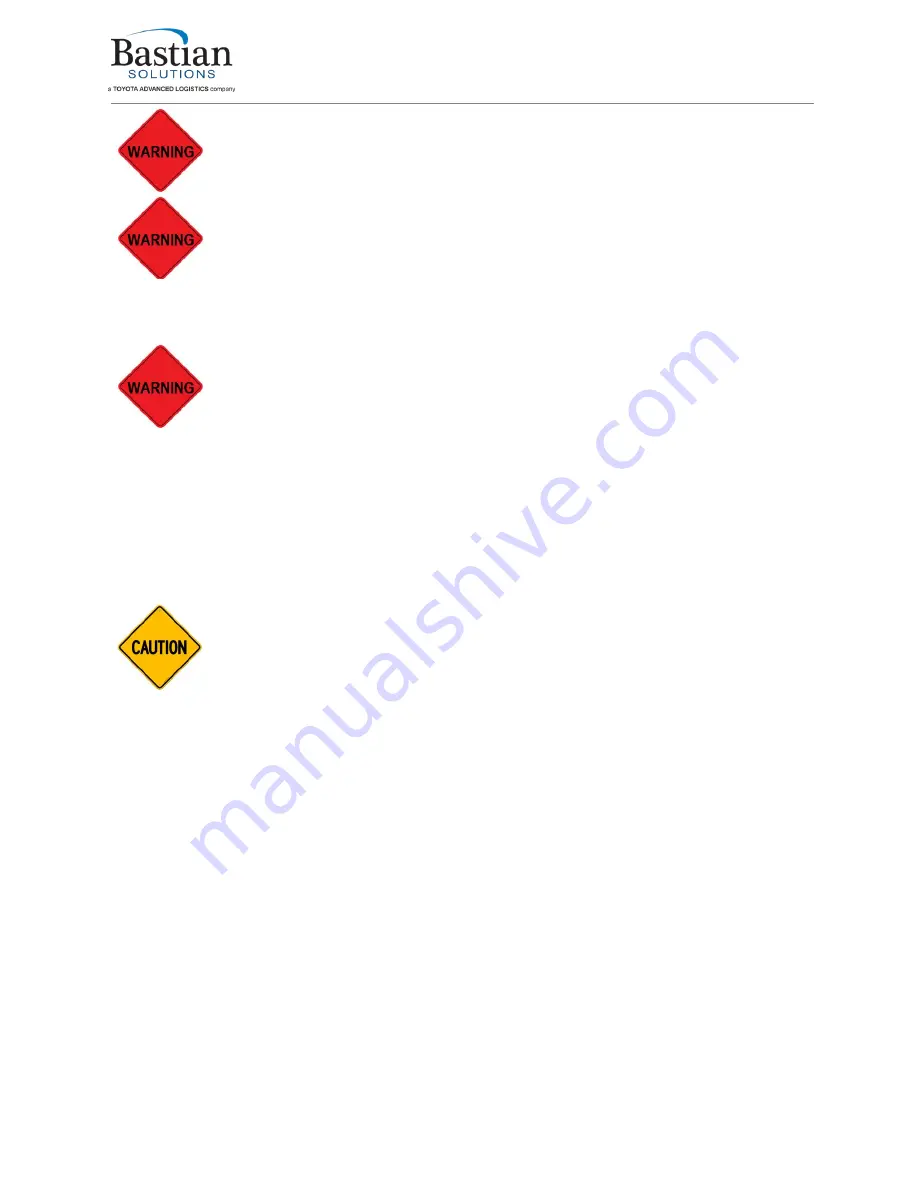
Installation and Maintenance Manual: RLVAC
Published February 2022
49
Only qualified electricians should connect or disconnect motor terminals. Incorrect
connection can cause hazardous voltages to be present on the outer case of the motor
or connected equipment, and can damage the motor or VFD.
For motors with VFDs, hazardous electrical power may be present for several minutes
after the supply is turned off and locked out, due to the VFD’s internal capacitors.
3. Remove the plastic dust cover, shaft fixing bolt, and shaft retaining washer in the end of the
motor’s hollow bore.
4. Support the motor from underneath.
Larger gearmotors are very heavy and will require mechanical assistance (e.g. a pump
cart) to remove and replace safely. Always use safe lifting practices and be cautious of
pinch points that can be created between the motor and its supports.
5. Loosen, but do not remove, the 1”-8 teardrop bolt. The underside cover nearest the motor may be
removed to gain access to the nut inside the drive section. See Figure 30: General Arrangement,
Belt Under Roller AC, Pneumatic Takeup Drive, Sheet 1 of 1 in Appendix 2: General
Arrangement Drawings for details.
6. Remove the shoulder bolt connecting the motor’s torque arm to the teardrop. The motor will have
a tendency to rotate around the shaft once this bolt is removed. Lift the teardrop out of the way so
it clears the motor’s torque arm.
7. Slide the motor off the drive shaft. If the motor does not slide freely, it may be binding because
the motor’s weight is not evenly supported.
Never hammer on the motor, gearbox, or shaft. Damage to the drive pulley bearings or
gearbox bearings can result.
8. Inspect the shaft and shaft key. File off any burrs, clean the shaft of any debris or corrosion, and
apply a good quality anti-seize compound to all exposed steel surfaces.
9. Orient the new motor’s key slot to match the key location in the shaft. For higher gear reductions,
this may require temporarily removing the rear cover to spin the motor fan by hand.
10. Slide the new motor onto the drive shaft. The new motor should slide freely; if it does not, find the
area that is binding and correct it. Forcing the motor in place will make it extremely difficult to
remove, and may cause damage to the drive shaft or gearbox bearings.
11. Reinstall the shoulder bolt in the new motor’s torque arm, and tighten the 1”-8 teardrop bolt to 200
ft-lbs. See Table 7: Fastener Standard Torque Values in section 6.3 for tightening torque of the
shoulder bolt.
12. Reinstall the shaft fixing hardware, ensuring that the threads are coated with anti-seize.
13. Reconnect the electrical connections, maintaining the phase rotation that was noted when
disconnecting the old motor. Review the winding diagram provided on the motor nameplate or
inside the junction box, to ensure the motor windings are set up for the correct voltage.
14. Replace any guards that were removed. Briefly start up the new motor to ensure it is running in
the correct direction.
6.6.2 Drive Pulley Replacement
1. Follow steps 2 through 7 of section 6.6.1 to remove the drive motor (63).