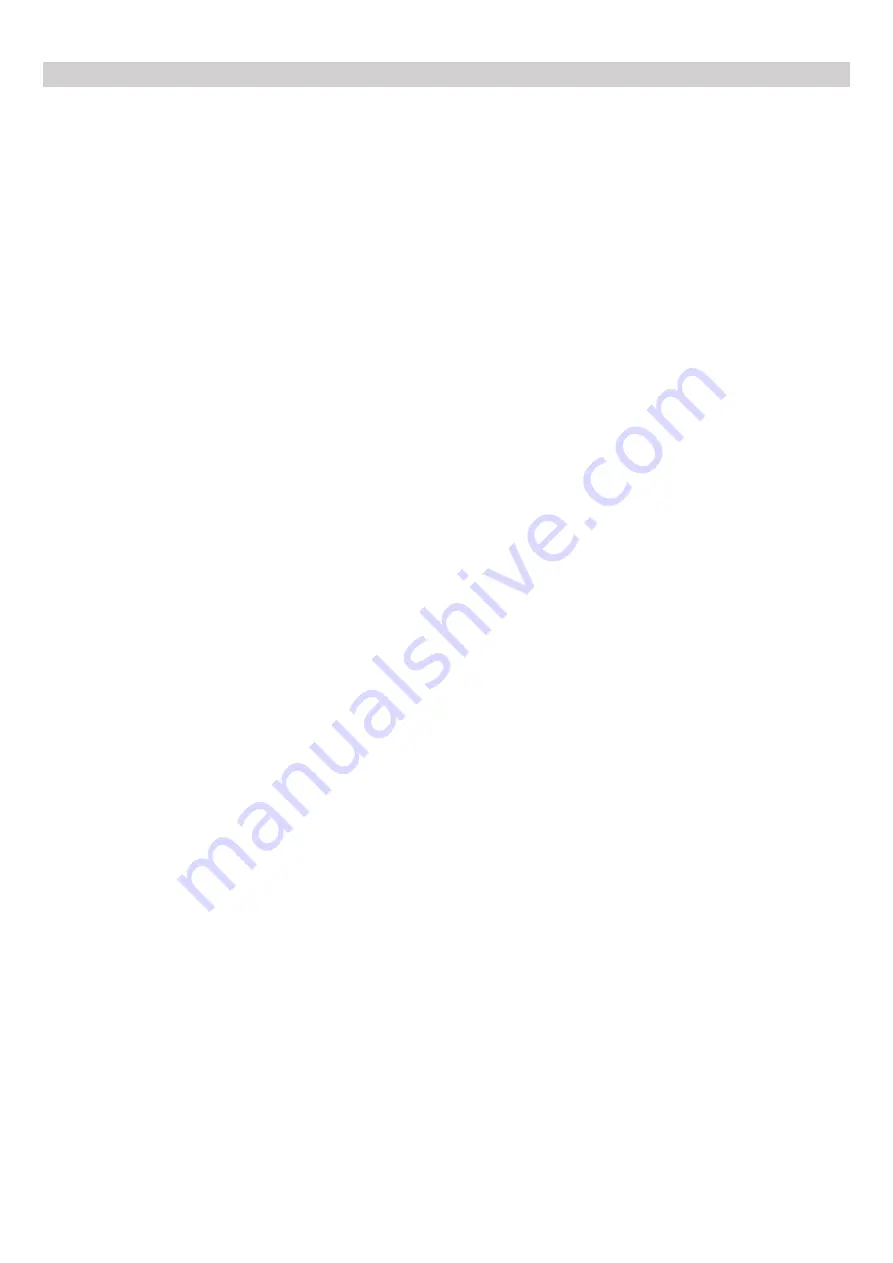
INSTRUCTION FOR REPAIRING APPLIANCES CONTAINING R 290
AUTHORISED PERSONS ONLY!
- that capacitors are discharged; this shall be done in a safe manner to avoid possibility of
sparking.
- that there are no live electrical components and wiring are exposed while charging, recovering
or purging the system;
- that there is continuity of earth bonding.
10. Repairs to sealed components
During repairs to sealed components, all electrical supplies shall be disconnected from the
equipment being worked upon prior to any removal of sealed covers, etc. If it is absolutely
necessary to have an electrical supply to equipment during servicing, then a permanently operating
form of leak detection shall be located at the most critical point to warn of a potentially hazardous
situation. Particular attention shall be paid to the following to ensure that by working on electrical
components, the casing is not altered in such a way that the level of protection is affected. This
shall include damage to cables, excessive number of connections, terminals not made to original
specification, damage to seals, incorrect fitting of glands, etc.
Ensure that apparatus is mounted securely.
Ensure that seals or sealing materials have not degraded such that they no longer serve the
purpose of preventing the ingress of flammable atmospheres. Replacement parts shall be in
accordance with the manufacturer's specifications.
NOTE: use of silicon sealant may inhibit the effectiveness of some types of leak detection
equipment. Intrinsically safe components do not have to be isolated prior to working on them.
11. Repair to intrinsically safe components
Do not apply any permanent inductive or capacitance loads to the circuit without ensuring that this
will not exceed the permissible voltage and current permitted for the equipment in use. Intrinsically
safe components are the only types that can be worked on while live in the presence of a flammable
atmosphere. The test apparatus shall be at the correct rating. Replace components only with parts
specified by the manufacturer. Other parts may result in the ignition of refrigerant in the atmosphere
from a leak.
12. Cabling
Check that cabling will not be subject to wear, corrosion, excessive pressure, vibration, sharp edges
or any other adverse environmental effects. The check shall also take into account the effects of
aging or continual vibrations from sources such as compressors or fans.
13. Detection of flammable refrigerants
Under no circumstances shall potential sources of ignition be used in the searching for or detection
of refrigerant leaks. A halide torch (or any other detector using a naked flame) shall not be used.
14. Leak detection methods
The following leak detection methods are deemed acceptable for systems containing flammable
refrigerants.
Electronic leak detectors shall be used to detect flammable refrigerants, but the sensitivity may not
be adequate, or may need re-calibration. (Detection equipment shall be calibrated in a refrigerant-
free area). Ensure that the detector is not a potential source of ignition and is suitable for the
refrigerant used. Leak detection equipment shall be set at a percentage of the LFL of the refrigerant
and shall be calibrated to the refrigerant employed and the appropriate percentage of gas (25%
maximum) is confirmed.
Leak detection fluids are suitable for use with most refrigerants but the use of detergents containing
chlorine shall be avoided as the chlorine may react with the refrigerant and corrode the copper
pipe-work.
If a leak is suspected, all naked flames shall be removed/extinguished.
If a leakage of refrigerant is found which requires brazing, all of the refrigerant shall be recovered
from the system, or isolated (by means of shit off valves) in a part of the system remote from the
leak.
11