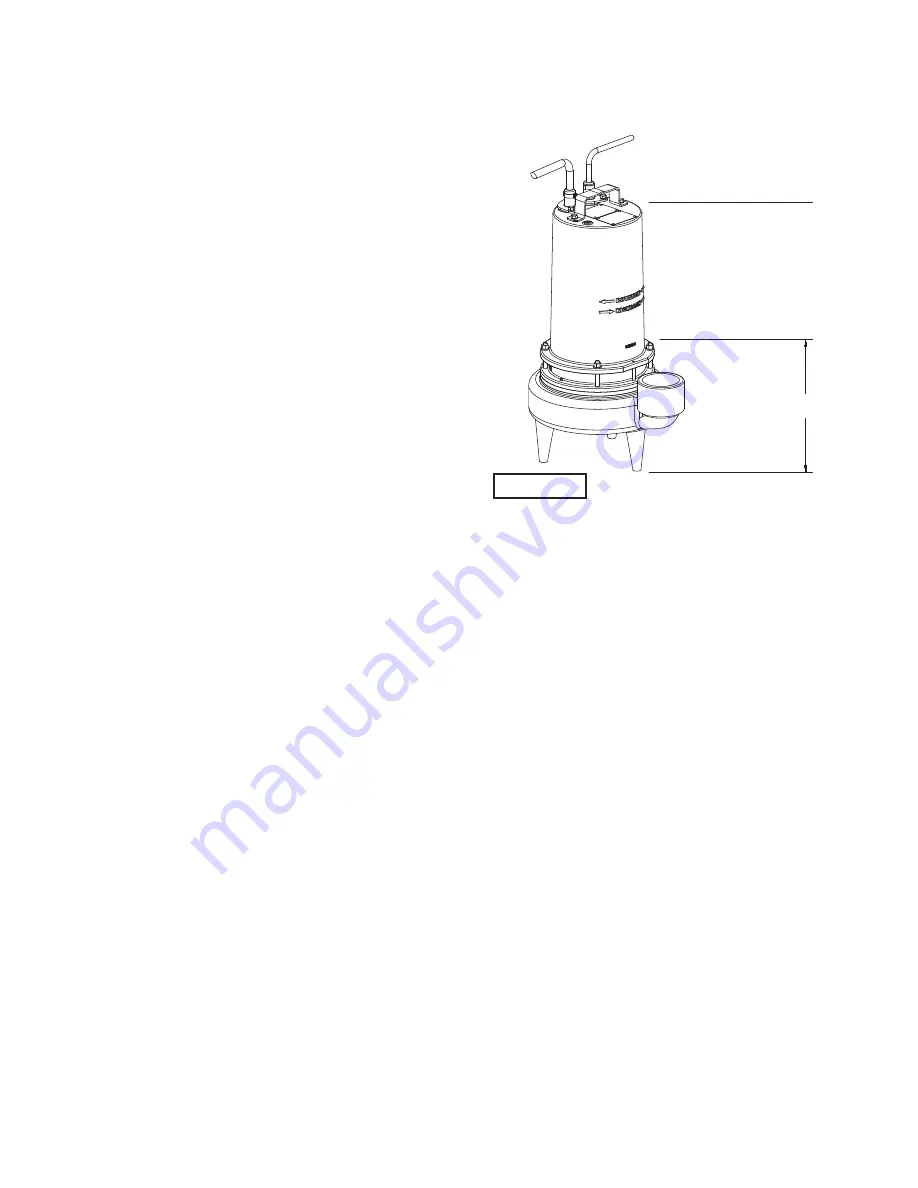
5
SECTION B: GENERAL INFORMATION
B-1) To the Purchaser:
Congratulations! You are the owner of one of the
fi
nest pumps
on the market today. CP&S pumps are products engineered
and manufactured of high quality components. Over one
hundred years of pump building experience along with a
continuing quality assurance program combine to produce a
pump which will stand up to the toughest applications. This
manual will provide helpful information concerning installation,
maintenance, and proper service guidelines.
B-2) Receiving:
Upon receiving the pump, it should be inspected for damage
or shortages. If damage has occurred,
fi
le a claim immediately
with the company that delivered the pump. If the manual
is removed from the packaging, do not lose or misplace.
B-3) Storage:
Short Term-
CP&S Pumps are manufactured for ef
fi
cient
performance following short inoperative periods in storage.
For best results, pumps can be retained in storage, as factory
assembled, in a dry atmosphere with constant temperatures
for up to six (6) months.
Long Term-
Any length of time exceeding six (6) months, but
not more than twenty-four (24) months. The unit should be
stored in a temperature controlled area, a roofed over walled
enclosure that provides protection from the elements (rain,
snow, wind-blown dust, etc.), and whose temperature can be
maintained b40°F and +120°F. (4.4 - 49°C).
Pump should be stored in its original shipping container.
On initial start up, rotate impeller by hand to assure seal
and impeller rotate freely. If it is required that the pump
be installed and tested before the long term storage
begins, such installation will be allowed provided:
1.) The pump is not installed under water for more than
one (1) month.
2.) Immediately upon satisfactory completion of the test,
the pump is removed, thoroughly dried, repacked in the
original shipping container, and placed in a temperature
controlled storage area.
B-4) Service Centers:
For the location of the nearest CP&S Service Center, check
your CP&S representative or Crane Pumps & Systems, Inc.,
Service Department in Piqua, Ohio, telephone (937) 778-8947
or Crane Pumps & Systems Canada, in Brampton, Ontario,
(905) 457-6223.
SECTION C: INSTALLATION
C-1) Location:
These pumping units are self-contained and are
recommended for use in a sump, lift station or basin. The
sump, lift station or basin shall be vented in accordance
with local plumbing codes. This pump is designed to pump
sewage, ef
fl
uent, or other nonexplosive or noncorrosive
wastewater. and shall
NOT
be installed in locations classi
fi
ed
as Class I Division 1 hazardous in accordance with the
National Electrical Code (NEC), ANSI/NFPA 70 or The
Canadian Electrical Code. Never install the pump in a trench,
ditch or hole with a dirt bottom; the legs will sink into the dirt
and the suction will become plugged.
C-1.1) Submergence:
It is recommended that the pump be operated in the
submerged condition and the sump liquid level should never
be less than dimension “A” in Figure 1.
C-2) Discharge:
Discharge piping should be as short as possible. Both a
check valve and a shut-off valve are recommended for each
pump being used. The check valve is used to prevent back-
fl
ow into the sump. Excessive back
fl
ow can cause
fl
ooding
and/or damage to the pump. The shut-off valve is used to
stop system
fl
ow during pump or check valve servicing.
CP&S Pumps supplies a breakaway
fi
tting discharge system
designed to allow the submersible wastewater pump to be
installed or removed without requiring personnel to enter the
wet well.
Place the Break Away Fitting (BAF) in position. Temporarily
secure the guide rails in the upper mounting brackets and
locate the base on the bottom of the wet well. Level the base
with grout and/or shims. Install the intermediate support
brackets, if required. Make sure the rails are in a true vertical
position so the pump will clear the access opening and
will slide freely down the rails into place on the discharge
stationary
fi
tting. Once the rails are in proper alignment, bolt
the base into the
fl
oor of the station and connect the discharge
pipe to the elbow.
Connect the movable portion and other supplied
fi
ttings of the
BAF onto the pump and lower into wet well. See the Break
Away Fitting manual for more information.
C-3) Liquid Level Controls:
The level controls are to be supported by a mounting bracket
that is attached to the sump wall, cover or junction box. Cord
grips are used to hold the cords in place on the mounting
bracket. The control level can be changed by loosening
the grip and adjusting the cord length as per the plans and
speci
fi
cations. Be certain that the level controls cannot hang up
or foul in it’s swing and that the pump is completely submerged
when the level control is in the “Off” mode.
A = 10.00"
(254)
BOTTOM OF FEET
MINIMUM
SUBMERGENCE
LEVEL
RECOMMENDED
SUBMERGENCE
LEVEL
FIGURE 1
Содержание 3SE3054DS
Страница 12: ...12 FIGURE 11 ...
Страница 20: ...20 Notes ...