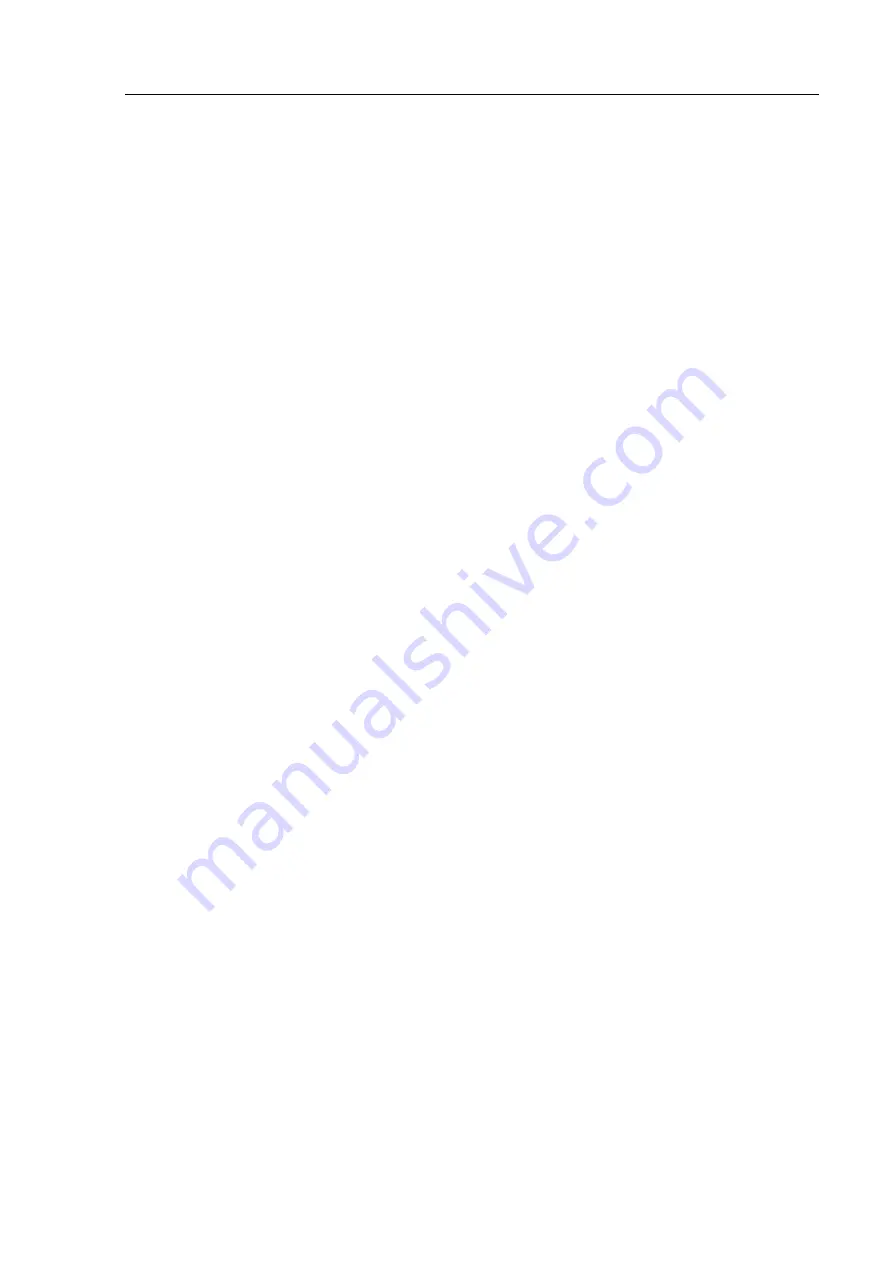
Light Weight Taut Wire Mk 14B Operation Manual
13
4.3
Winch System
The winch lower and hoist the depressor weight to and from the seabed.
The winch is powered by a electrical powered servomotor, and the
servo system is equipped with a fail-safe magnetic brake located
between the servomotor and the gear.
The system is automatically controlled and is operated by the amplifier
and the PLC.
Electrical power are from the vessel’s own supply.
A MDFRARS 132 Mx4 IP 66 Special Asynchron Servomotor, giving
84Nm at 2030 rpm/18 kW powers the winch drum. Max. moment is
168 Nm.
The SEW gear system (gear ratio 1:12) is bringing the maximum torque
up to 1200 Nm.
4.4
Tension Compensating System
The system activates the electrical powered servomotor whenever the
wire tension is deviating from the set-point in mooring mode.
Compensating cylinders air pressure is manually set and automatically
controlled by the pressure regulator. Actual pressure is indicated on the
manometer. Wire tension is directly related to the cylinder air pressure
i.e. increased pressure gives increased tension and visa versa.
Pressurised air is from the vessel’s own supply.
Wire tension is recorded by the load cells (2) located under the wire
angle compensator and visualized on a gauge located on the local
operating panel.
4.5
Control System
The hydraulic and winch drive systems are automatically controlled
and operated by a Telemecanique TSX Micro PLC system.
The local control panel, is situated on the taut wire cabinet R/H side
and has the following equipment
•
Main power switch
•
PLC terminal
•
Mooring indicator lamp
•
Mooring tension indicator (optional)
•
Joystick for manual hoisting and lowering