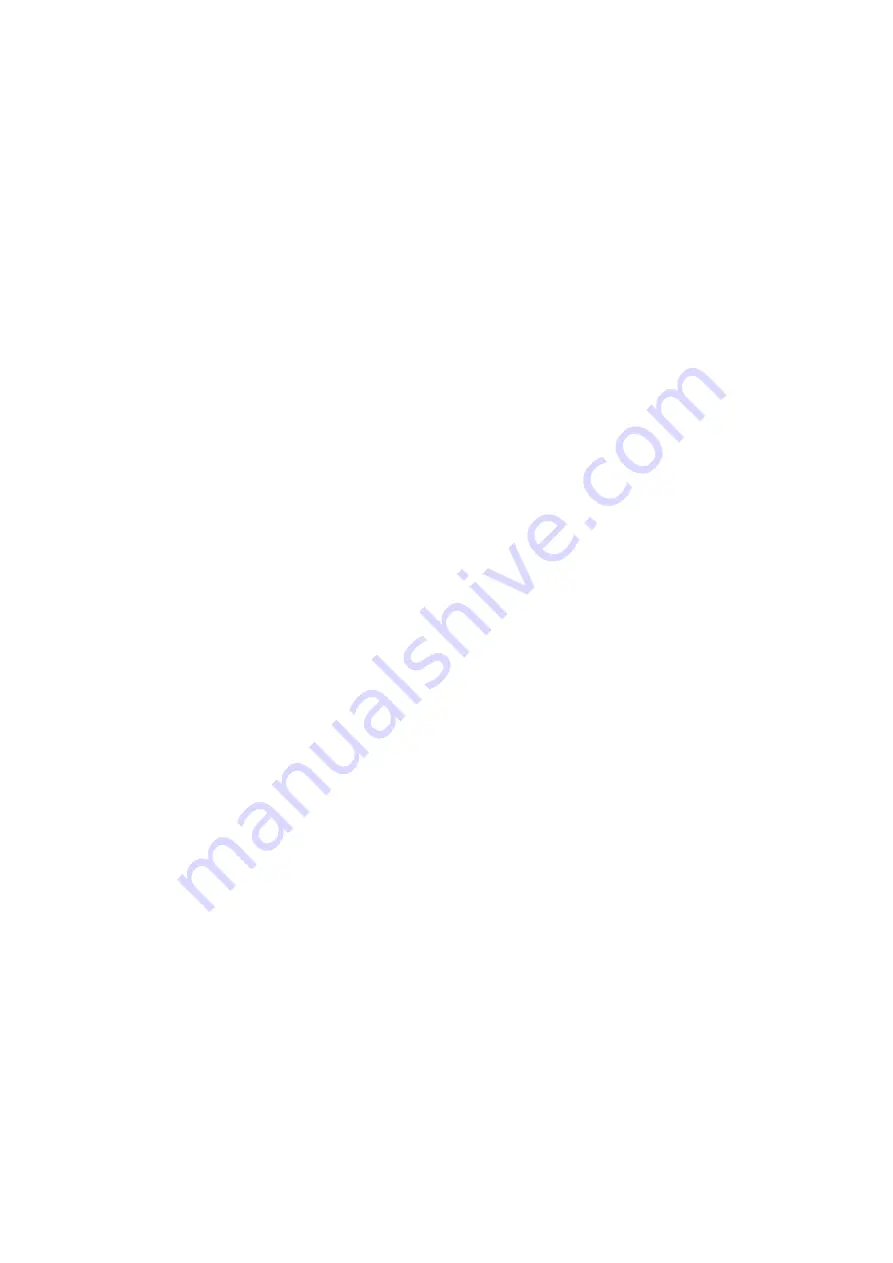
General Overview
The extraction (leaching) of a substance from a solid material with the aid of a liquid
is a common process in chemical engineering which can be applied to appropriate
biological, inorganic and organic substances. A familiar activity which illustrates this
process is the making of tea or coffee, where hot water is used to perform the
extraction from tea leaves or coffee beans. Other examples are the extraction of
sugar from sugar beet using hot water and the extraction of oils from seeds using
organic solvents such as hexane, acetone or ether.
For the solid/liquid extraction process to be appropriate, the substance to be
extracted (tea) must be soluble while the solid phase (tea leaves) must be insoluble
in the chosen solvent (hot water). The appropriate solvent is introduced to the solid
material and the two remain in contact while the soluble component dissolves into the
solvent. The solvent containing the dissolved substance (the miscella) is then drained
from the insoluble solid. This is the basis of all solid/liquid extraction processes.
Further processing may be required to recover the extracted substance from the
solvent.
Before performing solid/liquid extraction the solid material must be prepared by
crushing, grinding or cutting, as appropriate, to allow adequate contact between the
solvent and the soluble component. The amount of preparation will depend on the
amount and distribution of the soluble component within the solid and the nature of
the solid (how easily diffusion can occur).
Numerous different types of solid/liquid extractors may be employed to perform the
basic task of introducing the solvent to the material to be extracted. The extraction
process may involve batch operation (fixed-bed) with the addition of open loop or
closed loop circulation of the solvent. Alternatively extraction may be a continuous
operation (moving-bed) with single or multi-stage processing involving co-current flow
or counter current flow of the solvent and the soluble material to be extracted. In
large scale industrial solid/liquid extraction systems economic factors frequently lead
to the use of the more sophisticated multi-stage counter current flow systems due to
their high extraction efficiency.
The Armfield UOP4 MkII is designed to demonstrate a simplified version of the
moving-bed leaching process used by many industrial solid/liquid extraction systems.
The process used is a continuous multi-stage process, which gives counter current
flow of the solvent and the solid phase. A batch extraction vessel is also incorporated
to allow demonstration of fixed-bed leaching with either open or closed loop
circulation of the solvent. The recommended process for the UOP4 MkII is the
extraction of Potassium Bicarbonate from a solid carrier of porous polymer pellets
using water as the solvent.
2
Содержание UOP4 MKII
Страница 1: ...SOLID LIQUID EXTRACTION UNIT Instruction Manual UOP4 MKII ISSUE 16 November 2010...
Страница 4: ......
Страница 7: ...Equipment Diagrams Figure 1 Front View of UOP4 MKII Solid Liquid Extraction Unit 3...
Страница 8: ...Armfield Instruction Manual Figure 2 Side View of UOP4 MKII Solid Liquid Extraction Unit 4...
Страница 9: ...Equipment Diagrams Figure 3 UOP4 MKII Schematic Diagram Showing 3 Stage Process 5...
Страница 10: ...Armfield Instruction Manual Figure 4 UOP4 MkII Console Front View 6...
Страница 11: ...Equipment Diagrams Figure 5 UOP4 MkII Console Rear View 7...
Страница 12: ...Armfield Instruction Manual Figure 6 PCB Connections 8...