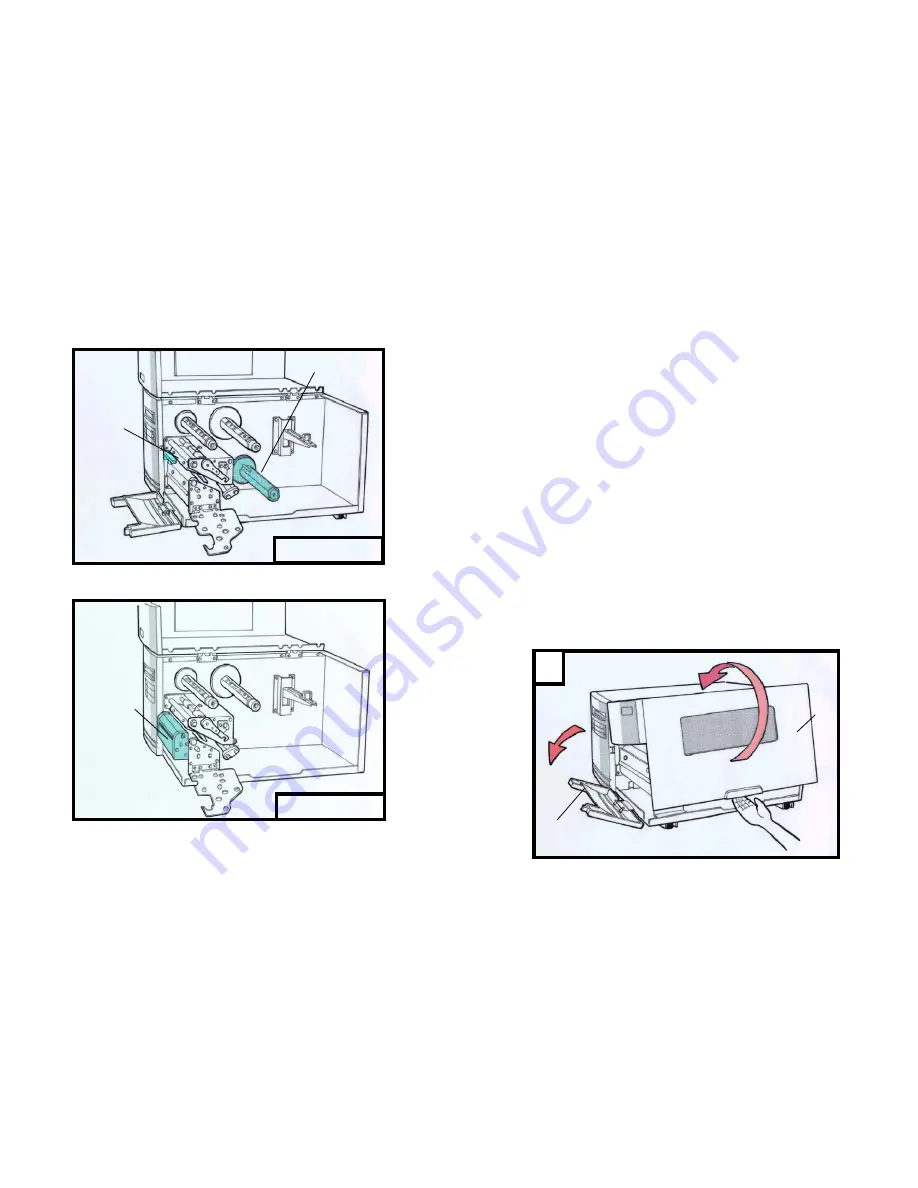
Loading the Ribbon
Reminder
Notes:
Peeler
Sensor
1. This section is applicable to the transfer thermal printing.
2. Attached ribbon is coating inside.
1. Lift the top access door and the front access door to expose the
compartment. ( Figure 1 )
2. Push the head latch by anti-clockwise, and then fold the bracket.
( Figure 2 )
3. Unwrap the ribbon roll pack and separate the ribbon roll and the bare
core.
4. Insert the ribbon roll into the ribbon supply spindle. ( Figure 3 )
5. Lead the bare core through the print head module. ( Figure 4 )
Peel Off Mode
6.
Attach the edge of the ribbon on the bare core and wind it a little bit
onto the core.
Note:
The
coating
side of the ribbon should be faced down.
7. Insert the bare core into the ribbon pick-up spindle. ( Figure 5 )
8. Turn the pick-up spindle to ensure the ribbon is tightly wound.
Cutter Mode
Cutter
8
Top Cover
Front Access
1
Door
7