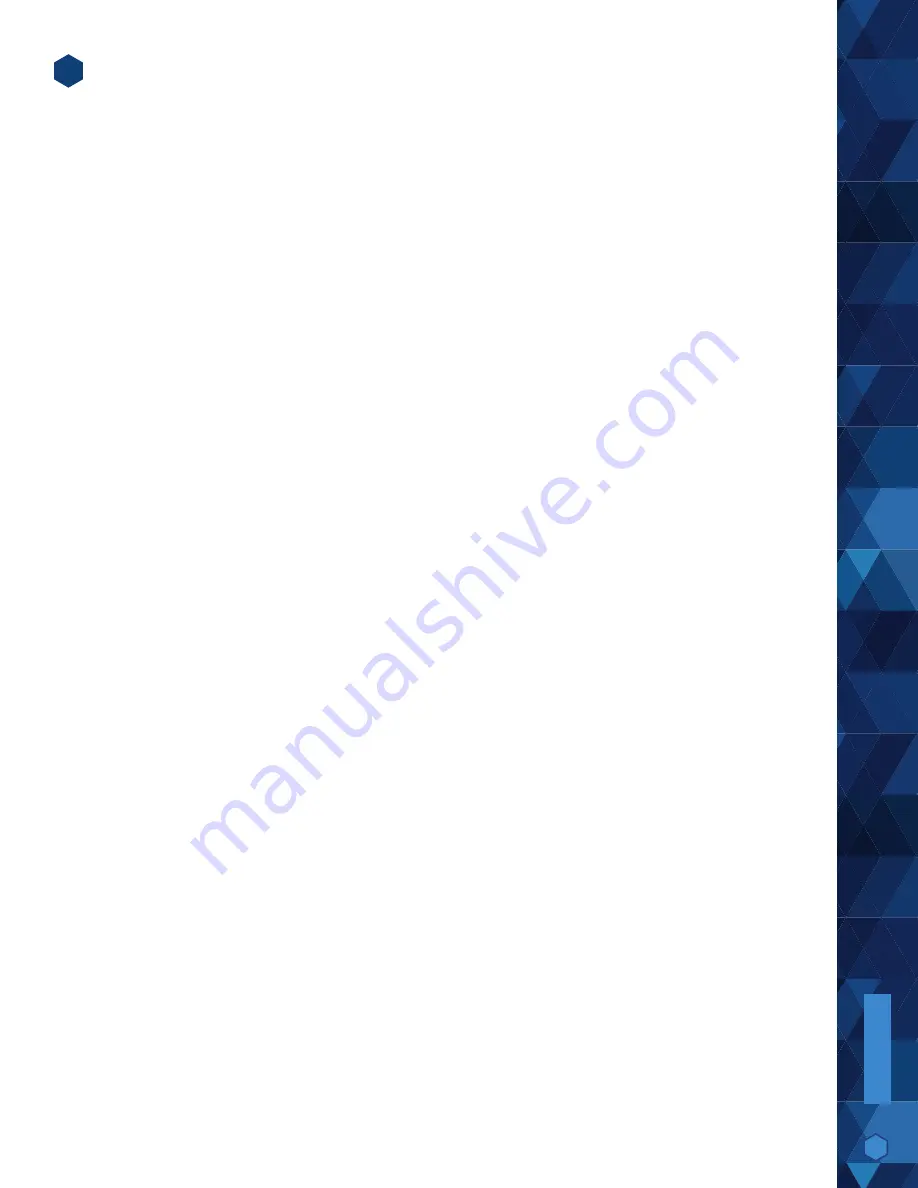
15
S
Y
S
TEM C
OMPONENT
S
PRIMAR
Y INSPECTION
INS
TALLA
TION
OPERA
TION
PRIMING
C
ONTR
OLLER
C
OMMISSIONING
REV03121080011217
MAINTENANCE
O
VER
VIEW
Maintenance
The SFM 1080 should be visually inspected and tested a minimum of every six (6) months according to the procedure below
during light duty cycles. Monthly inspections are recommended for systems that are being used in excess of an average of
eight (8) hours day and five (5) days a week.
Preventative Maintenance
Prior to performing the maintenance procedure ensure that:
1. The electrical sub-panel mounted main breaker is operating properly
2.
The user supplied circuit breaker is in the “OFF” position
3. All sources of power are isolated from the unit
Note: Proceed only after this has been verified and properly tagged.
•
Drain / remove visible water and sediment from strainer and fine filter/water separator
• Check enclosure and all parts for corrosion and rust
•
Check locking latches, door, and hinge operation
• Check cabinet mounting hardware - tighten as necessary
•
Check pump/motor hardware for tightness, as pump/motor hardware will loosen after normal operation due to vibration
• The hardware uses lock nuts - check all bolts for secure nuts
• Check all electrical terminals and connections for tightness
•
All motors are permanently lubricated and do not require any lubrication
•
All pumps are self-lubricating and do not require any maintenance
•
Check all plumbing joints for leaks, tightening fittings and joints as necessary, and remove accumulated fuel in drip tray
as necessary
•
Inspect all filters and separators
With breakers and power turned on again, and pump running, check all alarms for proper operation:
1.
Manually raise float switch located in drip/spill tray. Pump should immediately turn off and “LEAK DETECTION” should
illuminate. ALARM RESET by pushing the “ALARM RESET” button on the control panel.
2.
Slowly partially close inlet ball valve. At 12” HG, pump should turn off and “HIGH VACUUM ALARM” should illuminate.
Open inlet ball valve again. ALARM RESET by pushing the “ALARM RESET” button.
3.
Slowly partially close outlet ball valve. At 15 PSI, pump should turn off (after a delay of about one (1) second) and
“HIGH PRESSURE ALARM” should illuminate. Open outlet ball valve again. ALARM RESET by pushing the “ALARM
RESET” button.
Note: All filter elements should be replaced at least every six (6) months.