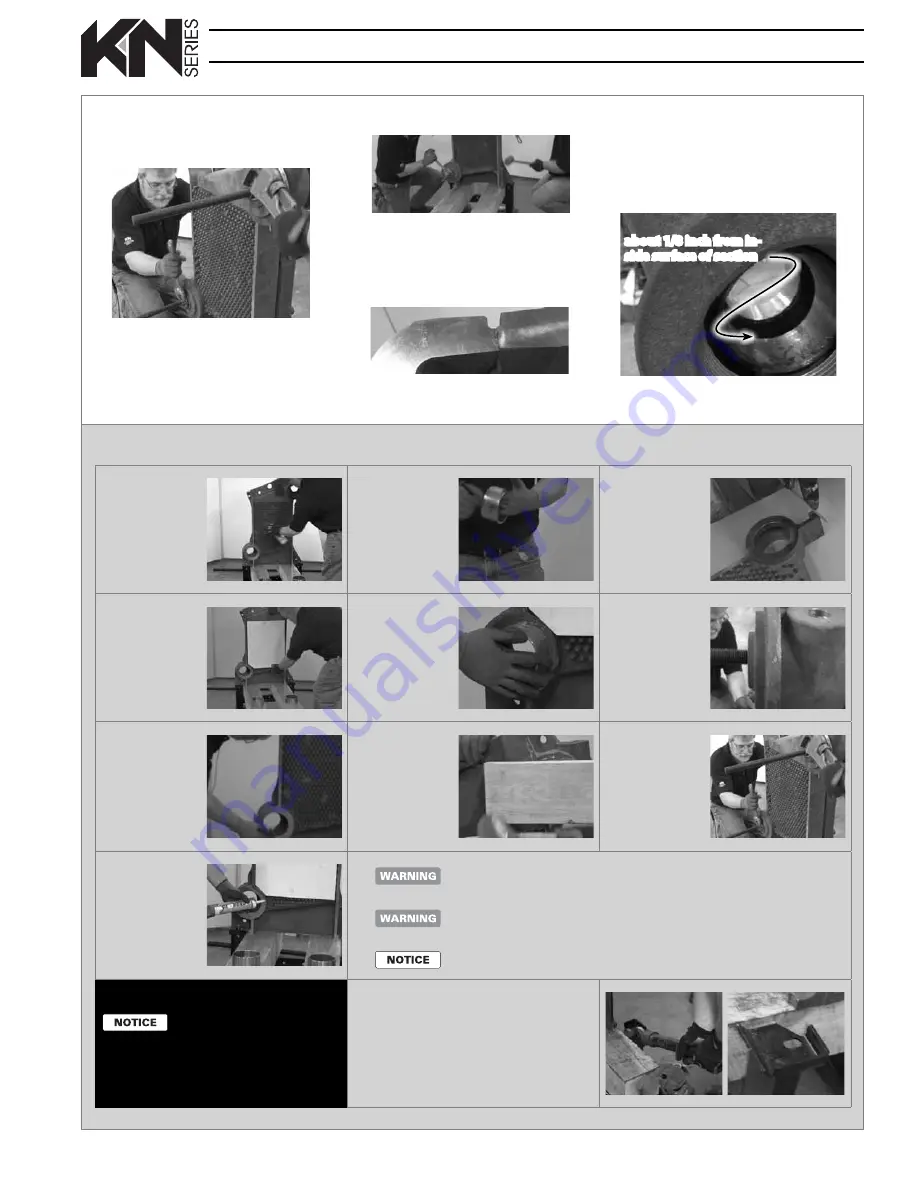
9
Gas-Fired Direct Vent Cast Iron Boilers – Field Assembly Instructions
Step 16
Draw sections together using draw rods and dead blow hammer
1. Use wrenches to pull the sections
together.
2. Alternate from one side to the other
during pull-up to avoid cocking the
nipple ports.
3. Use the dead blow hammer
to assist in the pull up.
4. The dead blow hammer will cause a
thud when struck against the section
until the sections are tight together.
When the draw up is complete, the
dead blow hammer should cause a
ringing sound from the block.
5. When the sections are properly pulled
up, they will be nearly metal-to-metal.
6. Look inside the nipple ports from the
end and inspect the push nipples. They
should be parallel with the section face
and about 1/8 inch from the inside
surface of the section.
Push nipple edge
Push nipple edge
about 1/8 inch from in-
side surface of section
f sectio
f section
Step 17
Install remaining intermediate sections and then the rear section (see previous pages for details)
Step 6
Apply adhesive for
ceramic fi ber fl ue
baffl
e
Step 11
Lubricate push
nipples with oil/
pipe dope mixture
(see Step 8)
Step 14
File lower edges of
next section
Step 7
Place ceramic fi ber
baffl
e in fl ueway
Step 12
Insert push nipples
Step 15
Install next section
and prepare draw
rods
Step 9
Lubricate nipple
ports
Step 13
Seat the push
nipples
Step 16
Draw sections
together using
draw rods and
dead blow
hammer
Step 10
Apply RTV to
machined surfaces
Read all instructions thoroughly and follow all WARNINGS and
NOTICES included in the steps referenced here.
Handle all sections with care to prevent any damage to
machined surfaces.
BLOCK ASSEMBLY SEQUENCE — See NOTICE on page 2.
Before attempting to install
the REAR SECTION, bend
down the tabs on the rear
legs as at right:
1. Bend down the end tabs on
the two rear legs at right. This is
required so that the rear section
can slid into position along the
runner beams. Use a hammer to
bend back into position after the
block assembly is completed.