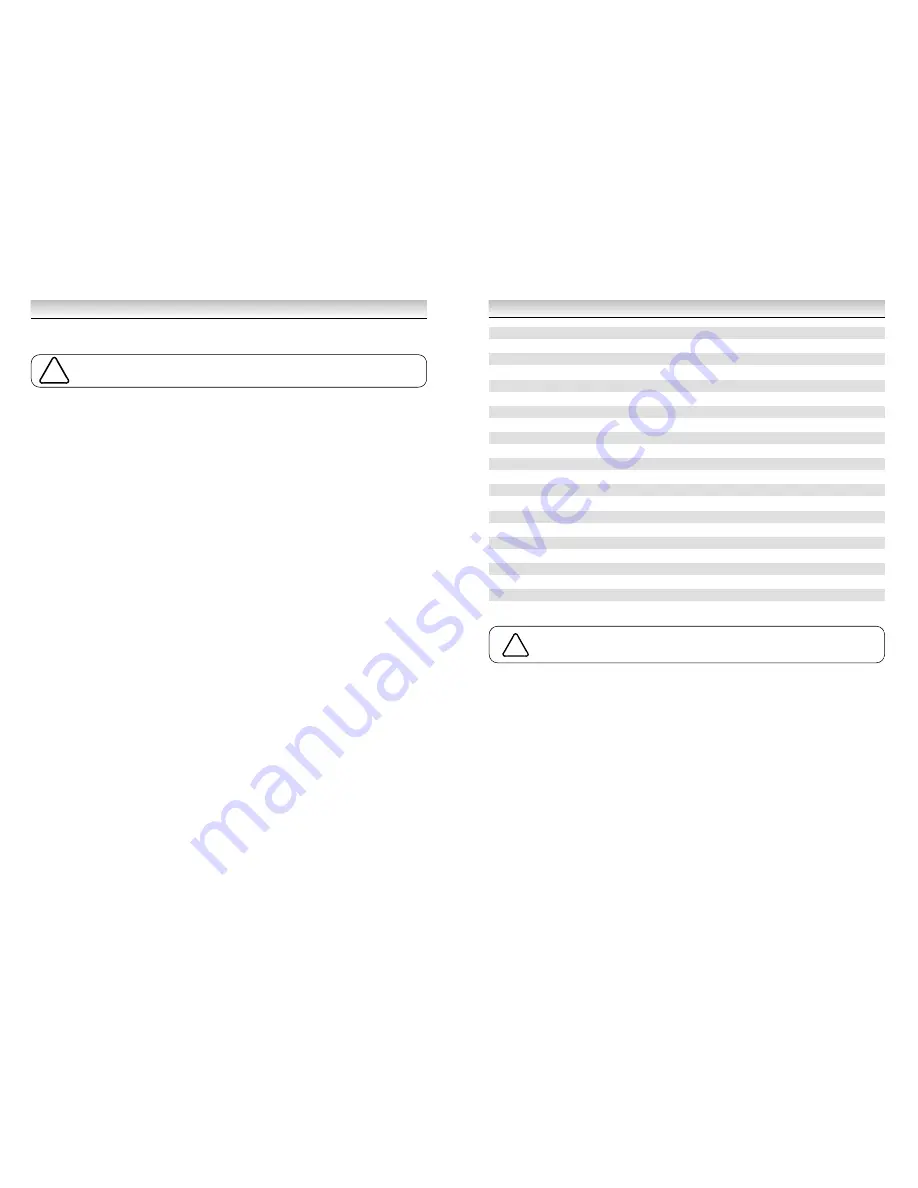
07
18
Specifications
Axminster No.
Metal Cutting Bandsaw
100090
Makers Number:
G4012
Motor:
230v 50Hz 550W
Blade Speeds:
20, 30, 50, M /min
Max cutting Capacities @ 90˚
Round Bar:
110mm diameter
Square Bar:
100mm x 150mm
Max Cutting Capacities @ 45˚
Round Bar:
70mm diameter
Square Bar:
85mm x 65mm
Blade Size:
1640L, 14 T.P.I., 0.65mm Thickness, 13mm Wide
Saw Body Swivel
0-45˚
Footprint:
915mm L x 575mm W x 1010mm H
Weight
70 Kgs
Noise level in accordance with DIN 45635
Offload:
> 60db(A)
Working:
60-65 db(A)
IT IS RECOMMENDED THAT YOU WEAR EAR PROTECTION
WHEN USING THIS MACHINE
!
Setting up the Machine
The machine has been set up in the factory. If, however, you think the settings may have been
moved due to a ’knock’ or whatever, proceed to set the machine up as follows:-
Disconnect the machine from the mains supply.
Remove the front cover by undoing the 5 off M4 caphead bolts, remove them and the shakeproof
washers, place carefully aside.
Clean the machine completely.
Withdraw the blade guide assemblies to their furthest extremes, (leaving the maximum expanse
of blade exposed.) Open up the drive belt and pulley cover and turning one of the pulleys move
the blade and check the teeth and the fabric of the blade, (no cracks etc.), if all seems ok, check
the blade is under reasonable tension, and reconnect the machine to the supply. Stand on the
side of the machine away from the open frame and start the machine.
Allow it to run up to speed. Once the saw is running, carefully move to the front left side of the
saw and check the blade is tracking correctly, i.e. more or less in the centre of the wheel, not too
far off the front of the wheel. If the blade is running too far to the front, adjust the tracking by
screwing ‘in’ the tracking control bolt (see fig 9a),only adjust in small increments and wait for it to
take affect. If the tracking is too far to the rear (scuffing against the rim) ‘unscrew’ the tracking
control bolt
NOTE
if you unscrew the bolt be prepared to ‘tighten the blade’ a touch. Once the
blade is running correctly, switch the machine off. Disconnect the machine from the mains
supply. Replace the front cover.
Pull the saw down, turn the swivel base against the preset stop and using a good square set
against the rear jaw of the vice, check the blade of the square lies along saw blade. If it is out of
square, adjust the position of the swivel base, by adjusting the preset stop, until the correct angle
is reached. Check that the base remains in position when the base clamp is tightened. Adjust the
index pointer.
Move the guide assemblies as close together as possible, leaving a small gap near the rear vice
jaw where you can stand a square. Stand the square on the floor of the vice with the blade of the
square up, check that the saw blade is vertical. The blades can be ‘twisted’ a little bit more, or
untwisted by loosening the main bolt that holds the bearing guide block onto the slides, moving
fractionally (there is only a small amount of ‘slop’ in the guide land and the groove between the
guide block assembly and the slide mechanism) and retightening.
Check the blade is pressed firmly between the two side rollers. If not, remove the safety cover
plates and adjust the rollers, by loosening the lock nuts (the top ones), and moving the bearing
using the eccentric cam profile (turn the bottom hexagons) of the mountings.
DO NOT PUSH
THE BLADE OUT OF LINE
by over adjusting (The blade should be in line with the groove in the
trust bearing). (See figs 9b & 9c)
When adjustment is complete re-tighten the lock nuts and replace the safety covers. Recheck
when everything is retightened. Reconnect the machine and run up to speed. Check everything
looks and sounds normal.
!