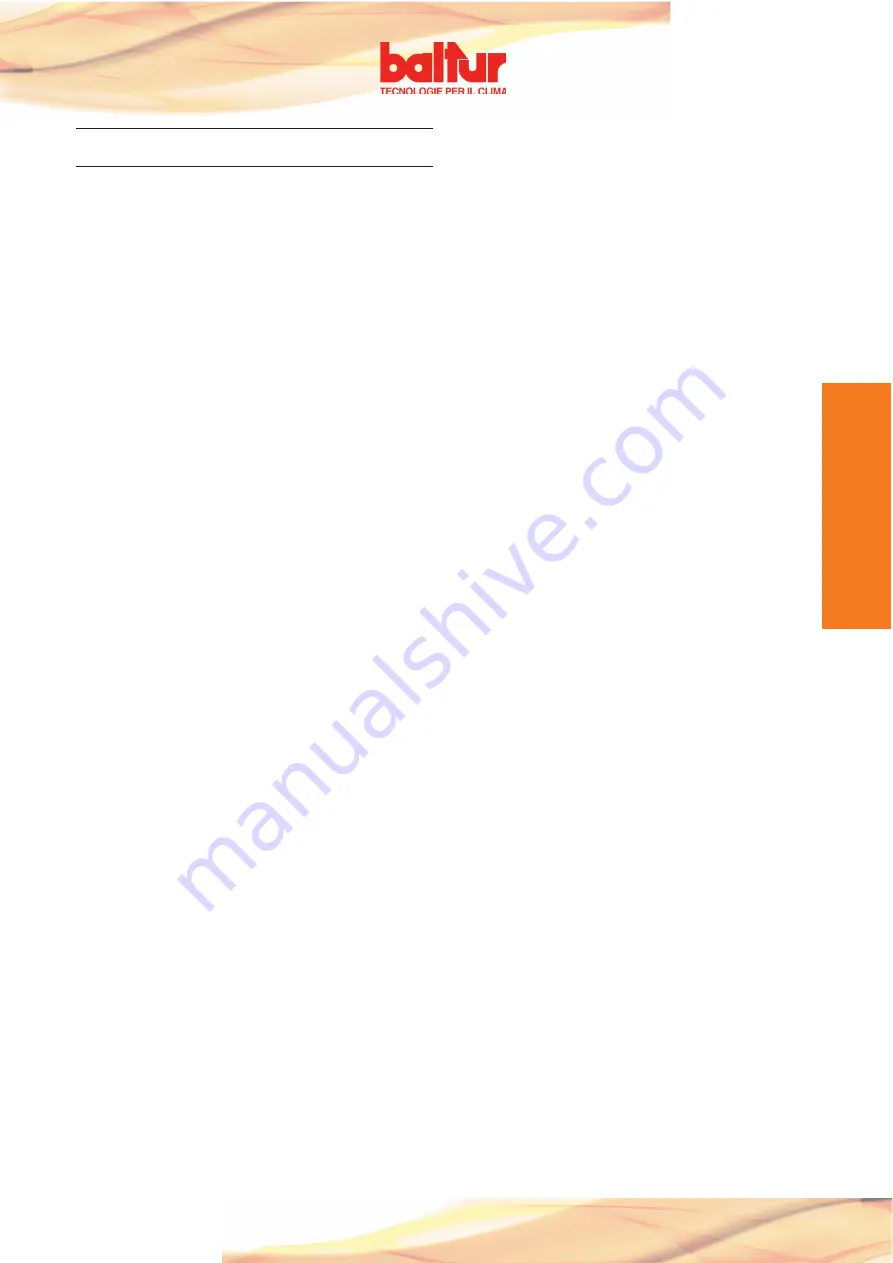
29 / 75
0006081327_200807
E
N
G
L
I
S
H
METHANE GAS IGNITION AND ADJUSTMENT
1) Check that the combustion head penetrates into the combustion
chamber to theextend required by the boiler manufacturer .
Check that the device that closes the air at the combustion head
is presumable in the position suited for the required supply of
fuel (the passage of air between the disk and combustion head
must be significantly reduced , if in the opposite case the fuel
supply is rather high, the passage between disk and combustion
head must be relatively open). See chapter “Adjustment of
combustion head”.
2) If it has not already been down when connecting the burner to the
gas piping, it is essentially to vent the air in the pipes, which should
done with doors and windows open. The connector on the piping
close to the burner must be opened and then the tap or taps that
shut off the gas must be opened a bit. Wait until you can smell the
gas and then close the tap. Wait a sufficient length of time, which
will depending on the specific conditions, until the gas in the room
disperses outside and then connect up the burner again to the gas
piping.
3) Check that there is water in the boiler and that the system’s
gate valves are open.
4) Check very thoroughly that the combustion products exhaust
path is free (boiler gates and flue open).
5) Check that current to be connected corresponds with that
required by the burner and that the electrical connections
(motor and main line) are set for the available power supply.
Check that all the electrical connections carried out on site
have been correctly performed as in our wiring diagram.
6) Apply a pressure gauge with suitable scale to the gas pressure
outlet to check the set value (if the pressure provided for permits
it is preferable to use a water column instrument and not use
those with pointers for modest pressures).
7) Put the air adjustment electric servo motor cams (see
instructions page.....) to the positions you presume are suitable
in proportion to the minimum and maximum modulation thermal
flow and to the ignition heat input.
8) Set the desired value for the ratio between the gas and
air pressures, following the pneumatic valves adjustment
instructions given in the manual provided with the gas train
installed
9) With the burner panel switch at the “O” position and the main
switch on, check, by manually closing the contactor, that the
motor turns in the correct direction, if necessary, swap around
the two power cables for the three-phase motor to invert the
direction of rotation.
10) Now switch on the control panel switch and turn the modulation
switches to MIN (minimum) and MAN (manual). The control
box is now powered up and the programmer sets the burner as
described in the chapter “description of working”.
Note: Preventilation is carried out with air open and so the
adjustment servo motor is switched on performs its complete
opening run up to the set “maximum”. Only when the adjustment
servo motor has returned to the “switch on” position will the control
box carry out its ignition program, switching on the transformer
and gas valves for ignition. Check during preventilation that the
pressure switch that controls air pressure in fact exchanges (from
the closed position where no pressure is detected it must pass to
the closed position with air pressure detection). If the air pressure
switch does not detect sufficient pressure (does not carry out the
exchange), the ignition transformer does not switch on and the
valves for the ignition flame also do not switch, with the result
that the control box goes to “lock-out”. It should be pointed out
that some “locking out” during this phase of first switch on can be
regarded as normal because the ramp valves piping will still have
some air in them and this must be eliminated before a stable flame
can be achieved. To “release” the lock press the “release” button.
On first switching on, repeated “lock outs” may occur due to:
a) The gas piping not being freed of the air sufficiently and so the
gas quantity is not enough to provide a stable flame.
b) The “lock-out” with flame on may be caused by flame instability
in ionisation area, due to incorrect air-gas mix. This can be
remedied by varying the quantity of air and/or gas until the
right ratio is found. The same problem may be caused by
incorrect air/gas distribution in the combustion head. This can
be remedied with the combustion head adjustment device by
closing or opening further the air passage between combustion
head and gas diffuser.
11) Set the burner at minimum thermal capacity of modulation
(air damper control servo motor at minimum), check the size and
appearance of the flame, making any necessary corrections.
To do this, follow the e instructions for the pneumatic valves.
Then carry out a meter reading check on the quantity of gas
supplied. If necessary adjust gas and combustion air supply
as described previously (points 7 and 8). Subsequently the
combustion is checked with the special instruments. For the
correct air-gas mix, the carbon dioxide level must be measured.
(C02) for the methane is at least 8% or O2=6% on minimum
burner supply up to a ideal value of 10% or 02= 3% for maximum
supply. It is essential to check, with a suitable instrument, that
the percentage of carbon monoxide (CO) present in the fumes
does not exceed the limit set by regulations at the time of
installation.”
12) After adjusting the burner to minimum thermal capacity, turn the
modulation switches to MAN (manual) and MAX (maximum).
The servo motor that regulates the air is put at “maximum” and
so also the gas supply reaches maximum thermal capacity. A
check must then be carried out on the quantity of gas supplied
(by reading the meter). With burner on at maximum existing
supply, the gas flow is measured as the difference between
the two readings at exactly one minute between one and the
other. Multiplying the value obtained by sixty you obtain the
flow in sixty minutes, i.e. per hour. Multiplying the supply per
hour (m3/h) for the gas calorific power you obtain the power
supply in kcal/h which must correspond to or be very near to
that required by the boiler (lowest calorific power for methane
= 8550 kcal/h). You must prevent the burner from continuing
to run if the flow is greater than the maximum permitted for
the boiler, to avoid possible damage to the boiler itself, and
so the burner should be stopped straight after the two meter
readings.
Содержание TBG 50LX PN
Страница 2: ......
Страница 21: ...34 75 0006081327_200807 E N G L I S H CAMS REGULATION SERVOMOTOR SQN 72 6A4A20 N 0002933651 rev 14 02 2007...
Страница 23: ...72 75 0006081327_200807...
Страница 24: ...73 75 0006081327_200807...
Страница 25: ...74 75 0006081327_200807...