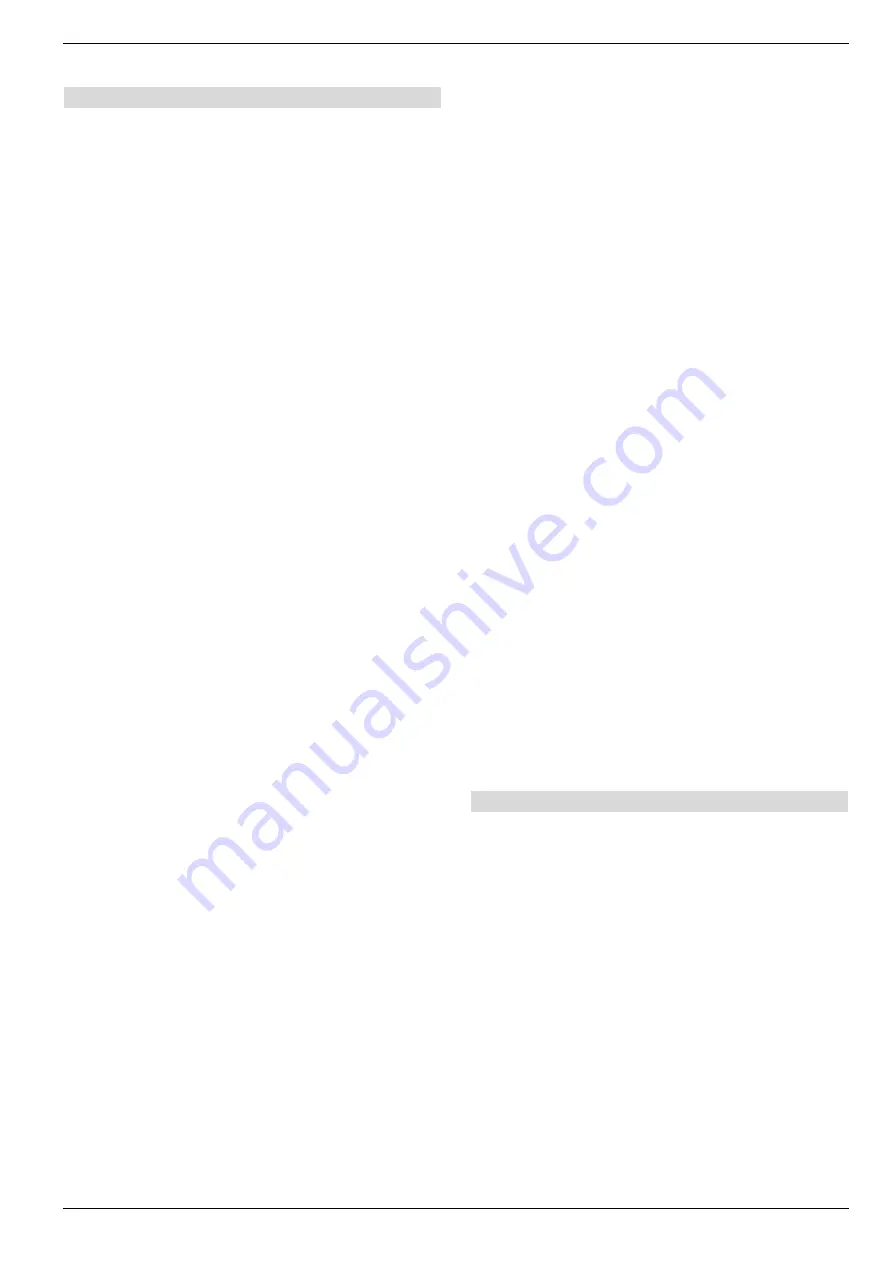
S
AFETY DURING USE AND OPERATION
To lift a compressor, all loose or pivoting parts, e.g. doors and drawbar, shall
first be securely fastened. Do not attach cables, chains or ropes directly to the
lifting eye; apply a crane hook or lifting shackle meeting local safety rules.
Helicopterlifting using the lifting eye is forbidden.
It is strictly forbidden to dwell or stay in the risk zone under a lifted load.
Never lift the compressor over people or residential areas.
Lifting acceleration and retardation shall be kept within safe limits.
1
Before towing the compressor:
Ð ascertain that the pressure vessel(s) is (are) depressurized,
Ð check the drawbar, the brake system and the towing eye. Also check
the coupling of the towing vehicle,
Ð check that the pivot wheel or stand leg is safely locked in the raised
position,
Ð ascertain that the towing eye can swivel freely on the hook,
Ð check that the wheels are secure and that the tyres are in good
condition and inflated correctly,
Ð connect the signalisation cable, check all lights and connect the
pneumatic brake couplers,
Ð attach the safety break-away cable to the towing vehicle,
Ð remove wheel chocks, if applied, and disengage the parking brake.
2
If the compressor is to be backed up by the towing vehicle, disengage the
overrun brake mechanism.
3
Never exceed the maximum towing speed of the compressor.
4
Place the compressor on level ground and apply the parking brake before
disconnecting the compressor from the towing vehicle. Unclip the safety
break-away cable. If the compressor has no parking brake the support of
the towbar partly acts as a brake; it is recommended to immobilize the
compressor by placing chocks before or behind the wheels.
When the towbar can be positioned vertically, the locking device must be
applied and kept in good order.
5
When the compressor has to operate in a fire-hazardous environment,
each engine exhaust has to be provided with a spark arrestor to trap
incendiary sparks.
6
The exhaust contains carbon monoxide which is a lethal gas. When the
compressor is used in a confined space, conduct the engine exhaust to the
outside atmosphere by a pipe of sufficient diameter (min. 100 mm); do
this in such a way that no extra back pressure is created for the engine. If
necessary, install an extractor.
7
When operating in a dust-laden atmosphere, place the unit so that dust is
not carried towards it by the wind. Operation in clean surroundings
considerably extends the intervals for cleaning the air intake filters and
the cores of the coolers.
8
Locate the unit away from walls. Take all precautions to ensure that hot
air exhausted from the engine and driven machine cooling systems cannot
be re-circulated. If such hot air is taken in by the engine or driven
machine cooling fan, this may cause overheating of the unit; if taken in
for combustion, the engine power will be reduced.
9
No external force may be exerted on the air outlet valves, e.g. by pulling
on hoses or by installing auxiliary equipment directly to a valve, e.g. a
water separator, a lubricator, etc.
10 Distribution pipework and air hoses must be of correct size and suitable
for the working pressure. Never use frayed, damaged or deteriorated
hoses. Replace hoses and flexibles of which the lifetime expired. Use
only the correct type and size of hose end fittings and connections.
A hose connected to a 2 inch (50 mm) valve must be provided with a
safety wire (¿ 8 mm) fixed to the hose (each 500 mm) for effective
pressures as from 10 bar (145 psi) up, although it is recommended to
apply such safeguard already from 4 bar (60 psi) up. The safety wire ends
have to be attached, one to the eye provided next to the compressor air
outlet valve, the other one to a point near to the air inlet of the applied
equipment.
Finally a wire mesh hose can be fixed over the hose ends to dampen the
blast in case a connection starts leaking or should become undone.
Close the compressor air outlet valve before connecting or disconnecting
a hose. Ascertain that a hose is fully depressurized before disconnecting
it.
When blowing through a hose or air line, ensure that the open end is held
securely. A free end will whip and may cause injury.
Never play with compressed air. Never apply it to your skin or direct an air
stream at people. Never use it to clean dirt from your clothes. When using it
to clean down equipment, do so with extreme caution and use eye protection.
Do not use compressed air from any type of compressor, without taking
extra measures, for breathing purposes as this may result in injury or
death. For breathing air quality, the compressed air must be adequately
purified according to local legislation and standards.
Breathing air must always be supplied at stable, suitable pressure.
11 Never move a unit when external lines or hoses are connected to the
outlet valves, to avoid damage to valves and/or manifold and hoses.
12 Never refill fuel while the compressor is running. Keep fuel away from hot
parts such as air outlet pipes or the engine exhaust. Do not smoke when
fuelling. When fuelling from an automatic pump, an earthing cable should
be connected to the compressor to discharge static electricity. Never spill
nor leave oil, fuel, coolant or cleansing agent in or around the compressor.
13 Never operate the compressor in surroundings where there is a possibility
of taking in flammable or toxic fumes.
14 Never operate the compressor at pressures or speeds below or in excess
of the limit ratings stated on the Principal Data sheet.
15 On water-cooled engines with closed cooling circuit: allow the
compressor to cool before removing a pressure cap.
16 All doors shall be shut during operation so as not to disturb the cooling air
flow inside the bodywork and/or render the silencing less effective. A door
should be kept open for a short period only, e.g. for inspection or adjustment.
17 Wear ear protectors when environmental noise can reach or exceed
90 dB(A). Beware of long-time exposure to noise.
18 Periodically check that:
Ð all safety equipment is in good working order,
Ð all guards and air conducting baffles are in place and securely fastened,
Ð all hoses and/or pipes inside the compressor are in good condition,
secure and not rubbing,
Ð there are no fuel, oil or coolant leaks,
Ð the tension of drive belts is correct,
Ð all fasteners are tight,
Ð all electrical leads are secure and in good order,
Ð the engine exhaust system is in good condition,
Ð air outlet valves and manifold, hoses, couplings, etc. are in good
repair, free of wear or abuse,
Ð the wheel nuts are tightened to the proper torque.
19
Diesel engine exhaust and some of its constituents are known to the State of
Califorina to cause cancer, birth defects, and other reproductive harm.
When more than one compressor is connected to a common header, be sure
each compressor has a non-return valve (check valve) to prevent reverse
rotation when stopping.
S
AFETY DURING MAINTENANCE AND REPAIR
Maintenance and repair work shall only be carried out by adequately trained
personnel; if required, under supervision of someone qualified for the job.
1
Use only the correct tools for maintenance and repair work.
2
Use only genuine spare parts.
3
All maintenance work, other than routine attention, shall only be
undertaken when the compressor is stopped. Ensure that the compressor
cannot be started inadvertently.
4
Before removing any pressurized component, effectively isolate the
compressor from all sources of pressure and relieve the entire system of
pressure. Do not rely on non-return valves (check valves) to isolate
pressure systems.
5
Never use flammable solvents or carbon tetrachloride for cleaning parts.
Take safety precautions against toxic vapours of cleaning liquids.
6
Scrupulously observe cleanliness during maintenance and when
performing repairs. Keep dirt away by covering the parts and exposed
openings with a clean cloth, paper or tape.
7
Never weld on or perform any operation involving heat near the fuel or
oil systems. Fuel and oil tanks must be completely purged, e.g. by steam-
cleaning, before carrying out such operations.
Never weld on, or in any way modify, pressure vessels. Disconnect the
alternator cables during arc welding on the compressor.
8
Support the drawbar and the axle(s) securely if working underneath the
compressor or when removing a wheel. Do not rely on jacks.
9
Make sure that no tools, loose parts or rags are left in or on the compressor.
5
Содержание XRVS455 Md
Страница 2: ...2 XRVS455 Md ...
Страница 26: ...26 XRVS455 Md ...