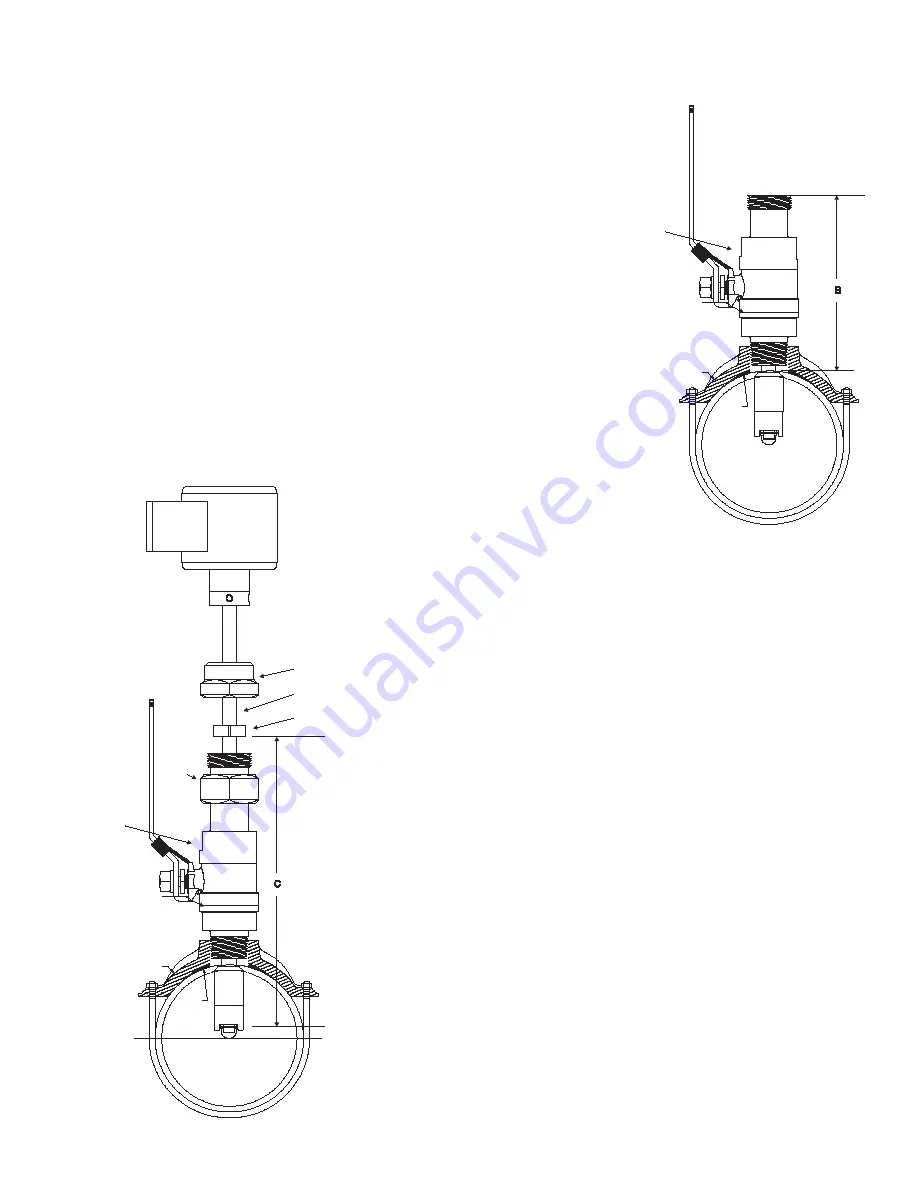
88
9
The preferred method of installation is by means of a saddle with 1” NPT out
-
let. On steel pipelines a weld-on type fitting may be substituted.
1. Attach the saddle to a section of pipe that has at least 10 diameters of
straight pipe ahead and five diameters of straight pipe behind the saddle.
2. Remove the sensor assembly from the mounting/isolation valve by
loosening the hex cap over the stem collar and the cover to the mounting/
isolation valve and detaching the assembly. Set aside taking care not to
damage impeller/shaft assembly.
3. Attach the pipe thread end of the valve to the saddle using a pipe joint
compound and tighten the joint.
Do not apply sealing compound to the top
thread of the valve. It is sealed with an o-ring.
4. Attach the tapping adapter, Data Industrial part number A-1027 to the top
of the valve.
5. Any pipe tapping machine with a 1” pipe thread connection may be used.
Use a cutter appropriate for the pipe material being tapped.
6. Attach the tapping machine to
the tapping adapter. Ensure
that all connections and seals
are tight.
7. Slowly open the valve by
rotating the handle 90° and lower the cutter past the valve ball to
the pipe. Drill the 1” nominal hole according to the manufacturer’s
instructions. Withdraw the cutter past the valve ball, close the valve
and remove the tapping tool.
8. Remove the Data Industrial tapping adapter from the top of the
valve.
9. The sensor rotor assembly is to be located a fixed distance from the
center of the pipe. To position the impeller at this depth, a reference
measurement for the pipe size and schedule is used. Look up the
pipe size and schedule number in
Table A
and note the reference
number. Next, measure from the outside wall of the pipe to the top
of the ball valve “B” in Figure 8. Add this number to the reference
measurement.
The resulting number is the distance from the recess of the sensor
tip to the bottom of the stem collar “C” in Figure 9. Insert the metal
tab of a tape measure into the recess of the flow sensor tip. Extend
the tape up the stem and mark the shaft with a pencil. Slide the
collar along the shaft until its bottom surface is at the mark on the
stem. Tighten the cap screw on the collar. When the sensor is
reassembled, this will set the insertion depth of the sensor.
Pipe Saddle
(ref.)
Gasket
(ref)
Ball Valve
Stem Collar
Stem
Hex Cap
Cover
Pipe Saddle
(ref.)
Gasket
(ref)
Ball Valve
Содержание SDI Series
Страница 2: ...2 2 This page intentionally left blank ...
Страница 26: ...26 26 This page intentionally left blank ...
Страница 27: ...27 This page intentionally left blank ...