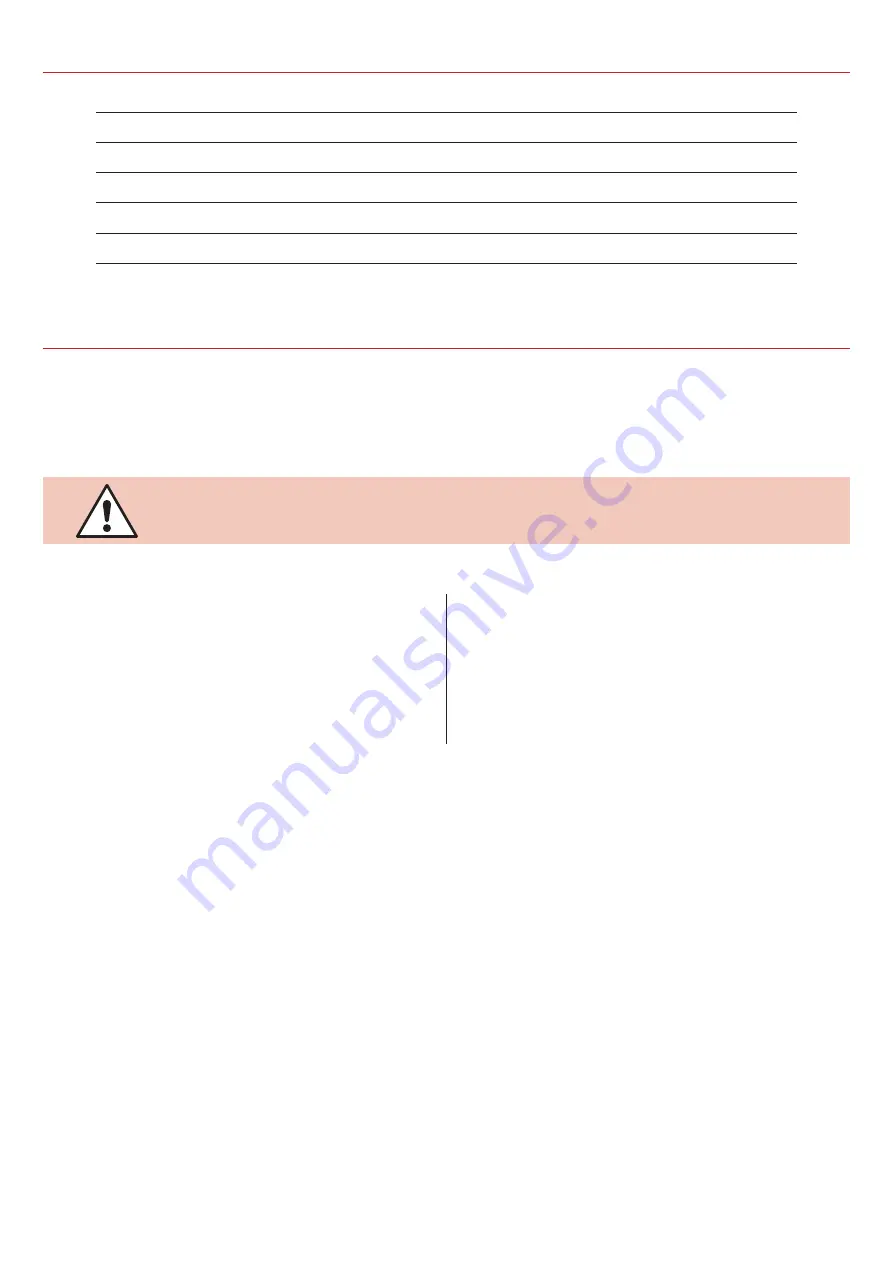
Parts index
General Instructions for 230V Machines
06
951539 10” and 12” Sliding Table kits ( Box 2 of 2)
Mitre Angle Rear Quadrant (with lift and shift handle)
Table Fence Mounting Casting
Mitre Angle Rip Fence
2 off: Height Adjusting Blocks
1 off: Distance Stop (with lift and shift handle)
42
43
44
45
46
The following suggestions will enable you to observe good working
practices, keep yourself and fellow workers safe and maintain your tools and equipment in good working order.
Good Working Practices/Safety
WARNING!
KEEP TOOLS AND EQUIPMENT OUT
OF THE REACH OF YOUNG CHILDREN
Primary Precautions
Primary Precautions
The machines are supplied with a moulded 16 Amp
plug (AW10BSB2) and 16 Amp plug (AW12BSB2) with a
3 core power cable. Before using the machine inspect
the cable and the plug to make sure that neither are
damaged. If any damage is visible, have the damaged
item inspected/repaired by a suitably qualified person.
If it is necessary to replace the plug, it is preferable to
use an ‘unbreakable’ type that will resist damage on
site. Only use a 16 Amp plug, (AW10BSB2) and 16 Amp
plug (AW12BSB2) and make sure the cable clamp is
tightened securely. Fuse as required. If extension leads
are to be used, carry out the same safety checks on
them, and ensure that they are correctly rated to safely
supply the current that is required for your machine.
The machine is not designed for sub-aqua operation, do not use when or where it is liable to get wet. If the
machine is to be used outside and it starts to rain, stop work and move it inside. If machine has got wet; dry it off
as soon as possible, with a cloth or paper towel.
DO NOT use 230V ac powered machines anywhere within a site area that is flooded or puddled, and do not trail
extension cables across wet areas.
KEEP the machine clean; it will enable you to more easily see any damage that may have occurred.
CLEAN the machine with a damp soapy cloth if needs be, do not use any solvents or cleaners, as these may
cause damage to any plastic parts or to the electrical components.
KEEP the work area as uncluttered as is practical, this includes personnel as well as material.
Содержание 501196
Страница 37: ...Wiring Diagram 37 ...
Страница 38: ...Parts Breakdown List 38 DIAGRAM A ...
Страница 40: ...Parts Breakdown List 40 DIAGRAM B Part 1 ...
Страница 41: ...Parts Breakdown List 41 DIAGRAM B Part 2 ...
Страница 44: ...Parts Breakdown List 44 DIAGRAM D ...
Страница 49: ...Notes 49 ...
Страница 50: ...Notes 50 ...
Страница 51: ...Notes 51 ...