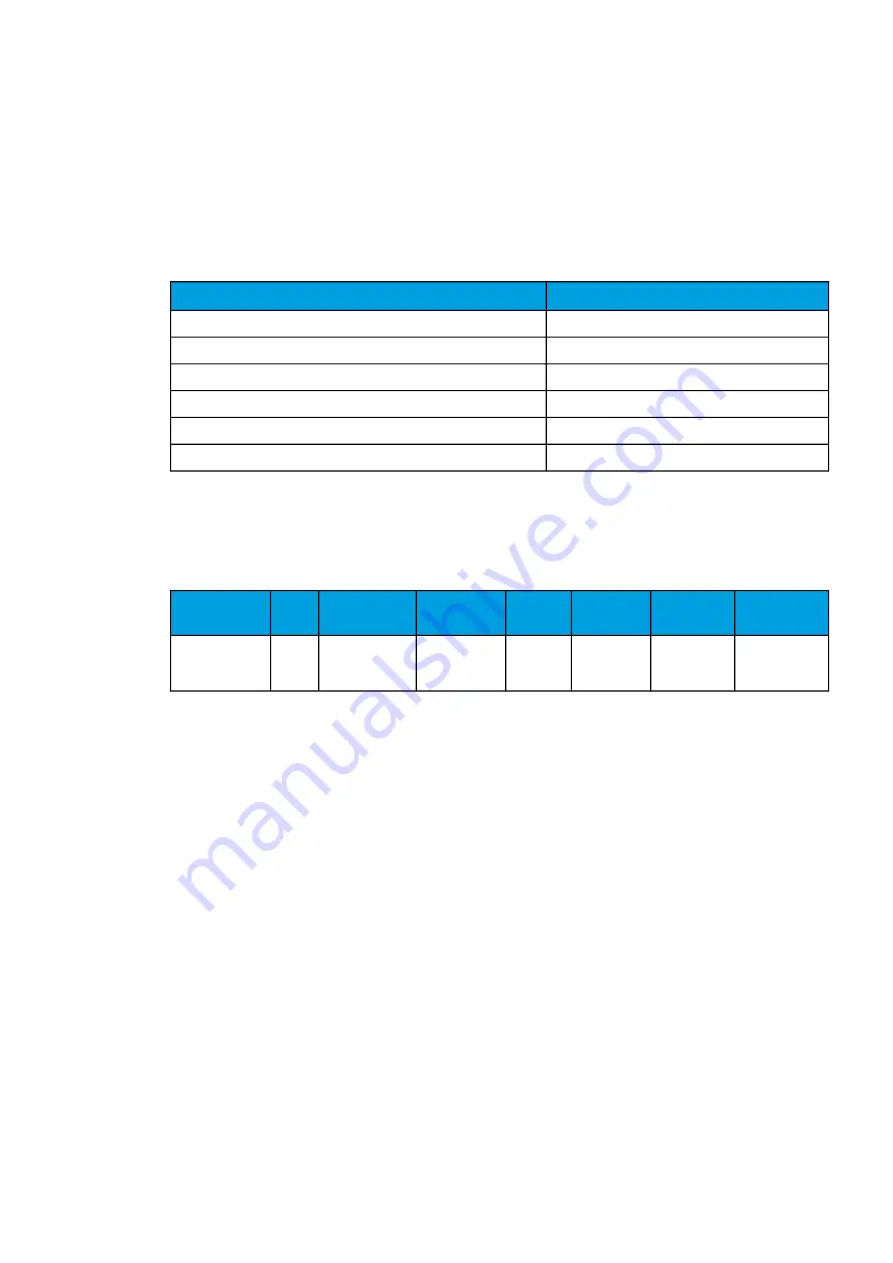
Events and registers
The undercurrent function (abbreviated "NUC" in event block names) generates events and registers
from the status changes in START, TRIP and BLOCKED. The user can select which event messages
are stored in the main event buffer: ON, OFF, or both.
The events triggered by the function are recorded with a time stamp and with process data values.
Table. 5.3.20 - 172. Event messages.
Event block name
Event names
NUC1
Start ON
NUC1
Start OFF
NUC1
Trip ON
NUC1
Trip OFF
NUC1
Block ON
NUC1
Block OFF
The function registers its operation into the last twelve (12) time-stamped registers. The register of the
function records the ON event process data for START, TRIP or BLOCKED. The table below
presents the structure of the function's register content.
Table. 5.3.20 - 173. Register content.
Date and time Event
Fault type
Pre-trigger
current
Fault
current
Prefault
current
Trip time
remaining
Used SG
dd.mm.yyyy
hh:mm:ss.mss
Event
name
L1-G…L1-L2-L3
Start/
Trip -20ms
current
Start/Trip
current
Start
-200ms
current
0 ms...1800s
Setting group
1...8 active
5.3.21 Mechanical jam protection (Im>; 51M)
The mechanical jam protection function is used for monitoring motor loading after motor starting. When
a motor-run apparatus jams during its work load, this function can be used to disconnect the motor
from the feeding network in order to avoid further damage to the motor drive. The function is active
only after the motor has started, and it is blocked during motor starting. This is done through
an internal connection of
Motor running and through a Motor starting signal taken from the Motor
status monitoring function. This function operates similarly to the motor starting/locked rotor function
(Ist>; 48/14) although it operates on Definite Time delay and does not work during motor starting. Also,
with the help of a dedicated locked rotor function and mechanical jam protection the user can divide all
possible fault situations based on a quick definition of the fault types in relay events. Additionally, the
Ist> function's setup can be problematic with heavy inertia loads that experience a locked rotor
situation during work load. Having separate functions for start-up and for mechanical jams divides the
situations clearly; for example, the mechanical jam protection can be set to instant operation while the
locked rotor function allows motor starting several tens of seconds.
The load jam protection function uses a total of eight (8) separate setting groups which can be
selected from one common source.
The function can operate on instant or time-delayed mode. In the time-delayed mode the operation can
be set to definite time (DT) delay.
The inputs for the function are the following:
• setting parameters
A
AQ
Q-M255
-M255
Instruction manual
Version: 2.06
© Arcteq Relays Ltd
IM00020
207
Содержание AQ-M255
Страница 1: ...AQ M255 Motor protection IED Instruction manual...
Страница 2: ......
Страница 384: ...Figure 7 4 189 Example block scheme A AQ Q M255 M255 Instruction manual Version 2 06 382 Arcteq Relays Ltd IM00020...
Страница 405: ...Figure 8 14 211 Device installation A AQ Q M255 M255 Instruction manual Version 2 06 Arcteq Relays Ltd IM00020 403...