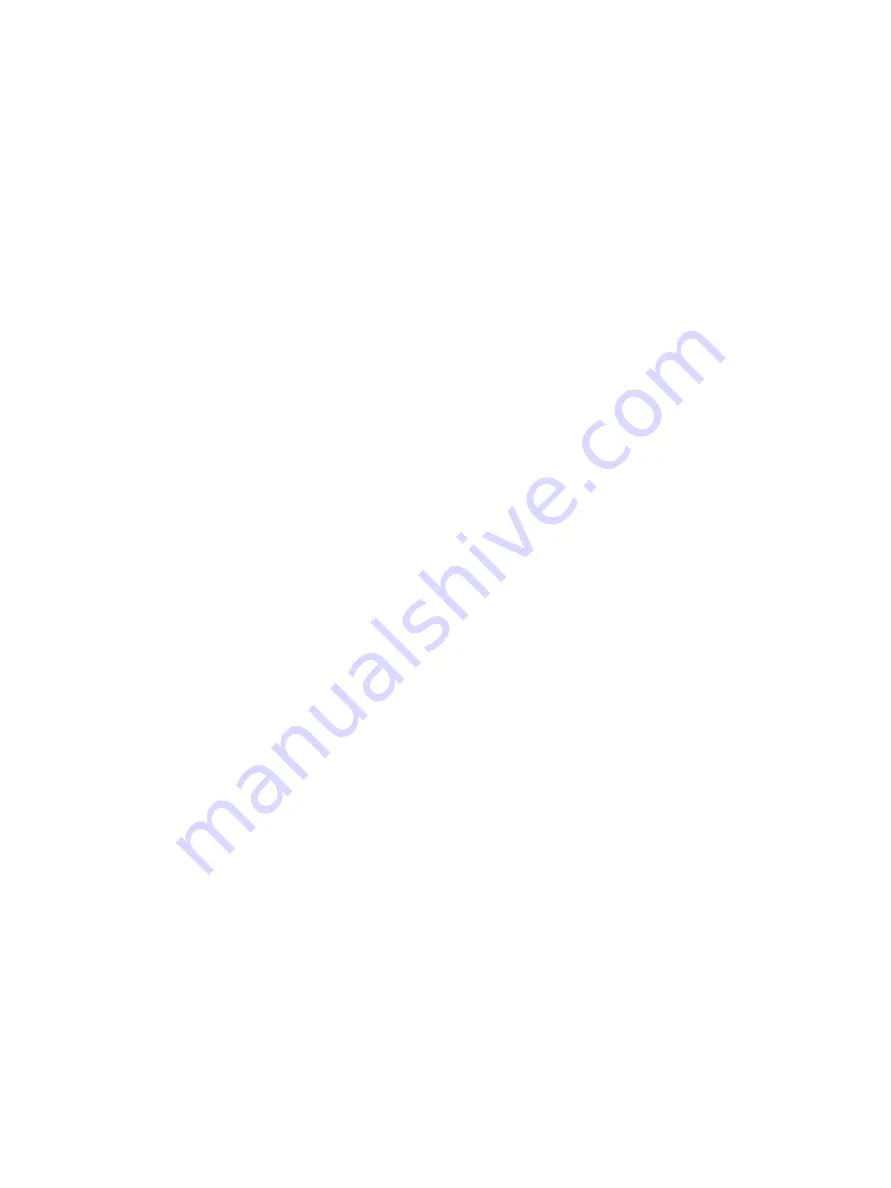
8 |
Baker Hughes
© 2020 Baker Hughes Company. All rights reserved.
IV. Warranty Information
Warranty Statement
- Baker Hughes warrants
that its products and work will meet all applicable
specifications and other specific product and work
requirements (including those of performance), if
any, and will be free from defects in material and
workmanship. Refer to Baker Hughes’s Standard
Terms of Sale, or specific contract for complete details
on warranty and limitation of remedy and liability.
Defective and nonconforming items must be held
for Baker Hughes’s inspection and returned to the
original F.O.B. point upon request.
Incorrect Selection or Misapplication of
Products
Baker Hughes cannot be responsible for
customer’s incorrect selection or misapplication of
our products.
Unauthorized Repair Work
- Baker Hughes has
not authorized any non-affiliated repair companies,
contractors or individuals to perform warranty repair
service on new products or field repaired products
of its manufacture. Therefore, customers contracting
such repair services from unauthorized sources must
do so at their own risk.
Unauthorized Removal of Seals
- All new valves and
valves repaired in the field by Field Service are sealed
to assure the customer of our guarantee against
defective workmanship. Unauthorized removal and/or
breakage of this seal will negate our warranty.
V. Valve Terminology for Safety Valves
(Paraphrased from ASME’s PTC 25)
•
Backpressure
Backpressure is the static pressure existing at the
outlet of a safety valve device due to pressure in
the discharge system.
•
Blowdown
Blowdown is the difference between actual popping
pressure of a safety valve and actual reseating
pressure expressed as a percentage of set
pressure, or in pressure units.
•
Bore Area
Bore area is the minimum cross-sectional area of
the seat bushing.
•
Bore Diameter
Bore diameter is the minimum diameter of the seat
bushing.
•
Built-Up Back Pressure
Pressure existing at the outlet of a safety valve
while it is open and flowing through a discharge
system.
•
Chatter
Chatter is abnormal, rapid reciprocating motion of
the moveable parts of a safety valve, in which the
disc contacts the seat.
•
Closing Pressure
Closing pressure is the value of decreasing
inlet static pressure at which the valve disc re-
establishes contact with the seat, or at which lift
becomes zero.
•
Disc
A disc is the pressure containing moveable
member of a safety valve which effects closure.
•
Inlet Size
Inlet size is the nominal pipe size of the inlet of a
safety valve, unless otherwise designated.
•
Leak Test Pressure
Leak test pressure is the specified inlet static
pressure at which a quantitative seat leakage
test is performed in accordance with a standard
procedure.
•
Lift
Lift is the actual travel of the disc away from closed
position when a valve is relieving.
•
Lifting Device
A lifting device is a device for manually opening a
safety valve, by the application of external force
to lessen the spring loading which holds the valve
closed.
•
Seat Bushing
A seat bushing is the pressure containing element
which constitutes the inlet flow passage and
includes the fixed portion of the seat closure.