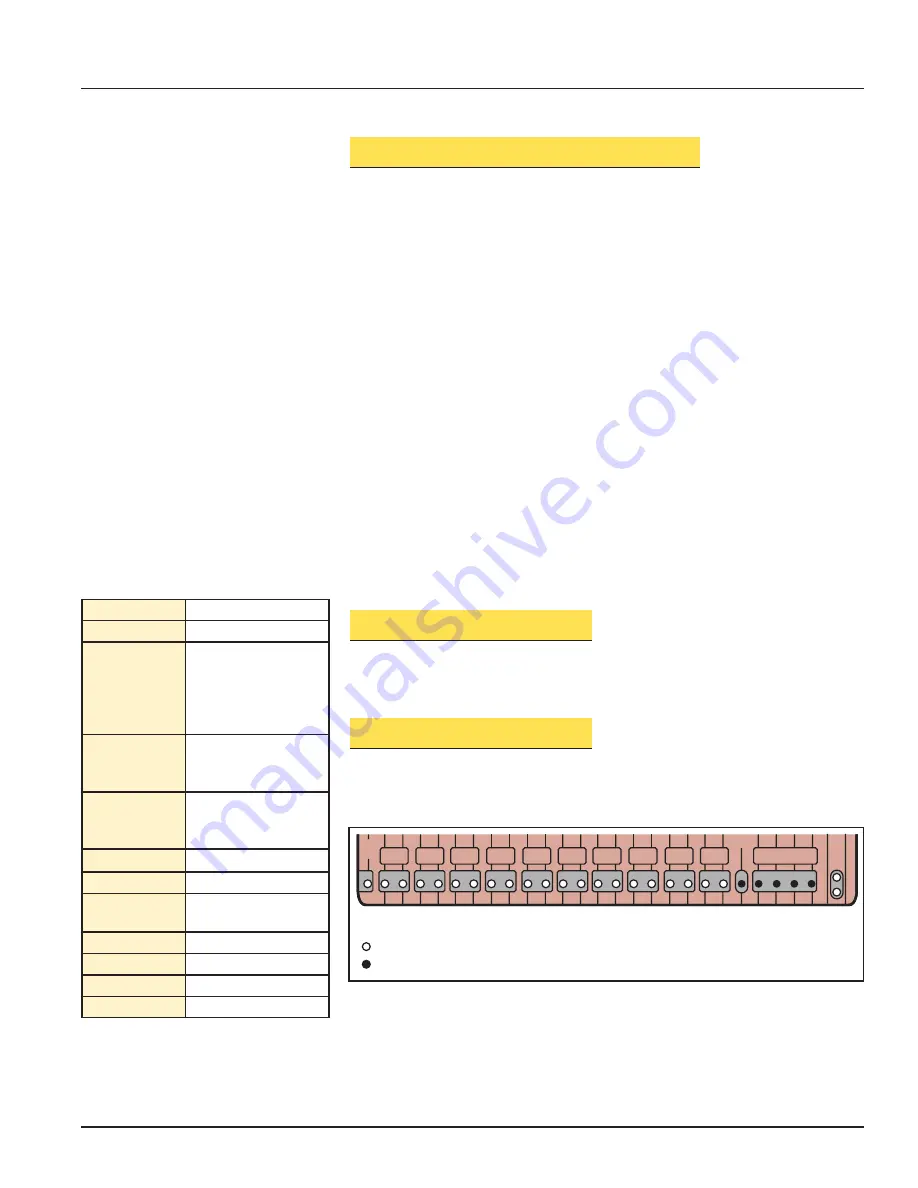
E-Stop Safety Module –
Model ES-TA-3F1
5.2 Periodic Checkout Requirements
The functioning of the Emergency Stop system (including the E-Stop Safety Module
and the guarded machine) must be verified on a regular periodic basis to ensure proper
operation (see also the machine manufacturer’s recommendations).
Procedure:
1) With the machine running, activate one Emergency Stop switch (open its
contacts). Verify that the machine stops. (The K1 and K2 indicators should turn
OFF simultaneously. If either indicator does not go OFF, check the E-stop
indicators. The indicators for the activated Emergency Stop switch should be OFF,
as well as indicators for E-stops with higher numbers. For example, if E-stop #6 is
activated, the indicators for #6, #7, #8, #9 and #10 should all go OFF
simultaneously.) If all E-stop indicators are OK but either or both K1 and K2
indicators are ON, disconnect the input power and check all wiring. Repeat this
step after the cause of any problem has been corrected.
2) Return the Emergency Stop switch to its closed-contact position. Close and open
the Reset switch (if the controller is in Auto Reset mode, this action is not
necessary). The machine must not start at this point. Initiate the machine startup
procedure (per manufacturer’s instructions). Verify that the machine restarts in
correct sequence.
3) Repeat the above checkout procedure for each E-stop switch, individually (ES1
through ES10).
5.3 Normal Operation
Following are examples of LED status indication and DeviceNet information for typical
E-Stop Safety Module RUN, STOP, and FAULT conditions.
5.3.1 RUN Condition
The following LED status represents a normal run condition, where all E-stop switches
are closed, and the E-Stop Module has been reset so that K1 and K2 output contacts
are closed:
ES4
A
B
ES3
A
B
ES2
A
B
ES1
24V
DC
+
PWR
A
B
ES5
A
B
ES6
RESET
A
B
MONITOR
1
2
3
K1
K2
4
ES8
A
B
ES7
A
B
ES9
A
B
ES10
A
B
Indicator Key
Indicator "ON"
Indicator "OFF"
Figure 7. Indicator status for normal RUN condition
Operating mode:
OK (Go)
E-stop Inputs:
All Closed
Monitor Inputs:
Mon 1 Open
(NOTE: unused,
jumpered monitor
contacts will not be
listed as open)
Reset Mode:
Manual Reset
(or Auto Reset,
depending on selection)
Reset Input:
- - - - - -
(or Disabled if in Auto
Reset mode)
K1 Relay:
Energized
K2 Relay:
Energized
Autobaud:
On (or Off, depending
on selection)
Fault Type:
No Fault
Action 1:
- - - - - -
Action 2:
- - - - - -
Action 3:
- - - - - -
A normal RUN condition is reported to
DeviceNet as follows:
Buy: www.ValinOnline.com | Phone 844-385-3099 | Email: [email protected]