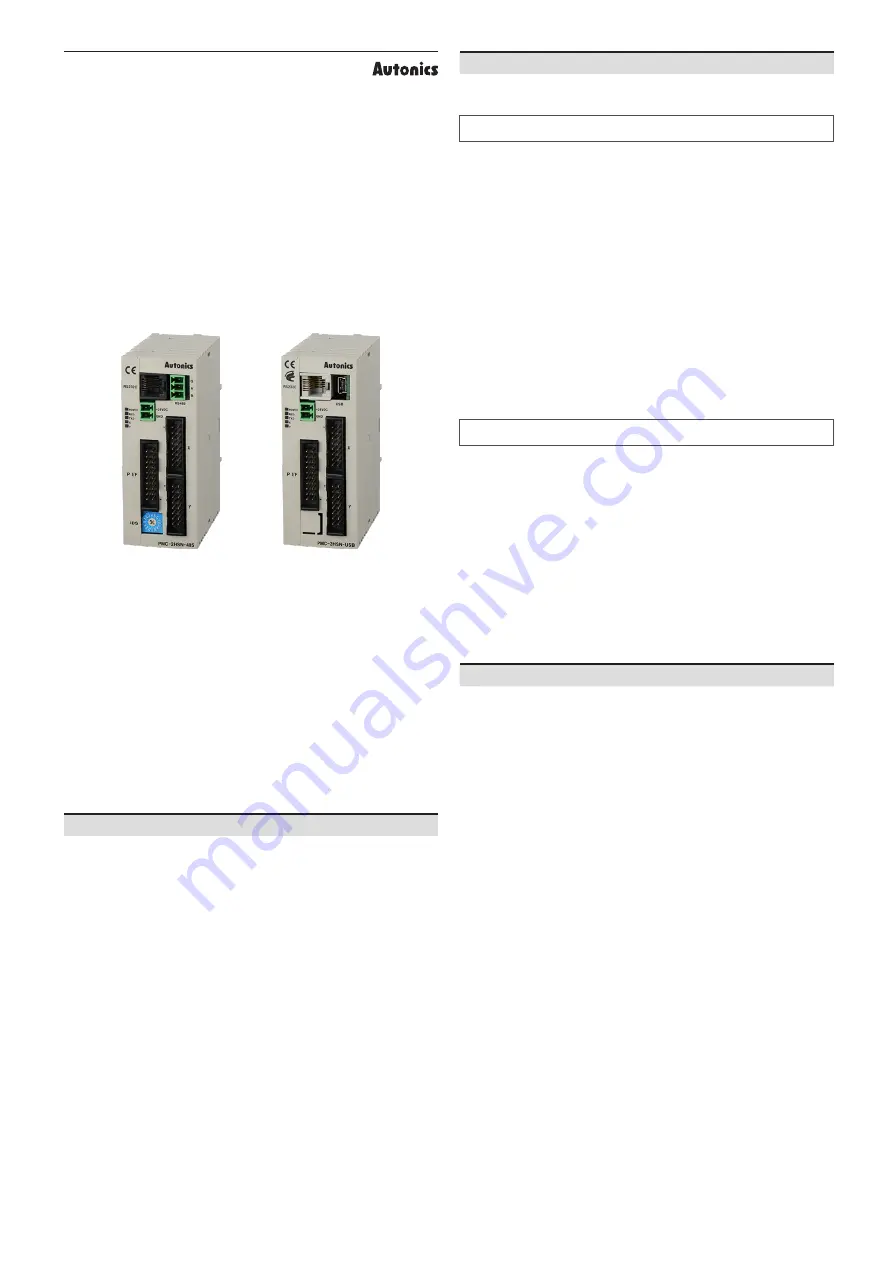
-|Transparent Guide|-
TCD210135AB
2 axis Interpolation Type
Motion Controller
PMC-2HSP Series
PRODUCT MANUAL
For your safety, read and follow the considerations written in the instruction
manual, other manuals and Autonics website.
The specifications, dimensions, etc. are subject to change without notice for product
improvement. Some models may be discontinued without notice.
Features
•
High speed independent 2 axis control with processing speed up to 4 Mpps
•
Supports linear and circular interpolation control
•
17 control commands and up to 200 steps of operation programming
•
Supports various control interfaces (USB, RS232C, RS485, Parallel I/F)
•
Multiple control of up to 32 axes (16 units) with RS485 communication (Modbus RTU)
•
4 operation modes: Jog mode, Continuous mode, Index mode, Program mode
•
Symmetrical/asymmetrical trapezoid or S-shaped acceleration/deceleration control
ᜢ ᜣ ᜫ
Safety Considerations
•
Observe all ‘Safety Considerations’ for safe and proper operation to avoid hazards.
•
symbol indicates caution due to special circumstances in which hazards may occur.
Warning
Failure to follow instructions may result in serious injury or death.
01.
Fail-safe device must be installed when using the unit with machinery that may
cause serious injury or substantial economic loss. (e.g. nuclear power control,
medical equipment, ships, vehicles, railways, aircraft, combustion apparatus,
safety equipment, crime / disaster prevention devices, etc.)
Failure to follow this instruction may result in personal injury, economic loss or fire.
02.
Do not use the unit in the place where flammable / explosive / corrosive gas,
high humidity, direct sunlight, radiant heat, vibration, impact or salinity may be
present.
Failure to follow this instruction may result in explosion or fire.
03.
Install on a device panel or DIN rail to use.
Failure to follow this instruction may result in fire.
04.
Do not connect, repair, or inspect the unit while connected to a power source.
Failure to follow this instruction may result in fire.
05.
Check ‘Connections’ before wiring.
Failure to follow this instruction may result in fire.
06. Do not disassemble or modify the unit.
Failure to follow this instruction may result in fire.
07.
Do not cut off power or disconnect connectors while operating the unit.
Failure to follow this instruction may result in personal injury or economic loss.
08.
Install the safety device at the out of the controller for stable system operation
against external power error, controller malfunction, etc.
Failure to follow this instruction may result in personal injury or economic loss.
Caution
Failure to follow instructions may result in injury or product damage.
01.
When connecting the power input, use AWG 28 - 16 (0.081 to 1.31mm
2
) cable or
over.
02.
Must use the insulated trans at the power input.
Failure to follow this instruction may result in personal injury or fire.
03.
Use the unit within the rated specifications.
Failure to follow this instruction may result in fire or product damage.
04.
Use a dry cloth to clean the unit, and do not use water or organic solvent.
Failure to follow this instruction may result in fire.
05.
Keep the product away from metal chip, dust, and wire residue which flow into the
unit.
Failure to follow this instruction may result in fire or product damage.
06.
If a ribbon cable is used as the I/O line, connect the cable correctly and prevent
from poor contact.
Failure to follow this instruction may result in malfunction.
07.
Note that this device is KCC certified for commercial use.
Make proper applications for the product.
Cautions during Use
•
Follow instructions in ‘Cautions during Use’.
Otherwise, it may cause unexpected accidents.
•
Power supply should be insulated and limited voltage/current or Class2, SELV power supply
device.
•
Install a power switch or circuit breaker in the easily accessible place for supplying or
disconnecting the power.
•
Wire as short as possible and keep away from high voltage lines or power lines, to prevent
inductive noise.
•
Run the unit after setting parameter with proper value depending on the load and
environment.
•
Make sure that Power On function is set to ON in atMotion program before supplying the
power to the unit.