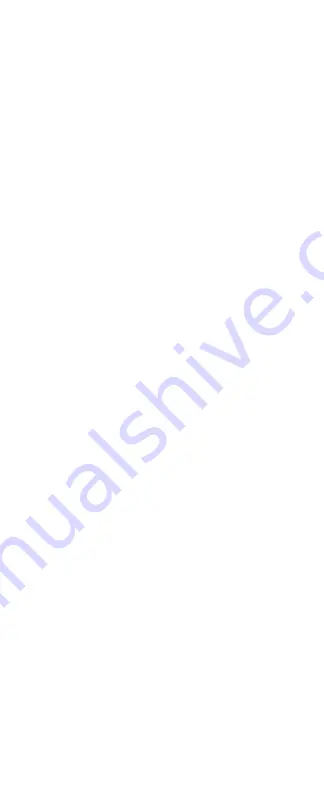
red LOW LED will go out and the green
OK LED will briefly glow. This indicates
the sensor’s heat/sensitivity is adjusted
for optimum performance.
If the red LOW LED remains on when
you briefly touch the bottle, the sensor
heat is set too low and the Heater
Adjustment must be turned slightly
clockwise. Allow unit to stabilize about
one minute and retest. Repeat this pro-
cedure until the green OK LED briefly
glows.
If the red HIGH LED glows, the heat is
set too high and the Heater Adjustment
should be turned slightly counterclock-
wise. Allow the unit to stabilize and then
repeat the test. Continue this procedure
until the proper green OK LED indication
has been achieved.
NOTES:
A. After initial check for correct adjustment,
disregard the LOW / OK / HIGH LEDs. Their
indication is meaningless during subsequent
leak testing activity.
B. Check for proper heat adjustment the first
time the unit is turned on and repeat on a daily
basis. This assures the product is calibrated
for the correct sensitivity in all leak size switch
positions for your daily test activity.
C. Frequency of sensor heat adjustment is a
function of how much exposure the sensor
has to refrigerant. Adjustment may be required
every couple of weeks for heavy duty service
and once every few months for light duty
service. The sensor LED status indicators will
accurately tell you when adjustment is neces-
sary during the daily check.
D. Over the usable sensor life, when heater
adjustment is fully clockwise and the green
OK LED will not come on, it is time to replace
the sensor. Before plugging in a new one,
turn the Heater Adjustment fully counter-
clockwise then plug in the new sensor and
test and adjust as described above to cali-
brate the instrument.