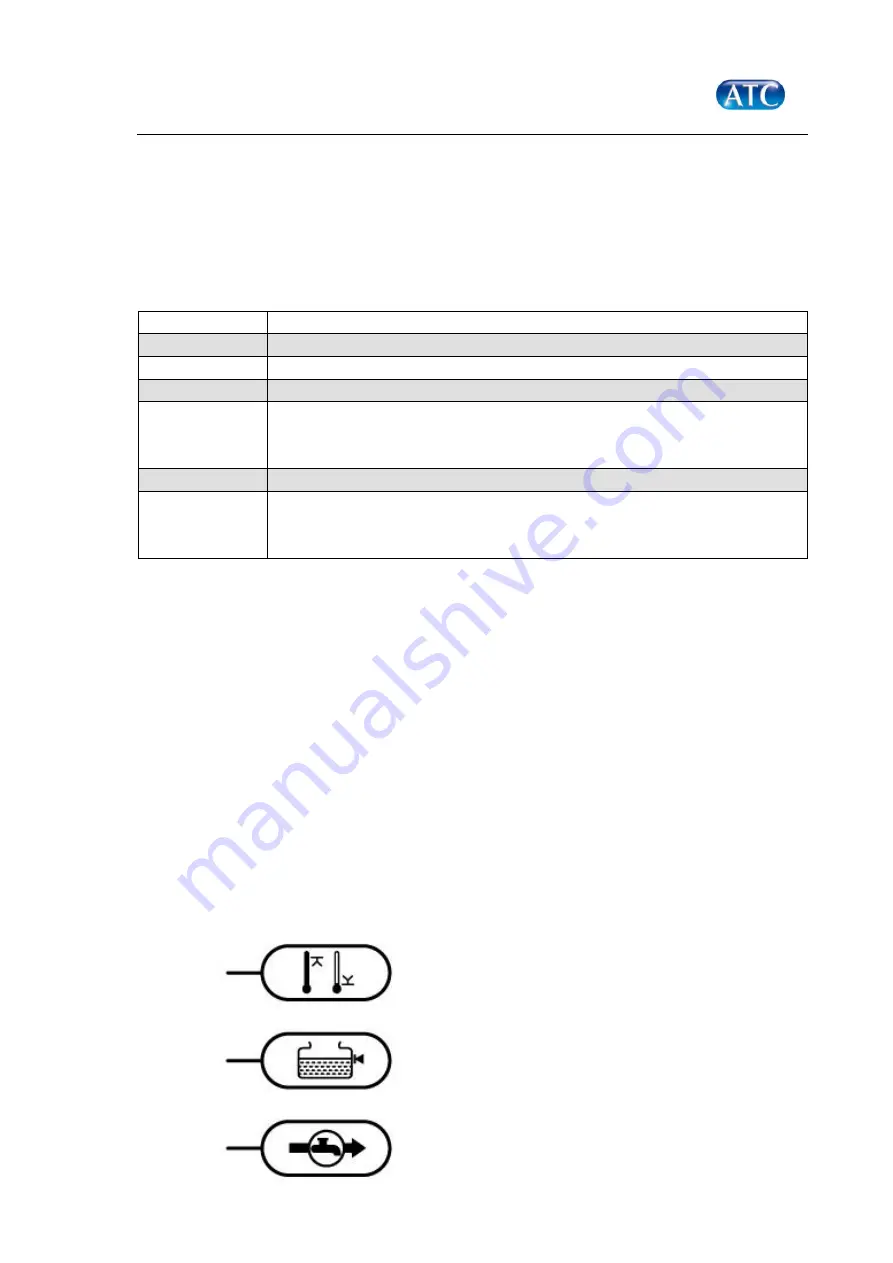
K1, K3 series chillers
–
Installation and Operation manual
Issue 10.24
Page 12
4.0 Maintenance and service requirements
Caution:
Failure to carry out service at the specified intervals may permanently damage your
equipment.
Interval
Actions
Weekly
Check fluid level
Monthly
Check the condenser (air intake) is free from obstructions or accumula-
tions of debris. Cleaning may be achieved with a domestic vacuum
cleaner with brush attachment.*
Annually
Change the fluid.
Check for fluid leaks throughout the whole system.
Check the condenser for fouling.
*
Caution:
Never blow the condenser out with compressed air.
4.1 Status lights and troubleshooting
The status panel on the front of your K series chiller is fitted with three amber lights, config-
ured such that ‘three ambers are good’; i.e. when they are lit, the parameter is operating
within design limits.
If an indicator light is not lit, this indicates an alert situation with the corresponding param-
eter, as follows:
TEMPERATURE
COOLANT LEVEL
COOLANT FLOW
Содержание K-Series
Страница 2: ......
Страница 16: ...K1 K3 series chillers Installation and Operation manual Issue 10 24 Page 14 ...
Страница 21: ......