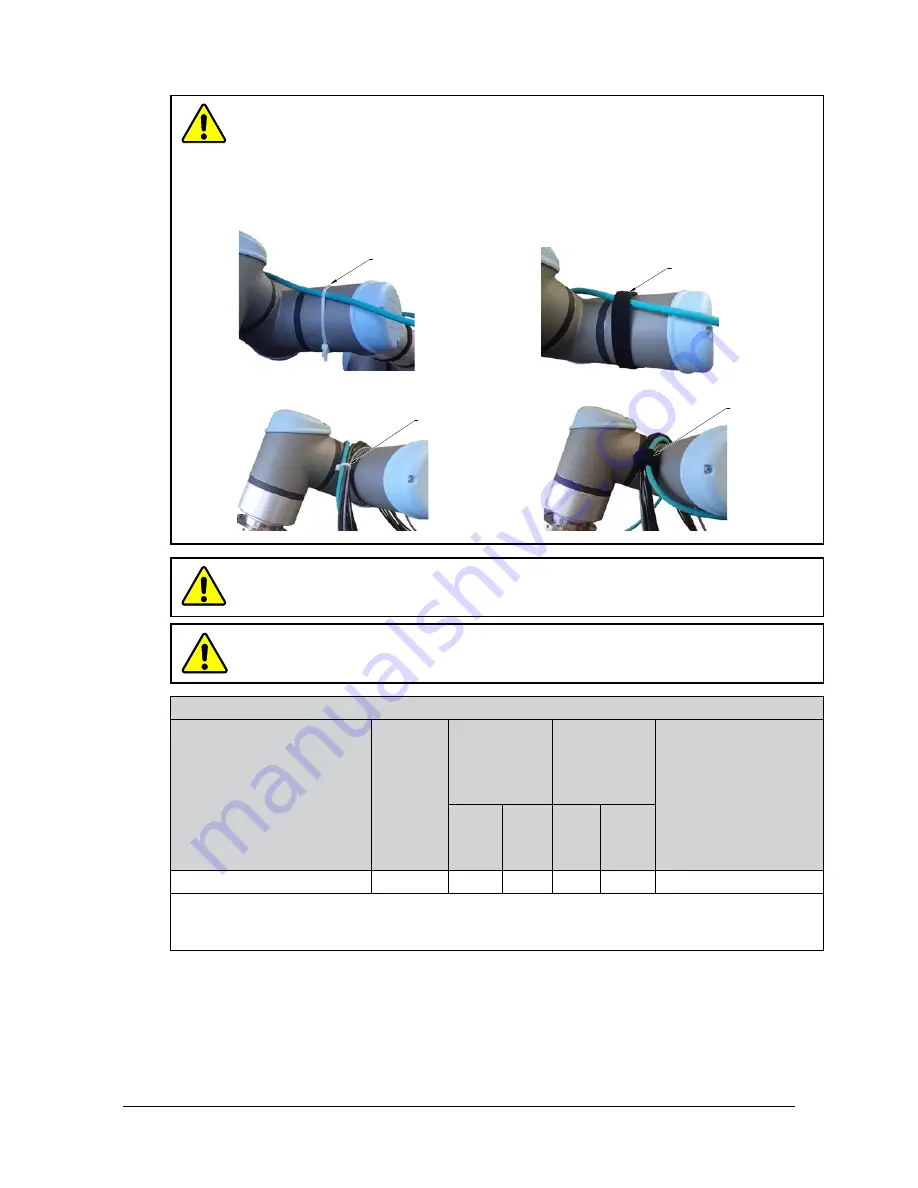
Manual, F/T Sensor, Serial Axia
Document #9610-05-Serial Axia-05
Pinnacle Park • 1031 Goodworth Drive • Apex, NC 27539 • Tel:+1 919.772.0115 • Fax:+1 919.772.8259 •
19
CAUTION:
Do not cable ties or zip ties to bundle cables or restrain the cable to the
robot arm. Directly affixing cable ties or zip ties to the cable jacket will prevent power
and signal communication between the F/T sensor and robot controller. Use hook
and loop or Velcro straps on the cable jacket surfaces. Examples of the incorrect and
correct methods to restrain or bundle cables are in the following pictures:
USE
Velcro
®
straps to restrain
the cable around the robot arm.
DO NOT
USE
zip ties to restrain
the cable around the robot arm.
INCORRECT
CORRECT
USE
Velcro
®
straps
to bundle cables.
DO NOT USE
zip ties
to bundle cables.
CAUTION:
Do not damage or crush the cable by over tightening the
straps on the cable.
CAUTION:
When routing the cables, do not bend less than the minimum bending
. A bend radius too small causes the cable to fail from
fatigue of the robot’s repetitive motion.
Table 3.1—Sensor Cable Bending Radius and Dynamic Twist Angle
Cable Part Number
Cable
Diameter
mm (in)
Static
Bending
Radius
(at room
temperature)
Dynamic
Bending
Radius
(at room
temperature)
Dynamic Cable Twist
Angle per Unit Length
mm
in
mm
in
9105-C-ZC33-ZC34-XXX
6.2 (.24)
31
1.3
62
2.5
180°/m or 55°/ft
Notes:
1.
Temperature affects cable flexibility. ATI recommends increasing the minimum dynamic bending radius for
lower temperatures.