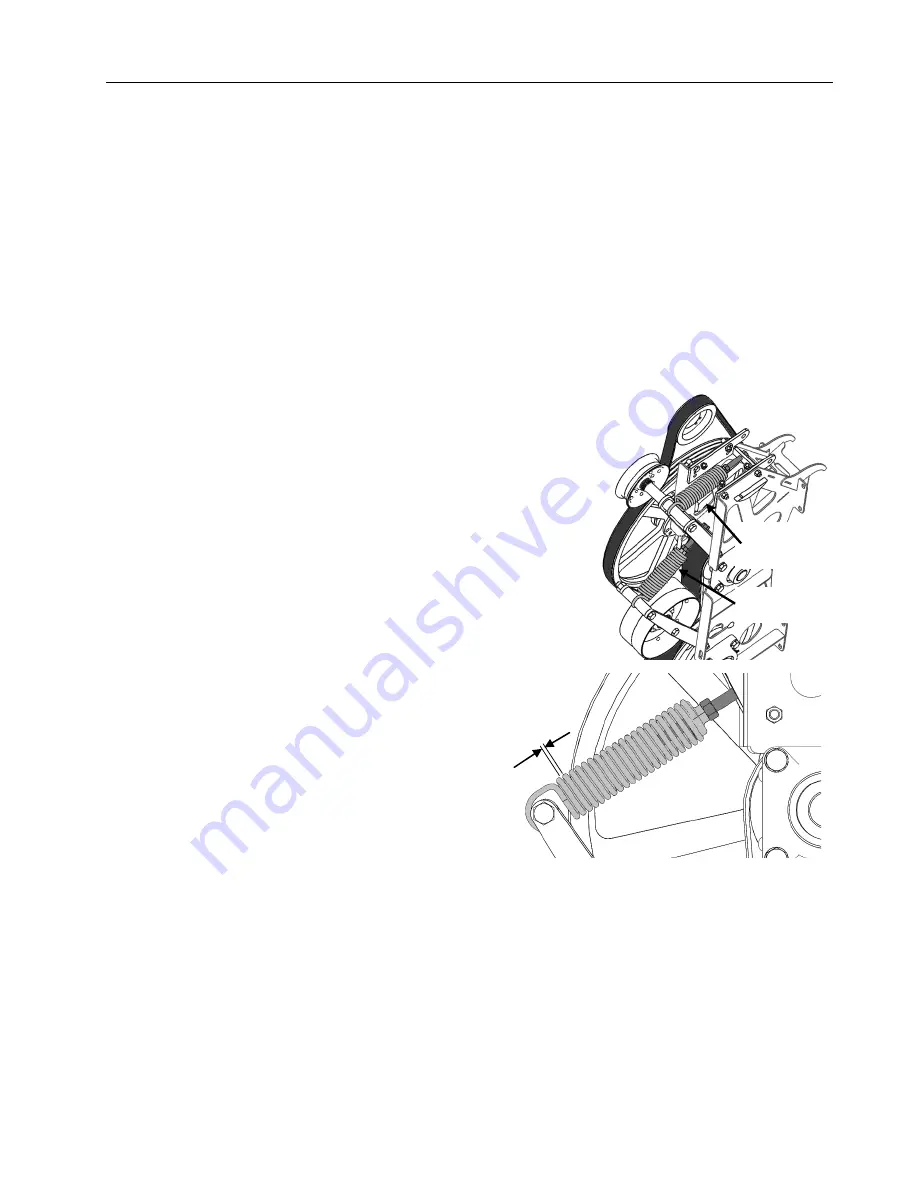
AWS AirBar Operator’s Manual
13
BELT / SHEAVE / IDLER CONDITION
Inspect all belts, sheaves and idlers for good condition.
Belts should appear supple with no shiny appearance on the
drive surface or cracks on the inner or outer surface.
Belts should not sit in the bottom of the sheave grooves or the
inner ribs between grooves should not be worn to a point. If
either of these cases exist, the sheave is worn excessively and
should be replaced.
Idler pulleys should be in-line with the belt running path and
parallel with the sheaves. If the idler is not inline or parallel,
inspect the idler bearing condition or the bronze bushings on
which the idler pivots for wear. Replace as required.
BELT TENSION
Proper belt tension is critical to both optimum performance and
long life of your AirBar system. Loose belts will create excessive
heat and ultimately fail. Belts that are too tight can lead to
accelerated bearing failure.
Belt tension is set using a draw-bolt to extend a spring. The
extended spring maintains tension.
On initial tensioning of new belts, tighten the draw bolt until a
quarter can fit between the coils. Once initial run-in is
completed, maintain a dime-thickness gap in the spring.
It is important to set the secondary belt tension first, then the
primary. Double-check the secondary belt tension after setting
primary tension.
“
Quarter
”
Thickness
–
Initial
“
Dime
”
Thickness
–
Run-In
Primary Tensioner
Secondary
Tensioner
Содержание AIRBAR
Страница 1: ...OPERATOR S MANUAL AWS Airbar Systems Header Mount Fan Version 20200325 ...
Страница 2: ......
Страница 4: ......