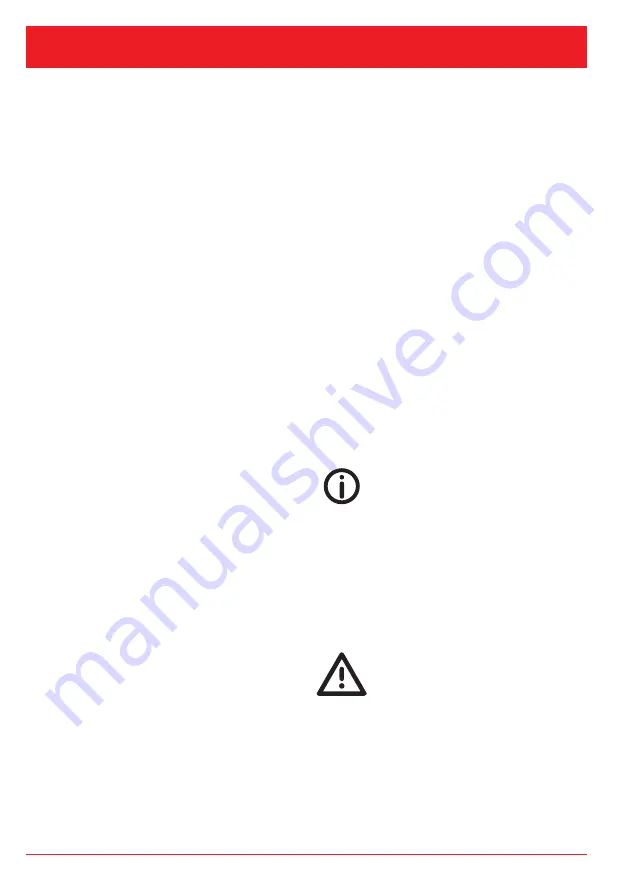
B00-100
• B1 • 09/22 • GB • p. 6 of 20 • www.armano-messtechnik.com
Operating Instructions Pressure Gauges
Selection Criteria, Measuring Arrangements, Installation and Operation Manual
The influence of temperature changes on the indication
mainly depends on the temperature coefficient of the
modulus of elasticity of the Bourdon tube.
Depending on the material used, the temperature-related
error is between 0.3 % and 0.4 % per 10 K.
Diaphragm pressure gauges:
Diaphragms are circularly shaped corrugated mem-
branes. The pressure to be measured acts on one side
of the diaphragm. The deflection of the diaphragm is a
measure for the pressure. Diaphragms have a relatively
high restoring force. Therefore, the influence of addi-
tional accessories is lower compared to Bourdon tube
pressure gauges. Due to the annular fixing arrangement
of the diaphragm, they are less sensitive to vibrations.
Diaphragms can be protected against high overload
by supporting the measuring element. They can be
protected against corrosive media by applying coatings
or foils. Diaphragm pressure gauges are also favourable
for highly viscous or crystallising media, since wide
connection bores, open connection flanges or flushing
orifices allow for cleaning options.
There are pressure gauges with horizontal diaphragm
and pressure gauges with vertical diaphragm, i.e. the
diaphragm is placed parallel to the dial. For pressure
ranges < 0.6 bar, generally diaphragms with a diameter
of 160 mm are used, whereas for higher pressure ranges
diaphragms with a diameter of 100 mm are used. Due
to the annular fixing arrangement of the diaphragm, the
indication deviation caused by temperature changes is
significantly higher compared to Bourdon tube pressure
gauges. Diaphragm pressure gauges are applied for
pressure ranges from 10 mbar to 25 bar with accuracy
classes of 1.6 and 2.5, rarely also of 4.0.
Capsule gauges for low pressure:
A diaphragm capsule consists of two circularly shaped
corrugated membranes or a membrane and a base
plate, which are assembled pressure-tight at the edge.
The measurement pressure is passed into the centre of
one of the membranes and acts onto the inside of the
diaphragm capsule. The lifting movement generated
hereby is a measure for the pressure.
Capsule gauges for low pressure are not suitable for
liquid media.
They can be applied for pressure ranges from 2.5 mbar
to 600 mbar with accuracy classes from 0.6 to 1.6.
The indication deviation caused by temperature chang-
es can be between 0.3 % and 0.4 % per 10 K, depending
on the material.
4.2
Pressure Ranges
The operating pressure should be within the middle
third of the pressure range specified for the pressure
gauge. The maximum pressure load should not exceed
75 % of the full scale value at steady load or 65 % of the
full scale value at dynamic load (
DIN EN 837-2).
4.3
Error Limits
The error limits for pressure measuring instruments are
defined in DIN EN 837-1 (Bourdon tube pressure gaug-
es) and DIN EN 837-3 (capsule gauges and diaphragm
pressure gauges).
• Pressure measuring instruments with classes 0.1
to 0.6 and higher are preferably used in laboratories
and workshops for precise measurements.
• Pressure measuring instruments with classes 1.0
and 1.6 are used for measurements on machines
and in production facilities.
• Pressure measuring instruments with classes 2.5
and 4.0 are used for monitoring tasks without spe-
cial accuracy requirements.
4.4
Operating Conditions
When selecting pressure measuring instru-
ments, attention should be paid on the se-
lection criteria and installation recommen-
dations according to DIN EN 837-2 as well
as the information provided in this manual
(
chapters 4.4.1, 4.4.2 and 6.). The appli-
cation of pressure measuring instruments
that are not suited for the actual operating
conditions may cause considerable conse-
quential damage.
4.4.1 Medium Properties, Pressure Profile
CAUTION! Material damage!
Rapid pressure changes or pressure strokes
must not act abruptly on the measuring ele-
ment. Pressure strokes must not exceed the
pressure limits of the pressure measuring
instruments.
If required, upstream overload protection devices
(
chapter 5 “Additional Accessory”) shall be provid-
ed. Pressure changes of > 10 % of the full scale values
per second impair the reading of the measured values.
Moreover, this severely reduces the service life of the
devices. In such cases, attenuators must be provided.