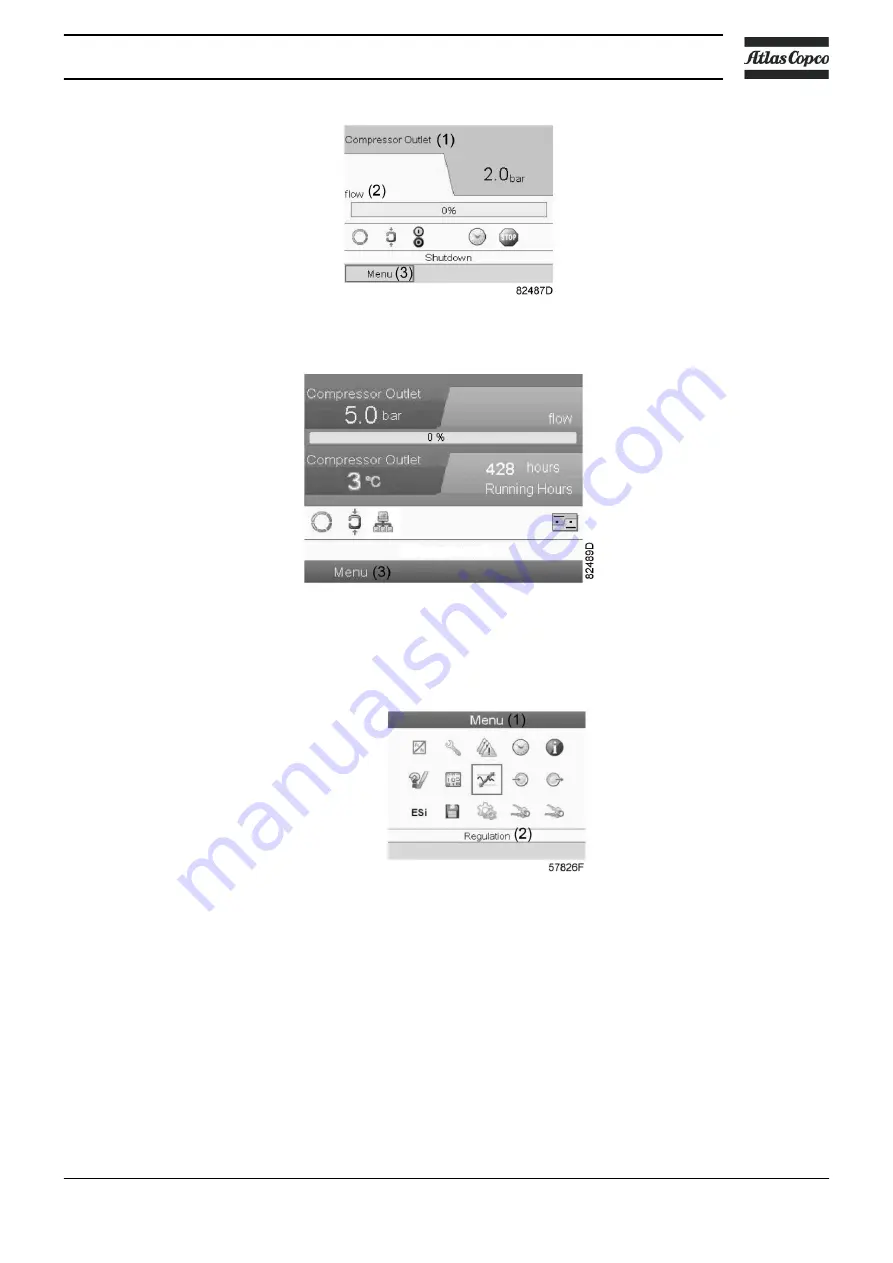
Typical Main screen (2 value lines), compressors with frequency converter
Typical Main screen (4 value lines), GA MED with frequency converter
• To go to the Menu screen, highlight the Menu button (3), using the Scroll keys.
• Press the Enter key to select the menu. Following screen appears:
• The screen shows a number of icons. Each icon indicates a menu item. By default, the Pressure Settings
(Regulation) icon is selected. The status bar shows the name of the menu that corresponds with the selected
icon.
• Use the Scroll keys to select an icon.
• Press the Escape key to return to the Main screen.
Instruction book
2920 7104 10
31
Содержание GA 11 VSD MED
Страница 2: ......
Страница 41: ...3 11 Service menu Control panel 1 Scroll keys 2 Enter key 3 Escape key Instruction book 2920 7104 10 39 ...
Страница 63: ...4 Installation 4 1 Dimension drawings Instruction book 2920 7104 10 61 ...
Страница 64: ...4 2 Installation proposal Instruction book 62 2920 7104 10 ...
Страница 102: ......
Страница 103: ......