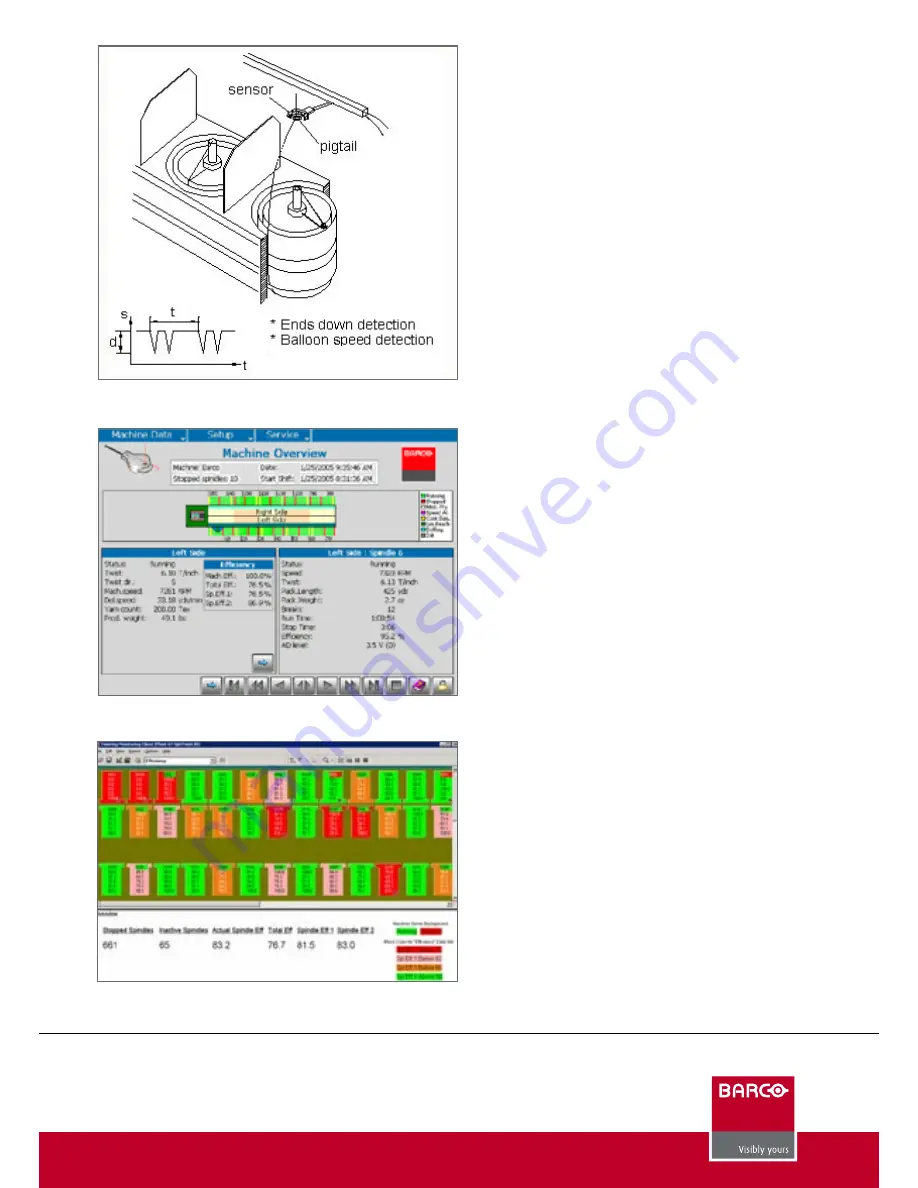
www.barco.com
Barco n.v.
Th. Sevenslaan 106
8500 Kortrijk
BELGIUM
Tel (intl) 32 56 26 26 11
Fax (intl) 32 56 26 26 90
e-mail: [email protected]
15/11/2006
BARCO SEDO GmbH
Neuwies 1
35794 Mengerskirchen
GERMANY
Tel (intl) 49 64 76310
Fax (intl) 49 64 763131
BARCO - Loepfe s.r.l.
Via El Alamein, 11/C
22100 Como
ITALY
Tel (intl) 39 031 3370457
Fax (intl) 39 031 305565
BarcoVision LTD
Capricorn Park
Blakewater Road
Blackburn, Lancashire BB1 5QR UK
Tel (intl) 44 1254 66 22 44
Fax (intl) 44 1254 58 25 95
BarcoVision LLC
4420 Taggart Creek Road
Suite 101
Charlotte, NC 28208 USA
Tel (intl) 1 704 392 93 71
Fax (intl) 1 704 399 55 88
Sensor: Principle of operation
The OptiTwist detector is mounted on the balloon thread guide
of the twisting machine. It consists of a photo receiver facing a
light emitting diode. During each revolution, the yarn balloon
interrupts the light beam twice.
The time between two consecutive interruptions serves as the
basis for the calculation of the balloon speed. In combination with
the delivery speed, this allows real time yarn twist monitoring
and length measurement. The time of each interruption and the
amount of light obstructed during the interruption serve as the
basis for the yarn diameter indication.
Sensor Control Unit (SCU
)
All sensors on one machine are connected to the SCU. This unit
offers a touch screen Windows-based user interface, USB inter-
face and Ethernet connection. The integrated OPC server allows
a PC to connect to the SCU via the “OptiTwist browser” allowing
remote operation and service. The standard screen on the SCU
shows a graphical machine view with color coded spindle status
and side by side machine details.
TwistMaster monitoring system
Through the OPC interface, all machines equipped with OptiTwist
can also be connected to the TwistMaster production monitoring
system. All connected twisters are shown in a color coded mill
lay-out. Machines with off-standard conditions are automati-
cally flagged.
Functionalities
- Real time yarn breakage detection
- Measurement of spindle and take up speed
- Accurate twist level calculation
- Flagging of spindles with off-standard twist level, with an
end down, with yarn defects
- Accurate length measurement
- User friendly interface for set-up and reporting
Benefits
- Prevention of waste by stopping off-quality spindles
- Improved and consistent quality level
- Increased efficiency
- Tracing of defective spindles
- Elimination of laboratory based sampling and stroboscope
checks
- Identification of motor and belt problems
- Suitable for all yarn counts
- Simple mounting and cabling
- Low power consumption
- No moving parts, resulting in limited maintenance