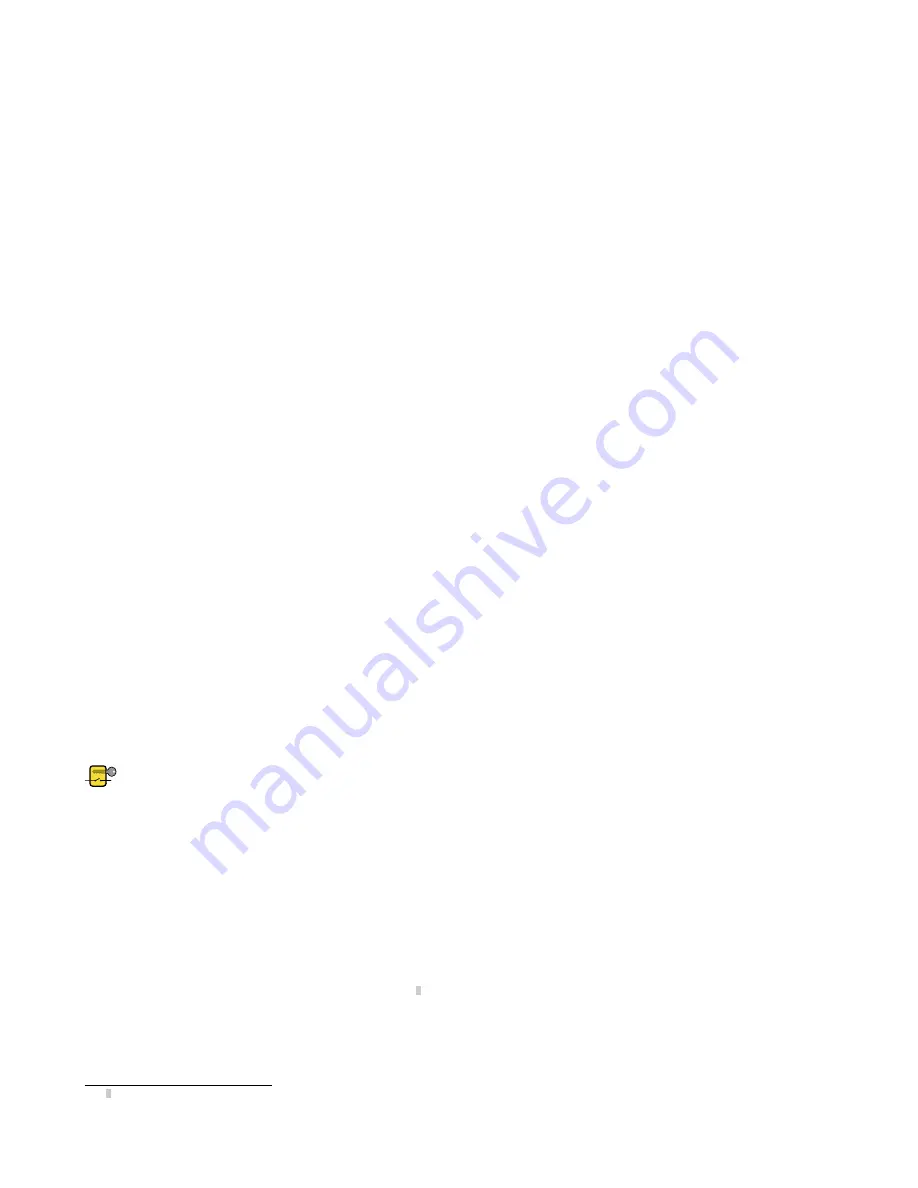
Photoelectric Sensors (Polarized Retroreflective Mode)
The user must ensure that false proxying (activation due to shiny or reflective surfaces) is not possible. Banner low profile
sensors with linear polarization can greatly reduce or eliminate this effect.
Use a sensor configured for light operate (LO or N.O.) if initiating a mute when the retroreflective target or tape is detected
(home position). Use a sensor configured for dark operate (DO or N.C.) when a blocked beam path initiates the muted
condition (entry/exit). Both situations must have open (non-conducting) output contacts in a power Off condition.
Positive-Opening Safety Switches
Two (or four) independent switches, each with a minimum of one closed safety contact to initiate the mute cycle, are
typically used. An application using a single switch with a single actuator and two closed contacts may result in an unsafe
situation.
Inductive Proximity Sensors
Typically, inductive proximity sensors are used to initiate a muted cycle when a metal surface is detected. Do not use two-
wire sensors due to excessive leakage current causing false On conditions. Use only three- or four-wire sensors that have
discrete PNP or hard-contact outputs that are separate from the input power.
Mute Device Requirements
The muting devices must, at a minimum, comply with the following requirements:
1. There must be a minimum of two independent hard-wired muting devices.
2. The muting devices must have one of the following: normally open contacts, PNP outputs (both of which must fulfill
the input requirements listed in the
Specifications and Requirements
on page 16), or a complementary switching
action. At least one of these contacts must close when the switch is actuated, and must open (or not conduct) when
the switch is not actuated or is in a power-off state.
3. The activation of the inputs to the muting function must come from separate sources. These sources must be
mounted separately to prevent an unsafe muting condition resulting from misadjustment, misalignment, or a single
common mode failure, such as physical damage to the mounting surface. Only one of these sources may pass
through, or be affected by, a PLC or a similar device.
4. The muting devices must be installed so that they cannot be easily defeated or bypassed.
5. The muting devices must be mounted so that their physical position and alignment cannot be easily changed.
6. It must not be possible for environmental conditions, such as extreme airborne contamination, to initiate a mute
condition.
7. The muting devices must not be set to use any delay or other timing functions unless such functions are
accomplished so that no single component failure prevents the removal of the hazard, subsequent machine cycles
are prevented until the failure is corrected, and no hazard is created by extending the muted period.
7.5.11 Bypass Switch
The safety device bypass is a manually activated and temporary suspension of one or more safety input stop signals,
under supervisory control, when no immediate hazard is present. It is typically accomplished by selecting a bypass mode of
operation using a key switch to facilitate machine setup, web alignment/adjustments, robot teach, and process
troubleshooting.
Bypass switches can be mapped to one or more of the following safety input devices:
• Safety gate (interlocking) switches
• Optical sensors
• Two-Hand Controls
• Safety mats
• Protective stop
Requirements of Bypassing Safeguards
Requirements to bypass a safeguarding device include
5
:
• The bypass function must be temporary
• The means of selecting or enabling the bypass must be capable of being supervised
• Automatic machine operation must be prevented by limiting range of motion, speed, or power (used inch, jog, or
slow-speed modes). Bypass mode must not be used for production
5
This summary was compiled from sources including ANSI NFPA79, ANSI/RIA R15.06, ISO 13849-1, IEC60204-1, and ANSI B11.19.
XS/SC26-2 and SC10-2 Safety Controllers
www.bannerengineering.com - Tel: + 1 888 373 6767
39