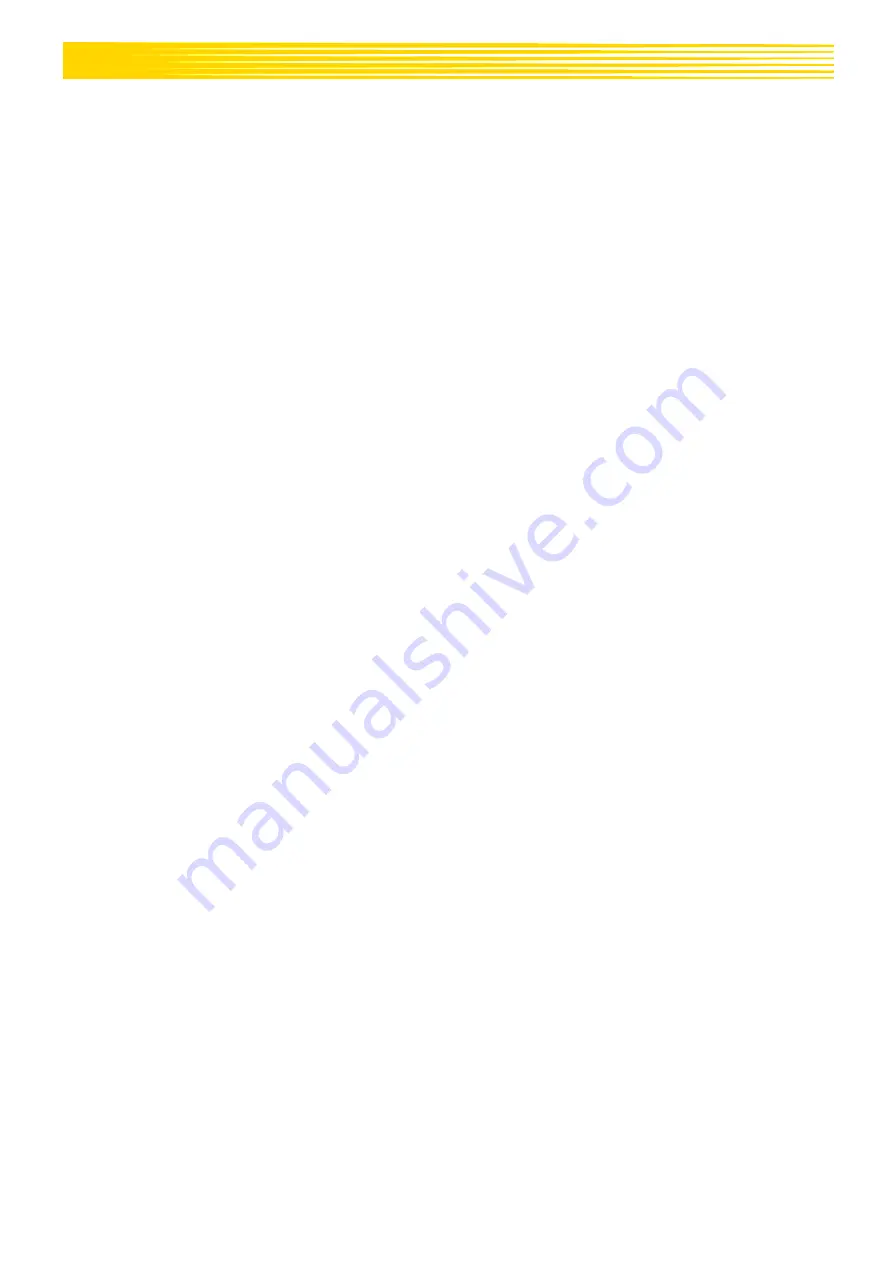
17
8
MAINTENANCE AND CARE
8.1
GENERAL MAINTENANCE INSTRUCTIONS
To maintain the implement in good condition even after a long service life, the following instructions must
be observed:
In Point 5, you will find some basic safety regulations for maintenance work.
Original parts and accessories are designed especially for the machines or implements.
Please note that original spare parts and original accessories not supplied by us have also not been
tested and approved by us.
The installation or use of such products can therefore possibly negatively change or impede the
constructional properties of your implement. The manufacturer rules out any liability for damages
resulting from the use of non-original parts and accessories.
The manufacturer is not liable for any unauthorised modifications to the implement and the use of
components and auxiliary parts on the implement that were not purchased from APV.
Before every operation, check the hydraulic hose lines for wear, damage and ageing. Damaged
or faulty parts must be immediately replaced.
When replacing the hydraulic hose lines, original spare parts must be used that comply with the
technical requirements of the implement manufacturer.
Caution! Liquids escaping under high pressure can penetrate the skin. For this reason, a physician
must be consulted immediately in case of accident!
After cleaning, lubricate all of the grease points and distribute the grease evenly in the bearing points
(e.g. perform a short test run).
Do not use a high pressure cleaner to clean bearing and hydraulic parts.
The paint can be damaged by cleaning with excessive pressure.
During the winter, the implement should be protected against corrosion with an environmentally-
friendly product.
Park the implement protected from weather conditions.
Put down the implement in a way that the tines are not needlessly strained.
Hydraulic hose lines must be replaced at the latest 6 years after their manufacturing date. The
manufacturing date of the hydraulic hose lines is specified on the fittings.
Hydraulically as well as mechanically folded implement must only be parked in a folded state.
The hydraulic system must be inspected at least once a year by specialist personnel.
8.2
REGULAR MAINTENANCE INSTRUCTIONS
All bolted connections should be re-tightened at the latest after 3 operating hours and again after 20
hours, and then checked regularly. Loose bolts can cause significant consequential damage, which is
not covered by the warranty.
The grease points on the joints and bearings must be lubricated regularly (approx. every 10 operating
hours with universal grease).
After the first 10 operating hours and subsequently every 50 operating hours, the hydraulic units, hoses
and couplings as well as tube lines must be checked for leaks and the bolted connections must be
tightened if necessary.
Occasionally check the tyre inflation pressure (2.1 bar).
The platform kit and its access ladder must be visually inspected on a regular basis.
The rubber for fastening the access ladder of the platform kit must be checked regularly for wear and
replaced if necessary.