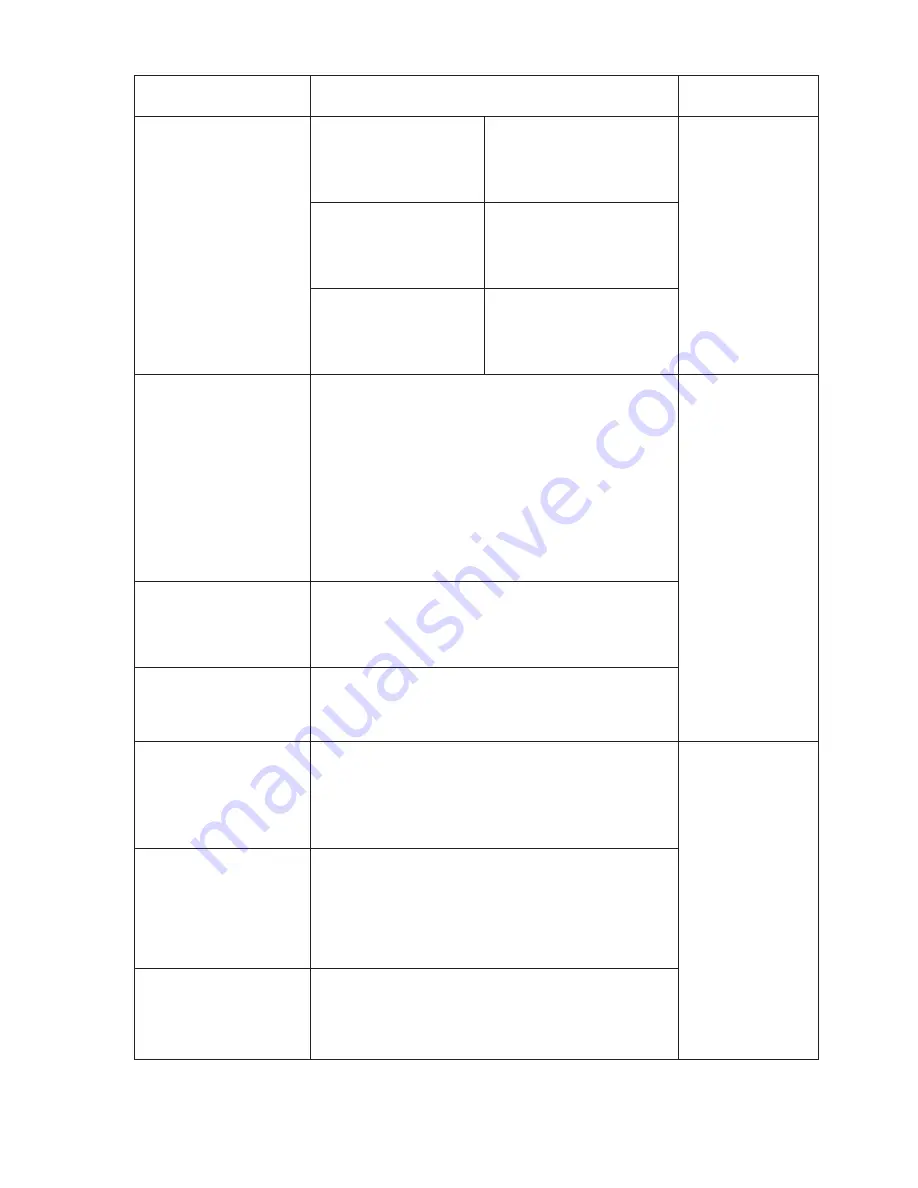
29
Troubles
Causes
Details
Generator running
not easy
Poor primary
ignition loop
Poor ignition coil
Poor contact of wire
or connector
Poor main switch
Refer to
“Ignition
System
Service’
Poor secondary
ignition loop
Poor ignition coil
Poor contact of wire
or connector
Poor main switch
Poor ignition
timing
Poor AC generator
coil
Poor fitting of stator
Poor CDI
Poor starting
Burnt fuse
Inadequate battery charging
Poor main switch
Poor starting motor switch
Poor switches of front brake and rear brake
Poor electric relay
Poor contact or breakage of wire
Poor starting motor
Refer to
“Electric
Starting
System
Service”
Feeble starting
motor
Inadequate battery charging
Poor contact of wire
Jamming of starting motor or pinion by
foreign matter
Engine refuses to
start with starting
motor running
Poor starting motor pinion
Reversed running of starting motor
Poor battery
No switching
between high beam
and low beam when
hightlight HI or LO
is operated
Poor or damaged electric bulb
Poor switching switch
Refer to
“ Lighting and
Signal System
Service”
Gasoline indicator
failure
Wire not mounted
Breakage of wire
Poor actuation of float
Poor gasoline gauge
Poor instrument
Fluctuation of
gasolin gauge
Loose wire bunch
Poor gasoline gauge
Poor instrument
Содержание BT49QT-28
Страница 1: ...BT49QT 28 MODEL SERVICE MANUAL ...
Страница 52: ...48 Ⅵ Ⅵ Ⅵ Ⅵ Circuit Diagram ...