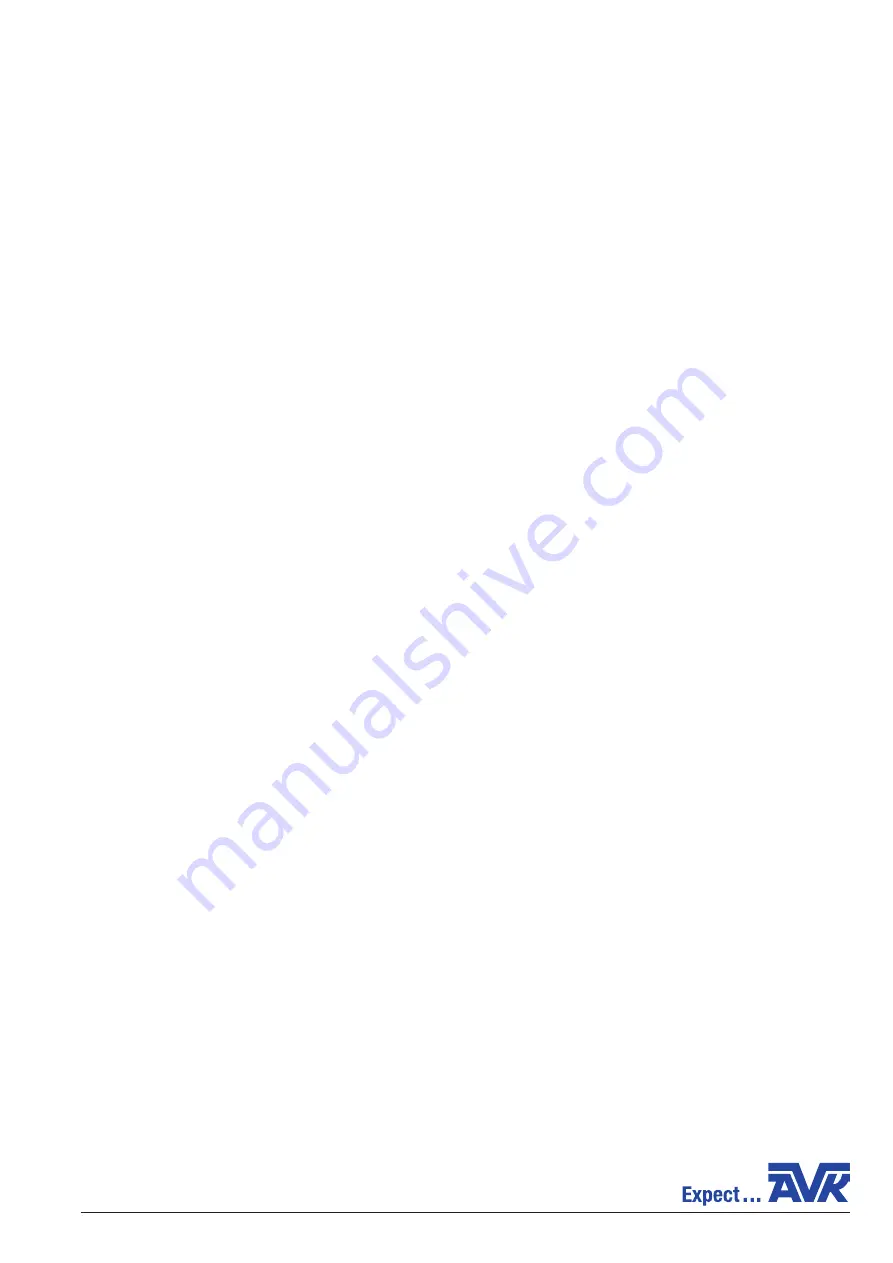
OPERATION & MAINTENANCE INSTRUCTIONS - ORIGINAL VERSION
AVK DOUBLE ECCENTRIC BUTTERFLY VALVES
SERIES 756
OPERATION & MAINTENANCE INSTRUCTIONS - ORIGINAL VERSION
AVK DOUBLE ECCENTRIC BUTTERFLY VALVES
SERIES 756
Page 7/13
MI Butterfly756 rev. AC 2018
When the AVK double eccentric butterfly valve is in open position, the disc may protrude beyond the overall length.
Make sure there is enough space between the disc and other pipeline installations.
Suspending the valve by its disc may lead to damage or destruction of disc or valve.
Hexagon bolts and nuts with washers from flange to flange must be used in the through holes to connect the valve with
the pipeline flanges. Fasten the bolts evenly and crosswise to prevent unnecessary tension with cracks or breaks in
consequence. The pipeline must not be pulled towards the valve. If the gap between valve and flange is too wide, this
must be compensated by thicker seals.
The seal material must be selected according to the operation conditions. However, we strongly recommend steel-
reinforced rubber seals according to EN 1514-1.
The operator must select bolts and nuts suitable for the respective operating pressure, temperature, flange material,
operational loads and the seal. The choice of seal material and whether the seal is used in main friction connections or
secondary friction connections will lead to very different tightening torques of the flange bolts. Therefore, the operator
must choose the tightening torque of the flange bolts according to the above parameters.
Make sure the flange bolts are not tightened too hard as this may result in crack formations in the flanges.
Make sure that pipeline flanges are in alignment with each other during installation of the valve.
The pipeline must be laid in a way that prevents harmful pipeline forces from being transmitted to the valve body. If
construction work near the valve is still in process, the valve must be adequately covered to protect it from dirt.
5. SET-UP AND VALVE OPERATION
5.1 VISUAL INSPECTION AND PREPARATION
A visual inspection of all functional parts must be performed before valve and equipment are put into operation. Check if
all bolted connections have been properly fastened.
5.2 FUNCTIONAL CHECK AND PRESSURE TEST
Prior to operation, the functional parts of the valve must be opened and closed completely at least once to ensure a
trouble-free operation.
Warning: It is not allowed to operate the AVK double eccentric butterfly valve in a dry state more than once due to the
risk of damaging the disc seals and/or increasing the torques.
A newly installed pipeline system must be thoroughly cleaned to remove all foreign particles. Residue or dirt particles in
the pipeline may damage the valve function or its free movement.
Please note that after repair work or upon commissioning of new equipment, it is very important to clean the pipeline
system again with the valve in fully open position. If detergents or disinfectants are used, it must be ensured that these
materials do not attack the valve material. As a standard, the valve is closed by turning the handwheel clockwise
towards the gearbox.
The dimensions of stem and actuators allow valve operation by one person via handwheel. The 90° turn is confined
by a limit stop on the gear. If it is turned any further due to excessive force, this may cause damage. Check that the
function is working properly by opening and closing the valve several times (not in a dry state).
6. ACTUATORS
6.1 GENERAL
Actuators (gear, pneumatic, hydraulic and electric actuators) are designed for flow velocities according to table 2 in EN
1074-1 (valves for water supply). Any deviating operating conditions need to be specified. Adjustment of the limit stops
(open, close) must not be changed without the manufacturer’s approval. If the valve is installed without gear units, it
must be ensured that the valve is not pressurised.