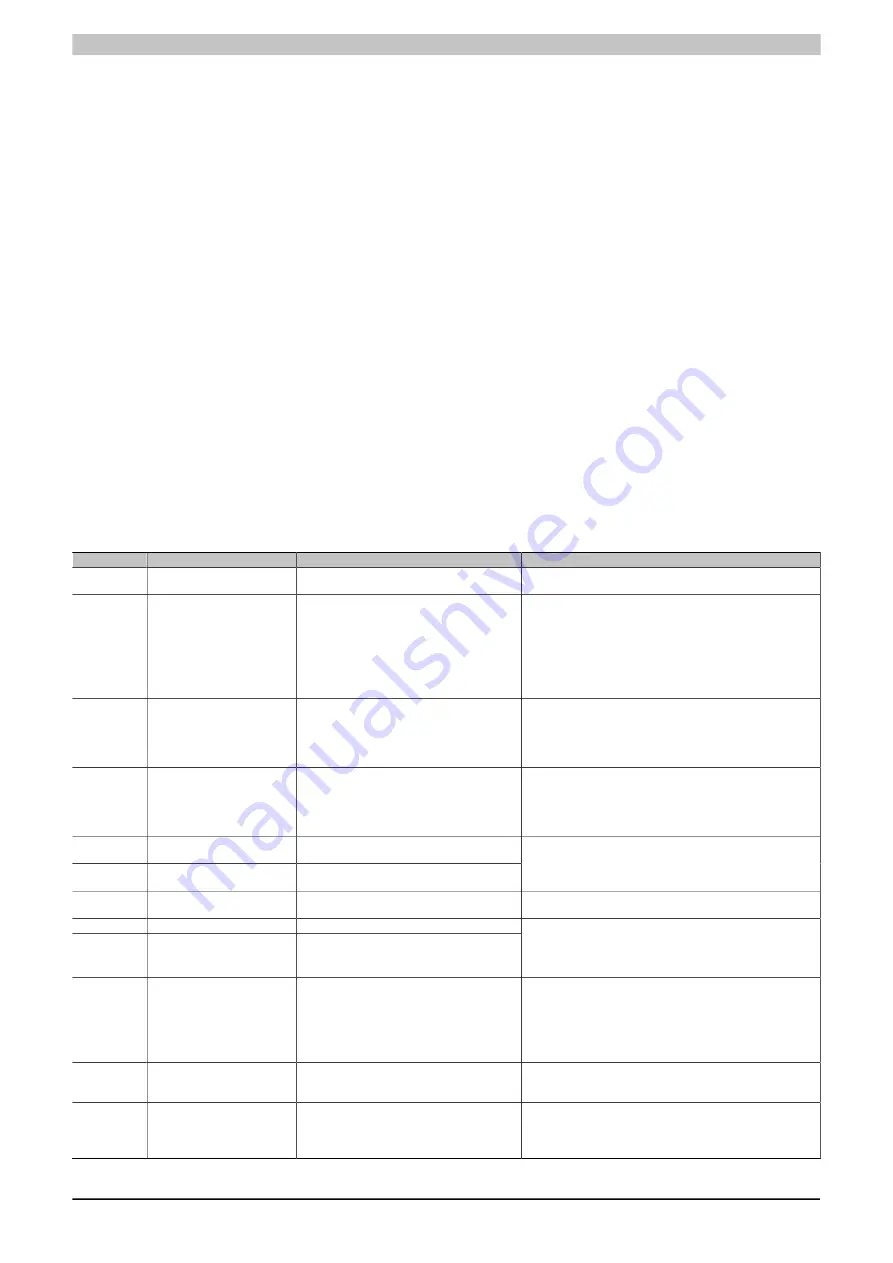
Programming guidelines
ACOPOSinverter P84 User's Manual 2.10
335
2.10 Fault - Causes - Measures
2.10.1 The inverter does not start and no error is displayed.
•
If the display does not light up, check the power supply to the inverter.
•
The assignment of the "Fast stop" or "Freewheel" functions will prevent the inverter starting if the corre-
sponding logic inputs are not powered up. The ACOPOSinverter P84 then displays
[freewheel stop]
(nSt)
on freewheel stop and
[fast stop]
(FSt)
for a fast stop. This is normal since these functions are active at
zero so that the inverter will be stopped safely if there is a wire break.
•
Make sure that the input or the inputs for run commands according to the selected control mode (parameter
[2/3 wire control]
(tCC)
and
[Type 2 wire control]
(tCt)
) is activated.
•
If an input of the function "limit switch" is assigned and is set to zero, then the inverter can only be started
with a run command for the opposite direction.
•
If the reference or command channel is assigned to a communication bus, when connecting the power
supply the inverter displays the message
[freewheel stop]
(nSt)
and remains in stop mode until the com-
munication bus sends a command.
2.10.2 Faults that do not allow automatic switch on again
The cause of the fault must be removed before resetting by turning off and then back on. The faults AnF, brF,
ECF, EnF, SOF, SPF and tnF can also be decentrally corrected via a logic input or control bit (parameter
[fault
reset]
(rSF)
).
The faults AnF, EnF, InFA, InFb, SOF, SPF and tnF can also be decentrally locked via a logic input and deleted
(parameter
[fault inhibit assign]
(InH)
).
Error
Name
Probable cause
Error correction
AI2F
[AI2 filter]
•
Inconsistency of the signal at the analog
input AI2
•
Check the wiring of analog input AI2 and the value of
the signal.
AnF
[Load slipping]
•
The actual speed of the encoder does
not match the reference
•
Check the motor, amplification and stability parameters.
•
Add a brake resistor.
•
Check the dimensioning of the motor/inverter/load.
•
Check the mechanical coupling of the encoder and its
wiring.
•
If the torque control is used, please observe the note
"TORQUE CONTROL (tOr-)" on page 256
.
bOF
[Overl. brake res.]
•
The braking resistor is under excessive
load.
•
Check the size of the resistance and allow it to cool
down.
•
Check the parameters
[brake resistor power]
(brP)
and
[brake resistor value]
(brU)
.
brF
[Brake contact]
•
The brake feedback contact does not
match the brake logic control.
•
The brake does not stop the motor
quickly enough (detected by measuring
the speed on the impulse input).
•
Check the feedback circuit and the brake logic control
circuit
•
Check the mechanical state of the brake.
•
Check the state of the brake linings.
CrF1
[Precharge]
•
Charging relay control fault or charging
resistor damaged
CrF2
[Thyr. soft charge]
•
Fault when charging the DC bus (thyris-
tors)
•
Switch the inverter off and on again.
•
Check the internal connections.
•
Examine and repair the inverter
ECF
[Mech Coupl Encoder]
•
Break in the mechanical coupling of the
encoder
•
Check the mechanical coupling of the encoder
EEF1
[Control Eeprom]
•
Internal memory fault, control card
EEF2
[Power Eeprom]
•
Internal memory fault, power card
•
Check the environment (electromagnetic compatibility).
•
Turn the device off and back on and reset it to factory
settings.
•
Examine and repair the inverter
EnF
[Encoder]
•
Encoder feedback fault
•
Check parameters
[number of pulses]
(PGI)
and
[En-
coder type]
(EnS)
.
•
Check the mechanical and electrical functions of the en-
coder, its power supply and connections.
•
Change the rotation direction of the motor (parameter
[Phase rotation]
(PHr)
) or the signals from the encoder.
FCF1
[Motor cont. closed]
•
The output contactor remains closed
although the opening conditions have
been met
•
Check the contactor and its wiring.
•
Check the feedback power path.
HdF
[IGBT desaturation]
•
Short-circuit or grounding at the inverter
output
•
Check the connection cables from the inverter to the mo-
tor and the insulation of the motor.
•
Run the diagnostic tests via the menu
[DIAGNOSIS]
.
Содержание ACOPOSinverter P84
Страница 2: ......
Страница 384: ...Accessories 384 ACOPOSinverter P84 User s Manual 2 10 8I0FT180 300 1 A Nm lb in 8I0FT180 300 1 25 221 3...
Страница 391: ...Accessories ACOPOSinverter P84 User s Manual 2 10 391 4 7 2 Installation 8I0XF084 020 1...
Страница 392: ...Accessories 392 ACOPOSinverter P84 User s Manual 2 10 8I0XF084 030 1...
Страница 393: ...Accessories ACOPOSinverter P84 User s Manual 2 10 393 8I0XF084 040 1...
Страница 394: ...Accessories 394 ACOPOSinverter P84 User s Manual 2 10 8I0XF084 050 1...
Страница 395: ...Accessories ACOPOSinverter P84 User s Manual 2 10 395 8I0XF084 0x0 1...
Страница 400: ...Accessories 400 ACOPOSinverter P84 User s Manual 2 10...