby, DE21 6BF.
Full acknowledgement of author and source must be given.
WARNING:
Any person who does any unauthorised act in relation to a
copyright work may be liable to criminal prosecution and civil claims for damages.
This product has an energy rating (A) on a scale of A to G.
For more information see www.boilers.org.uk. This is a certification mark.
Содержание Duo-tec
Страница 56: ...56 19 0 Notes Baxi Heating UK Ltd 2008...
Страница 57: ...57 19 0 Notes Baxi Heating UK Ltd 2008...