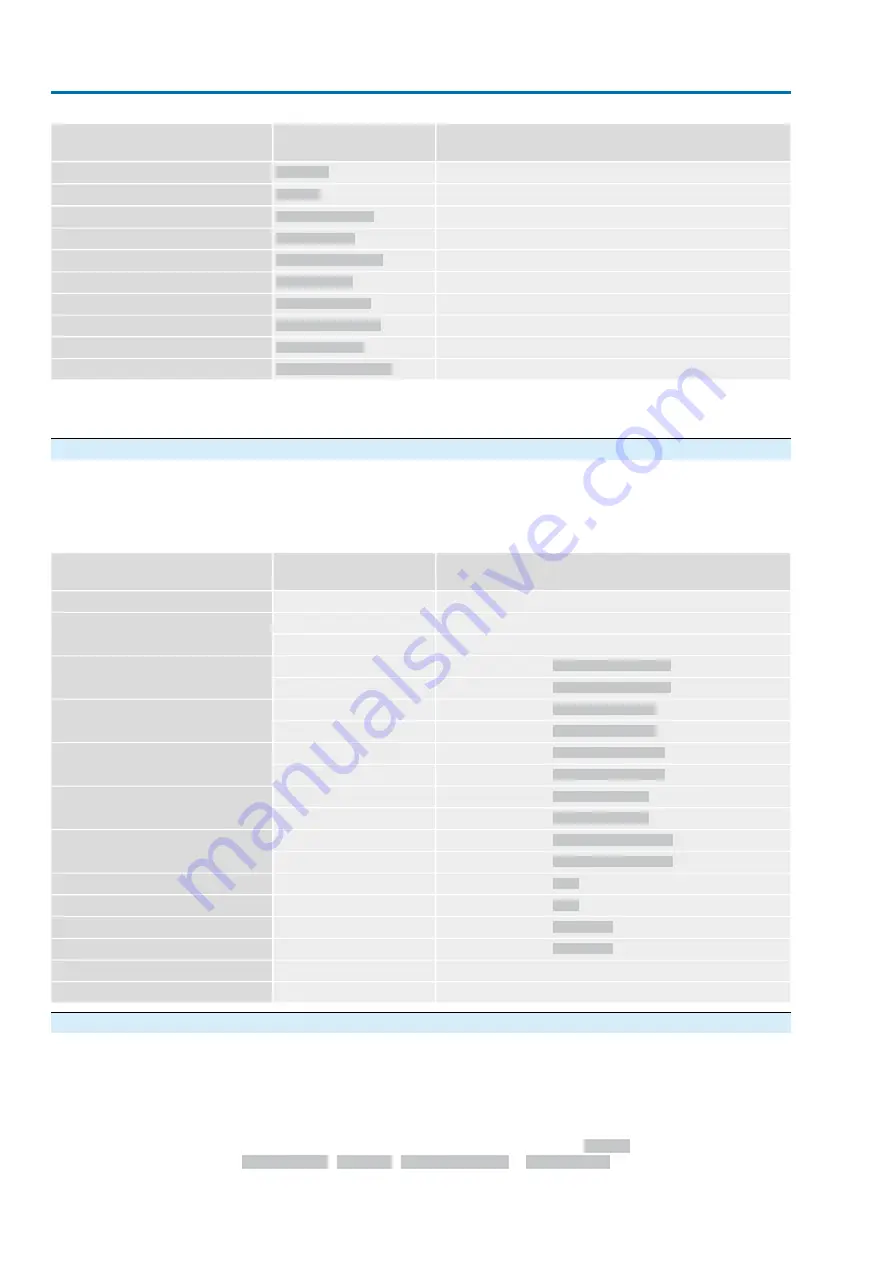
Description
Designation
(process representation)
Prm-Text-Def GSD file
Safe STOP function is active.
Safe Stop
1)
(205) = "Safe Stop"
A SIL fault has occurred (collective signal).
SIL fault
1)
(206) = "SIL fault"
A SIL function is active.
SIL function active
1)
(207) = "SIL function active"
(PVST) Partial Valve Stroke Test should be executed
PVST required
(208) = "PVST required"
Mechanic maintenance requirement
Mainten. mechanics
(209) = "Mechanic lifetime"
Seal maintenance requirement
Mainten. seals
(210) = "Seal lifetime"
Lubricant maintenance requirement
Mainten. lubricant
(211) = "Seal lifetime"
Contactor maintenance requirement
Mainten. contactors
(212) = "Contactor lifetime"
The set maintenance interval has expired.
Mainten. interval
(213) = "Maintenance interval"
Maintenance required
Maintenance required
(214) = "Maintenance required"
The safety function indications via fieldbus are for information only and must not be used as part of a safety function. The I/O signals of
the SIL module must be used for this purpose.
1)
3.6.3.
Additional (user-definable) parameters (option)
Parameter description of additional user parameters for setting the time stamp and
alarms according to Profibus DP-V2, available with the optional version
AUMA0CBD.gsd.
Table 3: Description of additional settings
Description
Setting
Prm-Text GSD Datei
ExtUserPrmData =
No function
–
1 "Setpoint valid bit"
DP-V2 time stamp deactivated.
Text(0) = "disable"
2 "Timestamp (TS)"
DP-V2 time stamp activated.
Text(1) = "enable"
DP-V2 time stamp of
End position CLOSED
signal deactivated.
Text(0) = "disable"
3 "TS -> End Position Close"
DP-V2 time stamp of
End position CLOSED
signal activated.
Text(1) = "enable"
DP-V2 time stamp of
End position OPEN
signal deactivated.
Text(0) = "disable"
4 "TS -> End Position Open"
DP-V2 time stamp of
End position OPEN
signal activated.
Text(1) = "enable"
DP-V2 time stamp of
Torque sw. CLOSED
signal deactivated.
Text(0) = "disable"
5 "TS -> Torque Limit Switch Close"
DP-V2 time stamp of
Torque sw. CLOSED
signal activated.
Text(1) = "enable"
DP-V2 time stamp of
Torque sw. OPEN
signal deactivated.
Text(0) = "disable"
6 "TS -> Torque Limit Switch Open"
DP-V2 time stamp of
Torque sw. OPEN
signal activated.
Text(1) = "enable"
DP-V2 time stamp of
Selector sw. REMOTE
signal deactivated.
Text(0) = "disable"
7 "TS -> Ready and Remote"
DP-V2 time stamp of
Selector sw. REMOTE
signal activated.
Text(1) = "enable"
DP-V2 time stamp of
Fault
signal deactivated.
Text(0) = "disable"
8 "TS -> Fault"
DP-V2 time stamp of
Fault
signal activated.
Text(1) = "enable"
DP-V2 time stamp of
Phase fault
signal deactivated.
Text(0) = "disable"
9 "TS -> Power Supply Fault"
DP-V2 time stamp of
Phase fault
signal activated.
Text(1) = "enable"
Without function (reserved)
–
10 "TS -> reserved"
Without function (reserved)
–
11 "reserved Byte"
3.6.4.
Further adaptation options
From firmware 04.05.xx, the actuator controls provide the option to adapt to the
existing DCS configurations of the actuator type range AC 01.1/ACExC 01.1. Actuator
controls of type range AC 01.2/ACExC 01.2 can be adapted as to support the default
arrangement of the Profibus DP-V0 process representation input of
AC 01.1/ACExC 01.1 without changing the Profibus configuration of the DCS.
Setting is performed using the following parameter:
Device
configuration
>
Profibus
>
Connection type
=
AUMATIC .1
18
Actuator controls
Commissioning
AC(V) 01.2/AC(V)ExC 01.2 Profibus DP
Содержание AC(V) 01.2
Страница 1: ...Actuator controls AC V 01 2 AC V ExC 01 2 Profibus DP Device integration Manual...
Страница 22: ...22 Actuator controls Description of the data interface AC V 01 2 AC V ExC 01 2 Profibus DP...
Страница 89: ...89 Actuator controls AC V 01 2 AC V ExC 01 2 Profibus DP...
Страница 90: ...90 Actuator controls AC V 01 2 AC V ExC 01 2 Profibus DP...