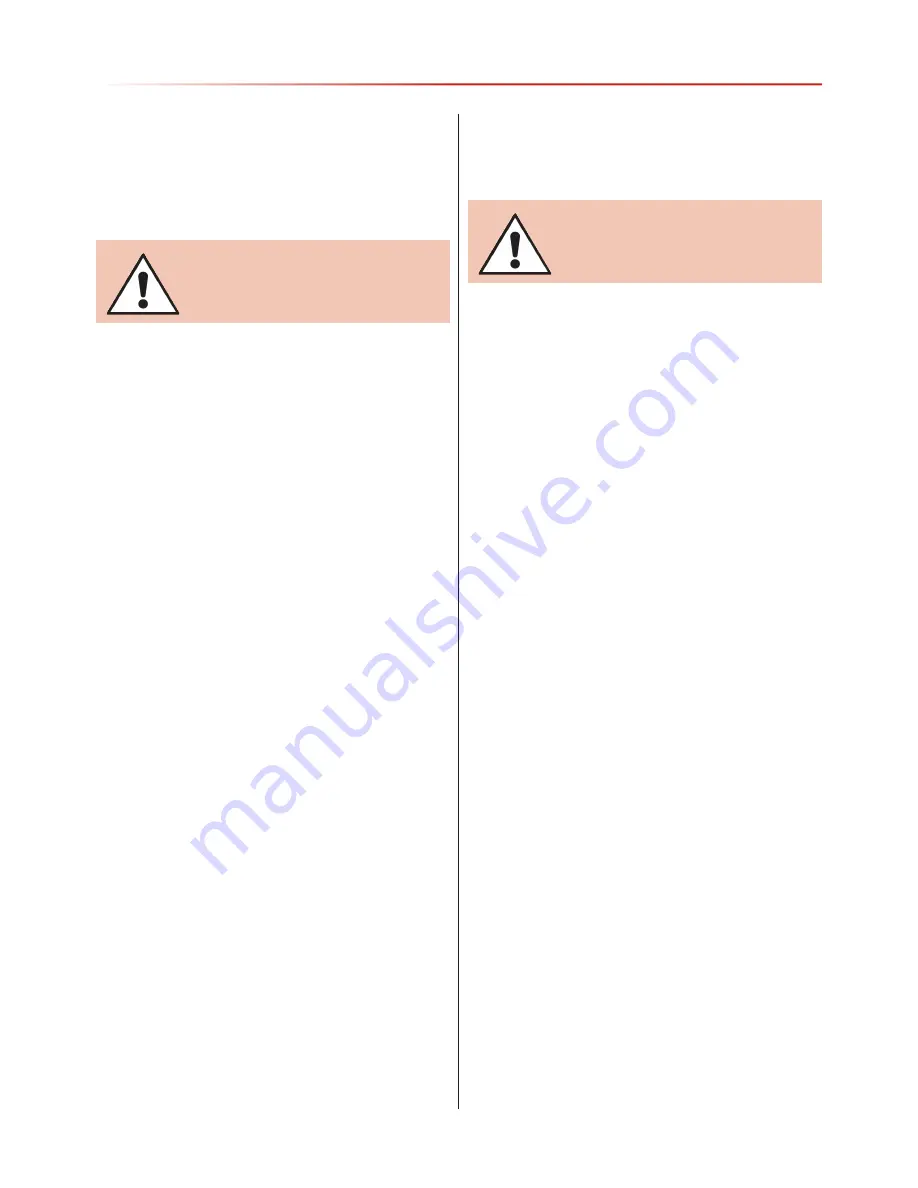
General Instructions for 230V Machines
5
Good Working Practices/Safety
Primary Precautions
Work Place/Environment
The following suggestions will enable you to observe
good working practices, keep yourself and fellow
workers safe and maintain your tools and equipment
in good working order.
WARNING! KEEP TOOLS AND
EQUIPMENT OUT OF THE
REACH OF YOUNG CHILDREN
UNDER NO CIRCUMSTANCES
SHOULD CHILDREN BE ALLOWED
IN WORK AREAS.
These machines are supplied with a moulded 13
Amp. plug and 3 core power cable. Before using the
machine inspect the cable and the plug to make
sure that neither are damaged. If any damage is
visible have the tool inspected/repaired by a suitably
qualified person. If it is necessary to replace the plug,
it is preferable to use an ‘unbreakable’ type that will
resist damage on site. Only use a 13 Amp plug and
make sure the cable clamp is tightened securely. Fuse
as required. If extension leads are to be used, carry
out the same safety checks on them and ensure that
they are correctly rated to safely supply the current
that is required for your machine.
Make sure when the machine is placed that it
sits firmly on the floor, that it does not rock and is
sufficiently clear of adjacent obstacles so that cutting
operations will not be impeded. Check you have
adequate clearance both in front of and behind the
machine when cutting long stuff. If you are liable to
be processing unwieldy or awkward work pieces, it is
suggested that you consider fastening the machine
down to the floor.
The machine is not designed for sub-aqua operation,
do not use when or where it is liable to get wet. If the
machine is set up in the open, and it starts to rain
(unusual though this would be in U.K.), cover it up or
move it into the dry. If the machine has got wet; dry
it off as soon as possible with a cloth or paper towel.
Do not use 230V a.c. powered machines anywhere
within a site area that is flooded or puddled and do
not trail extension cables across wet areas. Keep the
machines clean; it will enable you to more easily see
any damage that may have occurred. Clean the
machine with a damp soapy cloth if needs be, do
not use any solvents or cleaners, as these may cause
damage to any plastic parts or to the electrical
components. Keep the work area as uncluttered as is
practical, this includes personnel as well as material.
It is good practice to leave the machine unplugged
until work is about to commence, also make sure
to unplug the machine when it is not in use or
unattended. Always disconnect by pulling on the
plug body and not the cable. Once you are ready to
commence work, remove all tools used in the setting
operations (if any) and place safely out of the way.
Re-connect the machine.
Carry out a final “tightness” check e.g. guide fence,
table tilt, etc., check that the ‘cutting path’ (in this
case the path that the work piece will travel) is
unobstructed.
Make sure you are comfortable before you start
work; balanced, not reaching etc.
If the work you are carrying out is liable to generate
flying grit, dust or chips wear the appropriate safety
clothing, goggles, gloves, masks etc. If the work
operation appears to be excessively noisy, wear
ear-defenders. If you wear your hair in a long style,
wearing a cap, safety helmet, hair net, even a
sweatband, will minimise the possibility of your hair
being caught up in the rotating parts of the tool.
Likewise, consideration should be given to the
removal of rings and wristwatches, if these are liable
to be a ‘snag’ hazard. Consideration should also be
given to nonslip footwear, etc.
Do not work with cutting tools of any description
if you are tired, your attention is wandering or you
are being subjected to distraction. A deep cut, a lost
fingertip or worse; is not worth it!
Do not use this machine within the designated safety
areas of flammable liquid stores or in areas where
there may be volatile gases. There are very expensive,
very specialised machines for working in these areas,
THIS IS NOT ONE OF THEM.
Содержание 102266
Страница 1: ...Code 102266 AXMINSTER SERIES Hobby HBS200N 200mm Bandsaw AT M 24 04 2017 REF 102667...
Страница 4: ...What s Included 4 F C D M L K J H I G E Optional Mitre Fence Code 102919...
Страница 26: ...Parts Breakdown List 26 26...
Страница 29: ...Wiring Diagram 29 29...
Страница 30: ...CE Certificate 30 30...
Страница 31: ...Notes 31...