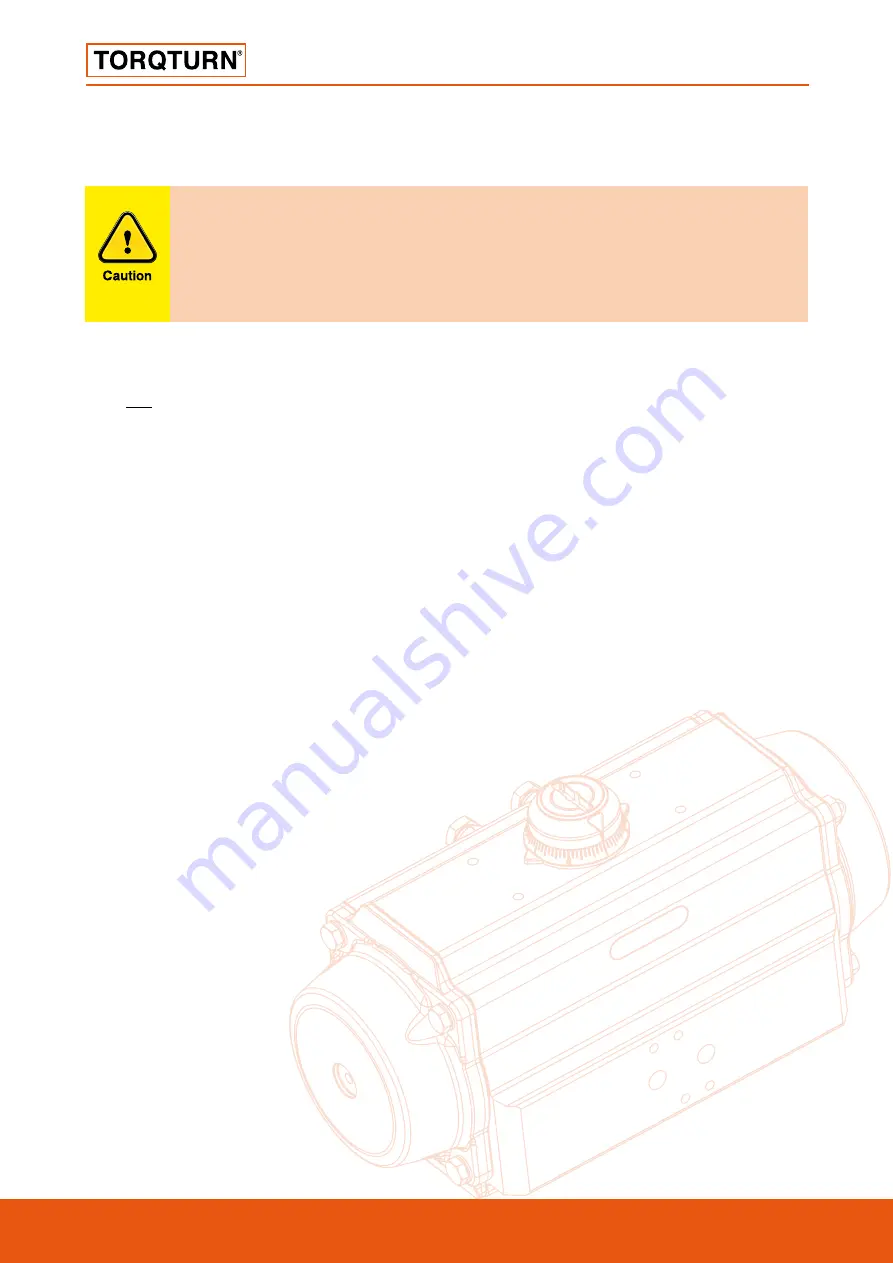
ACTUATORS - RP SERIES
Australian Pipeline Valve - Installation, Operation and Maintenance Manual
9
4.4 ACTUATOR SIZING
4.4.1 General Sizing Rules for Soft Seated Ball Valves
Valve and actuator torque values published are theoretical, however where required APV will perform a
torque test prior to despatch. The real valve torque value can be higher depending upon the following
listed factors as these factors can drastically increase (or decrease) the torque of soft seated ball valves.
These factors will have a similar effect on soft seated butterfly valves. Metal to metal seated ball,
butterfly and plug valves will also be effected but the torque implications will vary.
1) Fluid carrying dust, powder, abrasive particles (+50% to 125%). In extreme cases can be higher. i.e. Up
to 200%.
1a) Slurry, pulp, resins, paste (+50%) can be much higher in some cases.
2) Dry service (Dry Gas) (+30%).
3) High or low temperature (consult us).
4) Infrequent use (+30-50%) *1 - *2.
5) If a higher minimum air supply than used in the calculation is available more torque will be produced
in the air operation phase, (do not exceed maximum air capacity of the actuator).
6) Torque is based on a maximum Delta P for class. If your actual working pressure is lower please
advise as a smaller actuator may be possible.
7) Lubricated service (clean oil or other high lubricity fluid) (+15%).
*1 PTFE/RPTFE seats can require more torque to unseat after a period of time due to it’s fluidity &
‘memory’. For Devlon/Nylon Seat the valve torque is higher and PEEK® is even higher (of course this should
be factored into torque of valve where applicable), however as these are harder materials (especially
PEEK®) infrequent use has a lesser effect on the increase in torque.
*2 Where set fail closed, additional infrequent use safety factor only needs to be applied to spring stroke
torques. Allow additional 50% safety factor if valve is being operated less than once per month.
4.4.2 Actuator Sizing for Ball Valves
Use the following ‘ready reckoner’ rough estimating guide* to calculate the torque values required to
turn a ball valve through it’s 90
°
travel. Consider torque requirements at these five basic positions:
BTO - Break open torque: the torque required to unseat the closed valve. 100% of the stated torque.
RTO - Opening torque: the torque needed to move the valve to the fully open position. Average 70% of
stated BTO torque*.
ETO - Open breakout torque: the torque required to move the valve from the fully open position. 70% of
All factors shown in section 4.4.1 to 4.4.3 are only estimating guides and are based
more on common smaller sizes valves. It is impossible to accurately estimate the
effect on torque all the below factors will have. However, section 2.5.1 to 2.5.3
provide a rough guide and serve as a warning to ensure users are aware of the
dramatic affect all the below factors can have on torque.