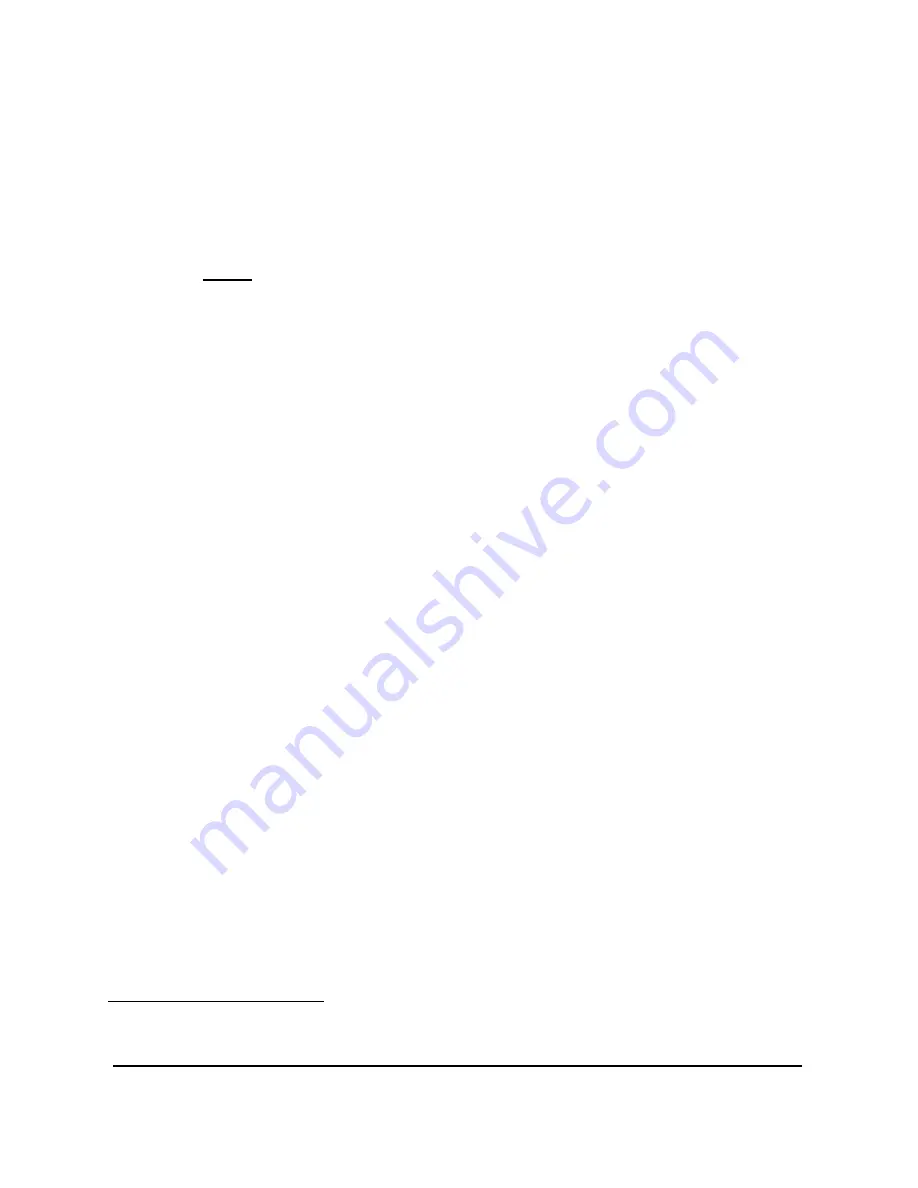
Quick-Change
Installation and Operation Manual
Document #9620-20-c-dkgm dkft-03
Pinnacle Park
•
1031 Goodworth Drive
•
Apex, NC 27539
•
Tel: 919.772.0115
•
Fax: 919.772.8259
•
www.ati-ia.com
•
Email: info@ati-
ia.com
C - 20
4. Operation
4.1 Recommended Sequence of Operation
This recommended Sequence of Operations procedure is to be used as a general guide when
programming a robot or PLC for use with a Tool Changer and DKG-M DKF-T control/signal modules.
This procedure is intended for "automatic" modes used during normal application processes.
Recommendations for operation in “teach” or “manual” modes where the operator has the teach pendant
in-hand will be addressed in a separate Troubleshooting Guide.
1.
Start
The robot and Tool Changer Master are free of the stand or storage location, the
Tool Changer is uncoupled and the Tool Changer locking mechanism may be fully
retracted (unlocked condition) or fully extended (missed Tool condition, i.e.,
Locked
and
Unlocked
inputs are false). The Tool is by itself in the Tool Stand.
a. The
RTL
inputs (RTL1 & RTL2) are false.
b.
RTLV
is false.
c. The ATI Tool and any downstream device is offline.
d. The
Input and Logic Power Good
is true.
The
Valve Power Available
input is true
provided the Switched AUX power supply is on.
e.
Tool Power is On
is false.
f.
TSIV
is false.
2. Unlock the Master. (This must be done prior to the Master entering the Tool to prevent the
ball bearings from impinging on the Tool bearing race.)
a. The
Latch
output command is made false and the
Unlatch
output command is made
true.
b. The
Unlocked
input goes true and remains true, indicating that the Tool Changer
locking mechanism is fully retracted and the
Unlatch
operation is complete.
3. Robot and Master move into the Tool, are parallel and within 0.125” to 0.06” of the Tool
(i.e., the module contact pins are touching, but the
RTL
sensors have not yet sensed the
targets on the Tool).
a. The
Tool Present
and
TSIV
inputs go true, indicating that the Master and Tool are in
close proximity of each other and verifying the operation of the
TSI limit switch
.
b. When the
Tool Present
input goes true,
Tool-ID
becomes available within 50ms.
c. Power is not yet available on the Tool. The bit “
Tool Power is On
” is false.
4. Robot and Master move within 0.06” of the Tool.
a. The
RTL
inputs are true, indicating that it is okay to couple the Tool.
b.
RTLV
is true.
5. Couple the Tool Changer.
a. The
Unlatch
output is made false and the
Latch
output is made true.
b. With the Latch output made true, Power becomes available on the Tool and the bit
“
Tool Power is ON
” turns on.
c. The
Unlocked
input goes false a short time later, indicating piston travel.
Subsequently, the
Locked
input goes true and remains true, indicating that the
coupling operation is complete.
d. Sometime thereafter3, communications should be established with the downstream
Ethernet device(s).
3 The time it takes to establish connection with a downstream EtherNet/IP node depends on the power up and
reconnect time of the individual EtherNet/IP equipment that is installed on the tool.