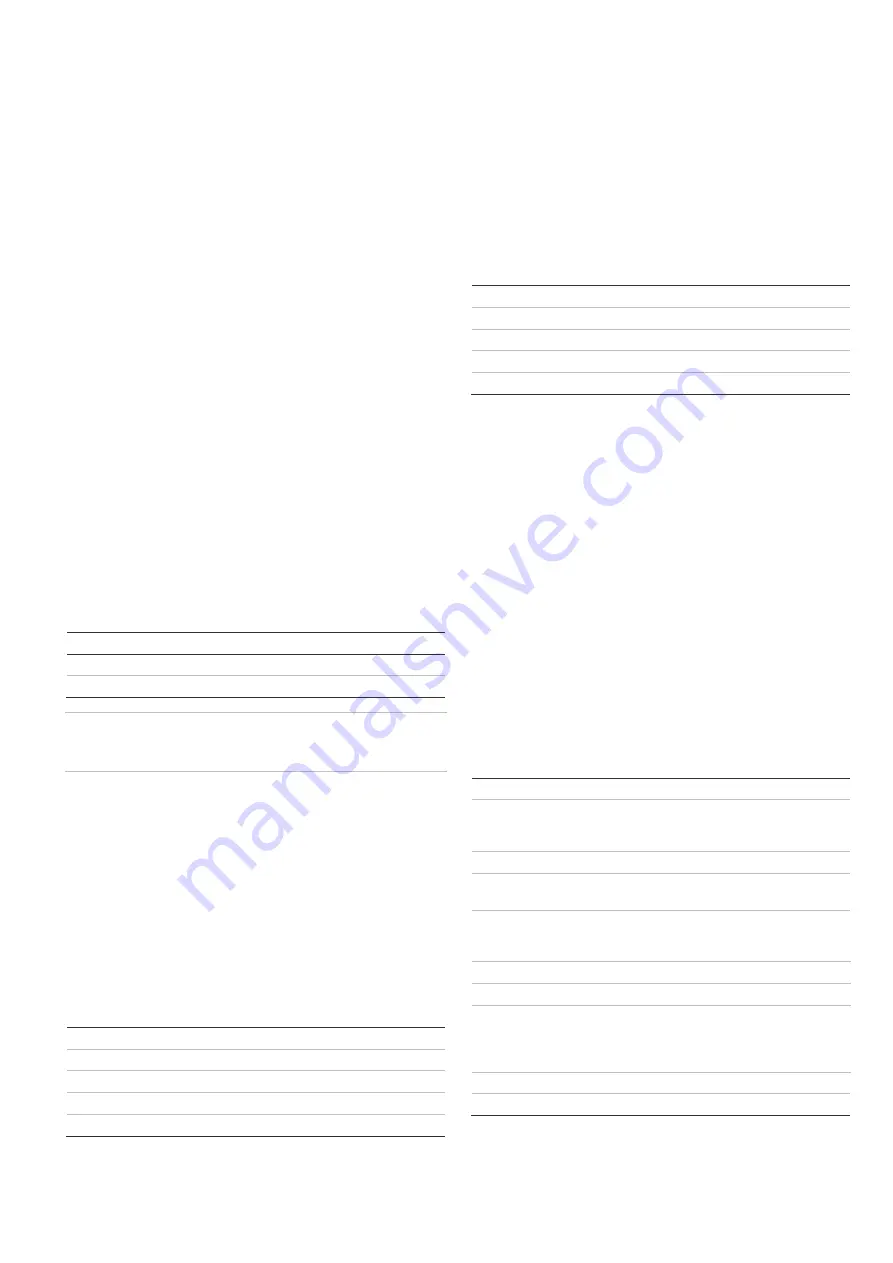
P/N 10-5106-501-55NC-01 • 19FEB19
3 / 4
Assembly
Install the module into the protective housing as shown in
Figure 1. Connecting cables should be fed through the cable
entry hole at the rear of the protective housing before the
module is fixed into place.
Addressing
Each module must be assigned an address from 1 to 128. Use
the rotary dial marked 0 to 12 to set the tens and hundreds part
of the address, and the rotary dial marked 0 to 9 for the
remaining digits. See Figure 5 for example address settings.
Note:
To overcome the mechanical effects of shipping and
storage, we recommend that you first rotate each dial counter-
clockwise (to the 0 position) and then clockwise (to the dial’s
maximum position) before setting the required address.
To change the address of a module that is operational:
1. Disconnect the module from the loop.
Wait at least 5 seconds for the module to completely
power down.
2. Change the address on the module using the rotary dials.
3. Connect the module to the loop.
4. Configure the device at its new address, and then remove
the old device address at the panel.
Configuration
The module operation mode (standard or IS) is configured
using jumpers J4 and J5, as shown in the table below. The
default configuration is for standard operation (non-IS).
Jumper
Standard
Intrinsically safe
J4
On
Off
J5
Off
On
Caution:
Always check the jumper configuration to ensure that
it is correct for your installation type (standard or intrinsically
safe).
Wiring
Standa
rd installation wiring (non-IS)
Connect the module to the addressable loop using the COM1
(negative) and COM2 (positive) inputs, as shown in Figure 2.
COM1 and COM2 are polarity sensitive.
For conventional zone output wiring for standard applications,
see Figure 3. The conventional zone output requires a
3.9 kΩ
end-of-line resistor.
Conventional loop impedance/loads for standard installation
are shown in the table below.
Short circuit
< 40 Ω
Fire
130
Ω to 760 Ω
Fault
1.1 kΩ to 1.4 kΩ
Normal*
2.1 kΩ to 4.5 kΩ
Open circuit
> 7.5 kΩ
* Including all devices and the 3.9 kΩ EOL resistor.
Intrinsically safe installation wiring
Connect the module to the addressable loop using the COM1
(negative) and COM2 (positive) inputs, as shown in Figure 2.
COM1 and COM2 are polarity sensitive.
For conventional zone output wiring for IS applications, see
Figure 4.
The conventional zone output requires a 3.9 kΩ end-
of-line resistor.
Never install standard conventional detectors behind the IS
barrier.
Conventional loop impedance/loads for IS installation are
shown in the table below.
Short circuit
< 26 Ω
Fire
250 Ω to 450 Ω
Fault
680 Ω to 1 kΩ
Normal*
1.6 kΩ to 4 kΩ
Open circuit
>
7 kΩ
* Including all devices and the 3.9
kΩ EOL resistor.
Maintenance
Basic maintenance consists of a yearly visual inspection. Do
not modify internal wiring or circuitry.
The wire impedance and threshold levels should also be
checked as follows:
•
Change EOL resistor to 330
Ω and check that the system
reports an alarm.
•
Change EOL resistor to 0
Ω and check that the system
reports a fault.
•
Change EOL resistor to open and check that the system
reports a fault.
•
Restore the EOL resistor to
3.9 kΩ and check that the
system operates normally.
Specifications
Loop operating voltage
21 to 28 VDC
Loop current consumption
Standby
Alarm
< 15 mA
< 40 mA
Remote LED current
3.6 mA
Zone operating voltage (in
standby)
17.5 to 18.5 VDC
Zone cable resistance
Standard installation
IS installation
< 40
Ω
< 26
Ω
Zone end-of-line resistor
3.
9 kΩ, 5%, 1/4W
IP rating
IP40
Operating environment
Operating temperature
Storage temperature
Relative humidity
−10 to +55°C
−20 to +60ºC
10 to 95% noncondensing
Weight
325 g
Dimensions
175 × 124 × 51 mm