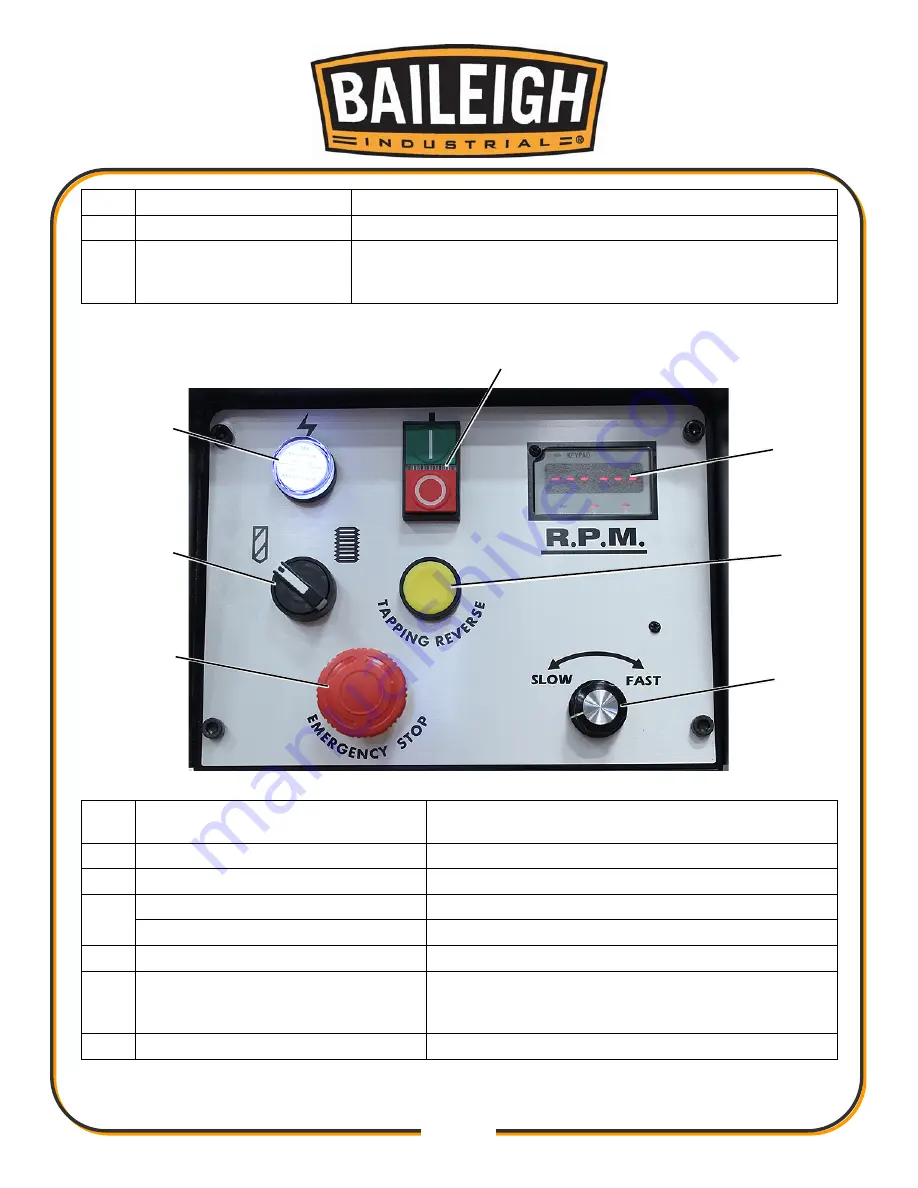
15
15
R
Limit Switch
Stops the machine if the guard is in an open position
S
Guard Adjustment Knob
Change guard height and lock with knob
T
Quill Spring Adjuster
GRASP FIRMLY. Pull out and rotate 90 at a time to
increase or decrease the spring tension on the quill
retractions spring.
AA
Emergency Stop Button
Stops all machine functions. Turn the switch
clockwise (cw) to reset the switch.
AB
Drilling / Tapping Selector Switch
Selects the mode of operation: drilling or tapping.
AC
Power Indicator Lamp
Illuminates when power is on at the control panel.
AD
Start Button (Top, Green)
Starts the spindle motor.
Stop Button (Bottom, Red)
Stops the spindle motor.
AE
Digital Indicator
Displays the rate of spindle rotation in RPM.
AF
Tapping Reverse Button
Manually reverses the spindle rotation for tapping
only. Normal operation will use the depth stop to
reverse the spindle during tapping.
AD
Spindle Speed Knob
Changes the speed of spindle rotation.
AC
AB
AA
AE
AG
AF
AD
Содержание DP-1200VS
Страница 15: ...13 13 GETTING TO KNOW YOUR MACHINE P B C M O N L D K J E F I G H A ...
Страница 23: ...21 21 ELECTRICAL DIAGRAM ...
Страница 30: ...28 28 HEAD CONTROL PARTS DIAGRAM ...
Страница 32: ...30 30 Item Description S19 Power Cord S20 Strain Relief S21 Relay 4p ...
Страница 33: ...31 31 LOWER HEAD PARTS DIAGRAM ...
Страница 36: ...34 34 BASE AND TABLE PARTS DIAGRAM ...