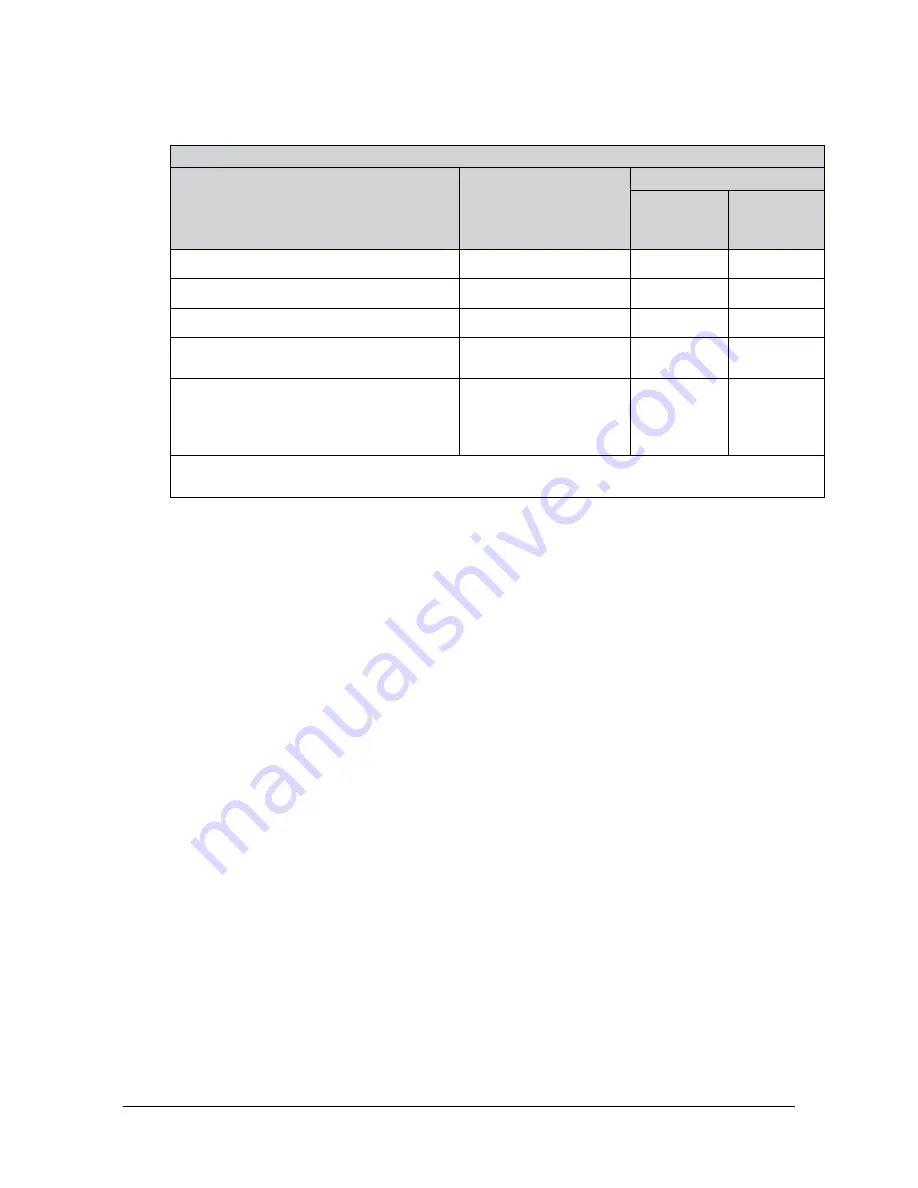
Manual, FT Sensor, ATI URCaps Software Installation and Setup for UR CB-Series
Document #9610-05-1036-07
Pinnacle Park • 1031 Goodworth Drive • Apex, NC 27539 • Tel: +1.919.772.0115 • Fax: +1.919.772.8259 •
8
2.1 ATI F/T Kits for Ethernet Axia
ATI provides the following kit options:
Table 2.2—ATI F/T Axia Kits
Item
P/N
ATI Kit P/N
9105-UR-
AXIA80
(
)
9105-UR-
AXIA80-S
(
)
Ethernet Axia F/T Sensor
9105-NET-AXIA80-M20
Mounting Interface Plate Assembly
9105-IP-2126
Tool Interface Plate Assembly
9105-IP-2191
Ethernet and Power Cable Kit
9105-CKIT-ZC22-
ZC28-4
Split Power and RJ45 Ethernet Cable:
8-pin M12 connector that splits to a RJ45
Ethernet connection and an unterminated
end for power
9105-C-ZC28-U-
RJ45S-4
Note:
1.
Part number used to be 9105-NET-AXIA80-M20-ZC22.
The mounting interface plate assembly (ATI P/N 9105-IP-2126) includes the following:
•
(1) interface plate (ATI P/N 3700-05-2126) that mounts the MAP to the robot arm
•
(6) M5-0.8 x 12 mm socket head cap screws (ATI P/N 3500-1064012-15) for mounting the sensor
to the interface plate
•
(4) M6-1 x 18 mm socket head cap screws (ATI P/N 3500-1066018-15) for mounting the interface
plate to the robot arm
•
(2) M4 x 12 mm dowel pins for aligning the sensor to the interface plate
•
(1) M6 x 12 mm dowel pin for aligning the interface plate to the robot
•
(1) clamp loop for routing the 9105-C-ZC22-ZC28-4 cable
•
(1) 4 mm low profile hex key (ATI P/N 3810-05-2182) for the M5 socket head cap screws
The tool interface plate assembly (ATI P/N 9105-IP-2191) includes the following:
•
(1) interface plate (ATI P/N 3700-05-2191) that mounts the TAP to the customer tooling
•
(6) M5-0.8 x 12 mm socket head cap screws (ATI P/N 3500-1064012-15) for mounting the
interface plater to the sensor
•
(1) M3 x 16 mm dowel pin for aligning the sensor to the interface plate
•
(1) M4 x 16 mm dowel pin for aligning the sensor to the interface plate
The Ethernet and Power Cable Kit (ATI P/N 9105-CKIT-ZC22-ZC28-4) includes the following:
•
(1) Ethernet and power cable (ATI P/N 9105-C-ZC22-ZC28-4) with a 6-pin sensor connector and
an 8-pin M12 connector
•
(1) L-bracket kit (ATI P/N 9005-05-1076) for cable routing
•
(1) P-clip kit and (6) cable straps for cable routing (ATI P/N 9005-05-1077)