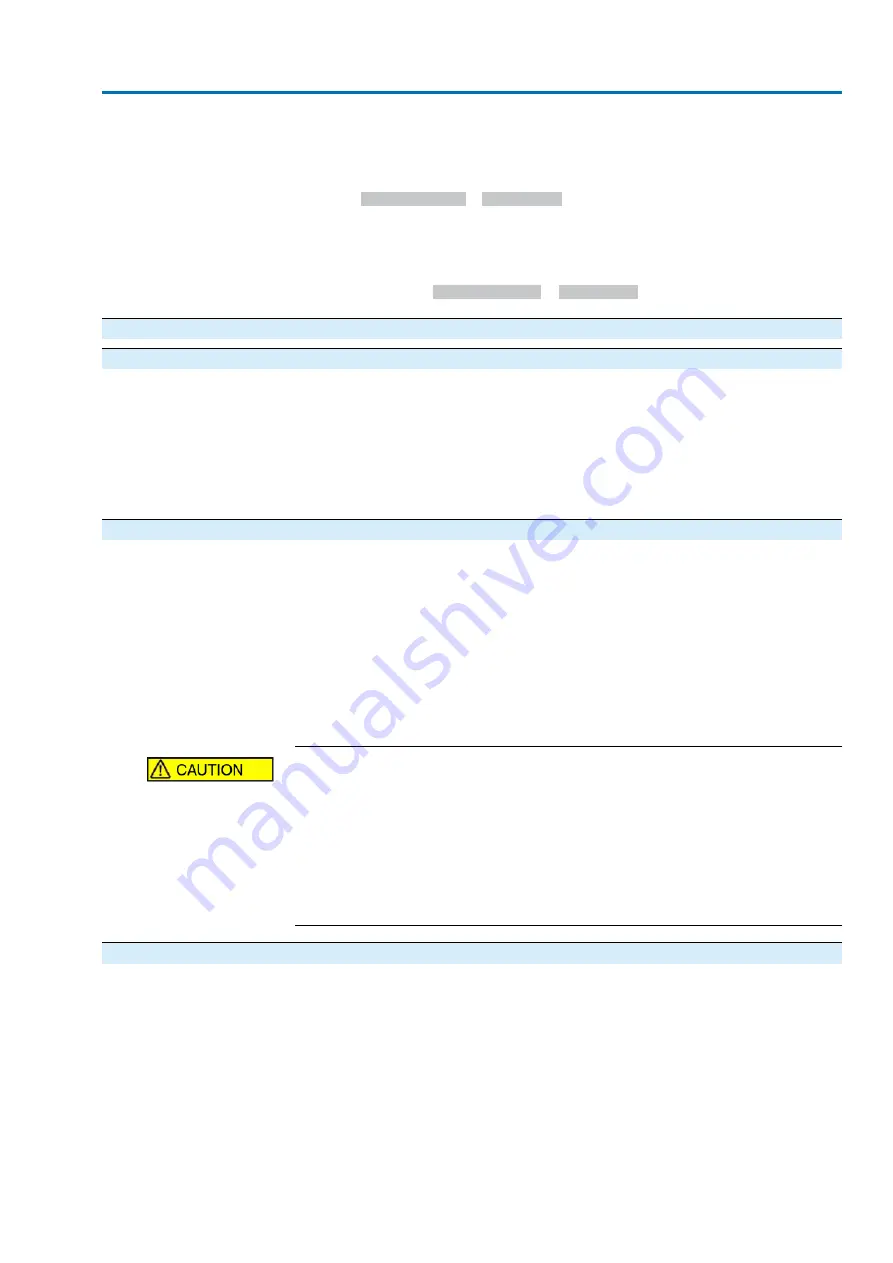
Information
●
Only the Profibus DP-V0 standard arrangement of the process representation
input of AC 01.1/ACExC 01.1 is supported, deviating arrangements of the
Profibus DP-V0 process data input require use/installation of AUMA04CF.gsd
or AUMA0CBD.gsd file in the DCS.
●
With
connection type
=
AUMATIC.1
the AC 01.2/ACExC 01.2 does not provide
any diagnostic NAMUR NE 107 information within the cyclic process data rep-
resentation.
●
EDD or DTM of the AC 01.2/ACExC 01.2 must imperatively be used for acyclic
communication via Profibus DP-V1 with AC 01.2/ACExC 01.2!
●
Factory setting:
Connection type
=
AUMATIC.2
3.7.
Communication monitoring
3.7.1.
Connection monitoring of the Profibus DP communication
The connection monitoring within the master has to be activated to monitor both
master and cable connection between master and actuator (parameter telegram
byte 1, bit 3, WD_ON = 1).
Only if the connection monitoring is active can the actuator react in the even of loss
of communication once the monitoring time also set in the master has elapsed.
The reaction of the actuator also depends on the settings for failure behaviour or
EMERGENCY BEHAVIOUR.
3.7.2.
Fail Safe and Global Control Clear telegrams
Another possibility to set the slave to a safe state in the event of a fault are the fail
safe telegrams (telegrams with data length = 0). If fails safe telegrams are received,
the actuator remains in the DataExchange state; depending on the respective setting,
the actuator may initiate the failure behaviour or the EMERGENCY behaviour. The
actuator quits the Fail Safe state as soon as valid telegrams with the data length
≠
0 are received.
Furthermore, the Global Control Clear (GC Clear) master telegrams can also be
used to initiate the failure behaviour or the EMERGENCY behaviour. This state can
be disabled using a Global Control Operate telegram (GC Operate).
For activated EMERGENCY behaviour:
The actuator can start its operation due to an EMERGENCY signal or a loss
of communication.
Risk of personal injuries or damage to the valve.
→
For commissioning and maintenance work: Set selector switch to position 0
(OFF). The motor operation can only be interrupted in this selector switch posi-
tion.
→
If the actuator starts its operation by accident: Set selector switch to position 0
(OFF).
3.8.
I & M functions
The actuator controls support the I & M functions according to PNO guideline 3.502.
With the term Identification & Maintenance (I & M) functions, the Profibus user
organisation e.V. (PNO) introduced a new functionality for all Profibus devices with
acyclic communication channel that may prove very useful for plant operators. The
I & M functions define how certain device-describing data (according to name plate)
is to be uniformly stored in the Profibus devices. Engineering tools may then read
and inteprete the data according to a code which can be accessed on the PNO
server. This provides uniform and powerful access to all important and current device
data, one of the major requirements for asset management.
Part of the device-specific I & M information is the unambiguous asset identification
using a manufacturer ID (MANUFACTURER_ID, for AUMA actuators = 319), the
19
Actuator controls
AC(V) 01.2/AC(V)ExC 01.2 Profibus DP
Commissioning
Содержание AC(V) 01.2
Страница 1: ...Actuator controls AC V 01 2 AC V ExC 01 2 Profibus DP Device integration Manual...
Страница 22: ...22 Actuator controls Description of the data interface AC V 01 2 AC V ExC 01 2 Profibus DP...
Страница 89: ...89 Actuator controls AC V 01 2 AC V ExC 01 2 Profibus DP...
Страница 90: ...90 Actuator controls AC V 01 2 AC V ExC 01 2 Profibus DP...