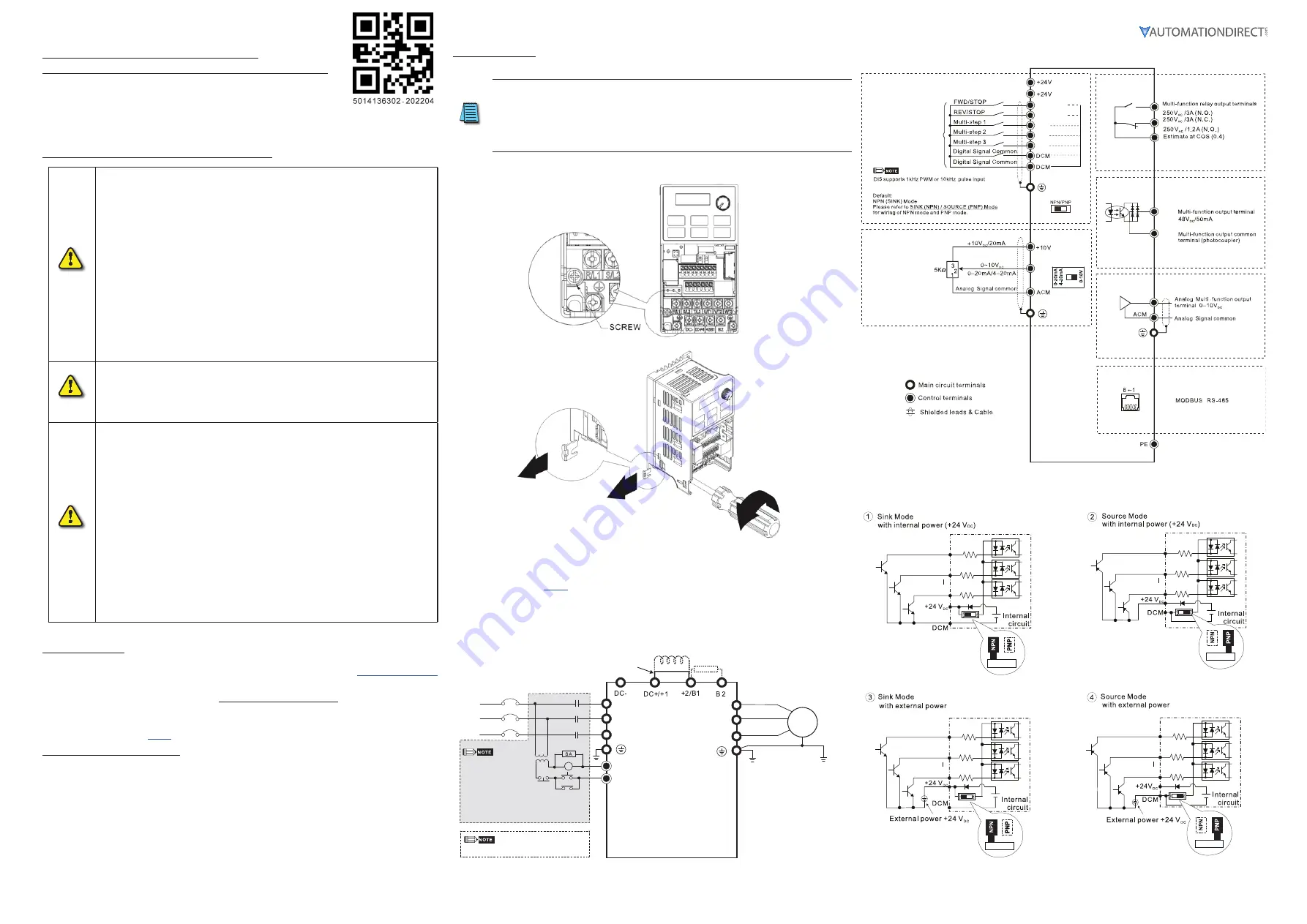
Page 1
GS10 AC Drive Quick-Start Guide – 1st Ed 06/15/2022
DURA
pulse
GS10 AC Drive Quick-Start Guide
GS10_QSP 1st Edition 06/15/2022
GS10 AC Drives Installation Instructions
Sensorless Vector Control Variable Frequency Micro-drive
• Please read this instruction sheet thoroughly before installation and retain for later
reference.
• To ensure the safety of operators and equipment, only qualified personnel familiar
with AC drives should install, wire, program, and operate the GS10 drive. Always read this instruction sheet
thoroughly before using the GS10 drive, especially the WARNING, DANGER and CAUTION notes. If you have any
questions, please contact AutomationDirect.
PLEASE READ PRIOR TO INSTALLATION FOR SAFETY
DANGER
• The ground terminal of the GS10 drive must be grounded correctly. The grounding method
must comply with the laws of the country where the GS10 drive is to be installed.
• After power has been turned off, the capacitors in the GS10 drive may retain a charge for
several minutes. To prevent personal injury, visually verify that the “CHARGE” LED has
turned off. Then measure to confirm that the DC bus voltage level between terminals (+1)
and (-) is less than 25VDC before touching any terminals. (Capacitor discharge will take at
least 5 minutes for most GS10 models).
• The CMOS ICs on the internal circuit boards of the GS10 drive are sensitive to static
electricity. Please DO NOT touch the circuit boards with your bare hands before taking
anti-static measures. Never disassemble the internal components or circuits.
• If wiring changes must be made, turn off power to the GS10 drive before making those
changes. Allow the internal DC bus capacitors in the GS10 drive sufficient time to discharge
prior to making changes in power or control wiring. Failure to do so may result in short
circuit and fire. To ensure personal safety, allow DC bus voltage to discharge to a safe level
before making wiring changes to the GS10 drive.
• DO NOT install the GS10 drive in locations subject to high temperature, direct sunlight, or
flammable materials.
WARNING
• Never apply power to the output terminals U/T1, V/T2, W/T3 of the GS10 drive. If a fault
occurs during operation of the GS10 drive, refer to the fault code descriptions and corrective
actions to reset the fault before attempting to operate the GS10 drive.
• DO NOT use Hi-pot test for internal components. The semi-conductors in the GS10 drive are
easily damaged by high voltage.
CAUTION
• Long motor lead lengths may result in reflective wave due to impedance mismatch between
the motor cable and the motor. Reflective wave may damage the insulation of the motor.
To avoid the possibility of reflective wave damage, use an inverter-rated motor with an
insulation rating of 1600 volts. A load reactor installed between the GS10 drive and motor
will help to mitigate reflective wave.
• Nominal supply voltage to the GS10 drive should be less than or equal to 120/240/480 volts
AC depending on GS10 model.
• Nominal supply current capacity should be less than or equal to 100kA for all GS10 models.
• The GS10 drive must be installed in a clean, well-ventilated and dry location, free from
corrosive gases or liquids.
• The GS10 drive must be stored within an ambient temperature range from –40°C to +85°C,
and relative humidity range of 0% to 90% without condensation.
• Do not apply AC power to the GS10 drive with the front cover removed. Following a fault of
the GS10 drive, wait 5 seconds before pressing the RESET key.
• To improve power factor, install a line reactor ahead of the GS10 drive. Do not install power
correction capacitors in the main AC supply circuit to the GS10 drive to prevent drive faults
due to over-current.
Minimum Wiring
• AC input power to R/L1, S/L2, T/L3 (for single-phase input, use two of the terminals) (For applicability of 1-phase
input power, please refer to Chapter 1 of the DURApulse GS10 AC Drives User Manual at
.)
• Ground from the power supply
• Drive power to the motor (U, V, W on T1, T2, T3) (For use with 3-phase motors only!)
• Ground to the motor
With this minimal wiring, the drive can be operated via the keypad to test the motor and drive installation.
See the “Parameter Set Up” (
) section to configure the drive for keypad operation.
Recommended Safety Wiring
We strongly recommend that customers configure a multifunction input as the Emergency Stop to stop the
drive in an emergency situation.
To configure this feature, set any multifunction input to selection 28 (Emergency Stop EF1) and wire a relay or
E-stop pushbutton to the configured input.
Wiring Diagrams
RFI Jumper Removal
If the power distribution system supplying the GS10 AC drive is a floating (IT) or an
asymmetric ground system (including most 120V inputs), the RFI jumper must be
removed.
Removing the RFI jumper uncouples the internal RFI capacitor (filter capacitor)
between the GS10 drive frame and circuitry to avoid damaging those circuits and
(according to IEC 61800-3) to reduce ground leakage current.
GS10 Frame A through D
Main Wiring (Power Circuit)
For main (power) wiring terminal specifications, Please refer to “Specifications for Wiring Terminals –
Main-Circuit Terminals” (
GS10 all Frames
*(Note that 1-phase only drives do not have a T/L3 terminal. 120V drives do not have DC- or DC+
terminals).
R/L1
S/L2
T/L3*
R/L1
S/L2
T/L3*
U/T1
V/T2
W/T3
3~
R1
R1C
R1 and R1C are the relay output terminals.
Input: one-phase / three-phase* power
DC reactor (optional)
Brake resistor (optional)
Jumper
Motor
Circuit Breaker or Fuse
MC
ON
MC
OFF
It is recommended that
you install a protective
circuit at R1 – R1C to
protect the drive from
damage.
When a fault occurs, the MC contactor
switches to OFF to shut off the drive input
power and protect the power system.
MC
GS10 Control Terminal Wiring
R1O
R1C
R1
DO1
DOC
AO1
AI
AI
FWD(DI1)
REV (DI2)
DI3
DI4
DI5
Functions set via Parameter P02.13
Default functions
set via Parameters
P02.00 - P02.05
Functions set via Parameter P02.16
See User Manual Chapter 2 for
sink/source wiring examples
Default functions set via Parameter P03.00
Functions set via Parameter P03.20
(SG+ Pin5, SG- Pin4, SGND Pin3,7)
DI1
DI2
DI5
DI1
DI2
DI5
DI1
DI2
DI5
DI1
DI2
DI5