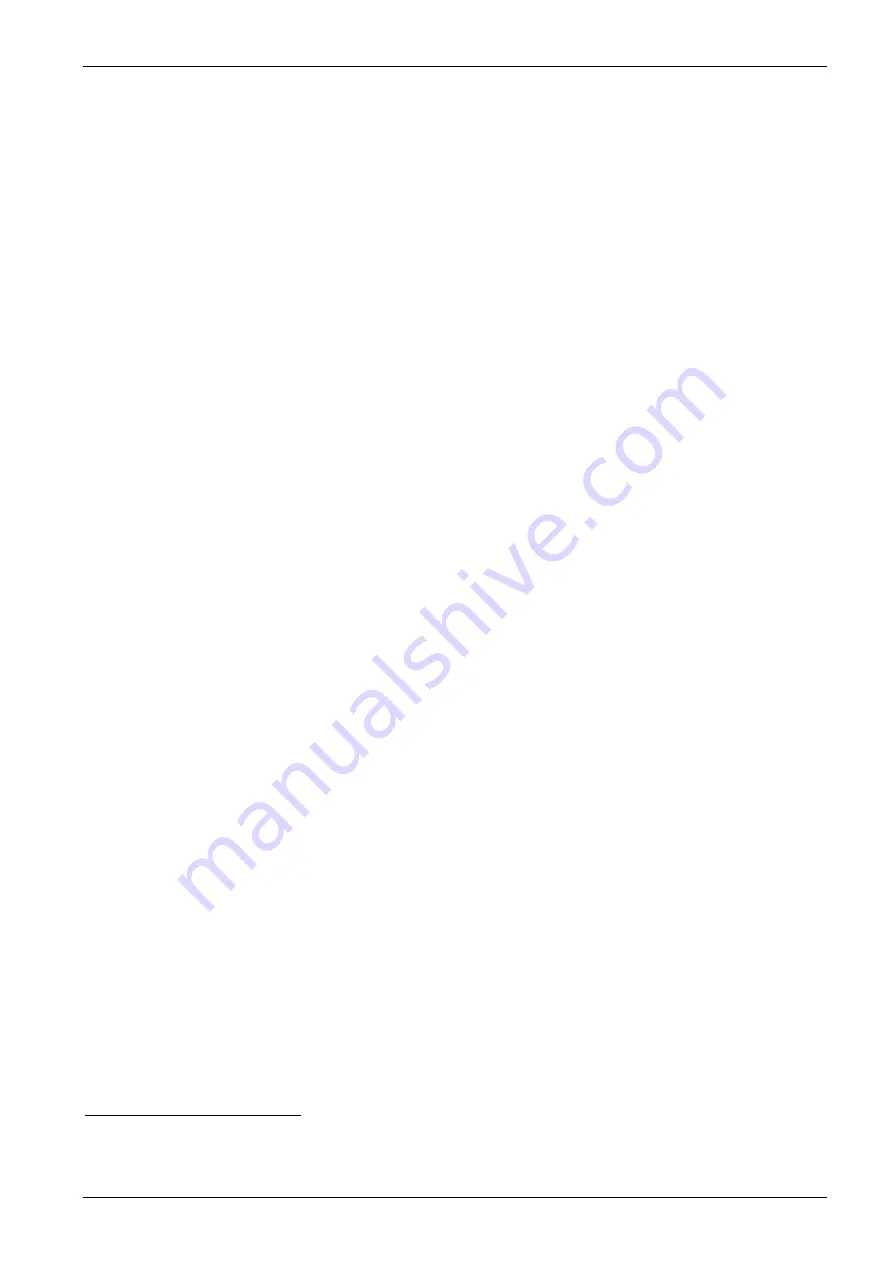
GT3000
STO Function
IMGT30017EN
71
6A.6.5 Installation instructions and extraordinary maintenance
The following instructions apply to start-up, after extraordinary maintenance operations and at least once a year. In order to facilitate
verifications, it is possible to enable the two channels (XM1-20 and XM70-1) separately.
Warning!
Qualified personnel, trained on the risks typical of the different operations, shall perform the verifications described below. Keep
away from the hazardous area and prevent access to personnel not tasked with the verification.
Before any operation, check the presence and proper activation of the parking brake in case of vertical or tilted axes.
6A.6.5.1
Controlled Stop
The STO function shall be enabled with the motor stopped, or the uncontrolled stop of the motor must never be dangerous.
In case of controlled stop according to category 1 of EN 60204-1:
1.
configure the motor moving at maximum speed and in the most heavy condition for the machine from the stop time standpoint,
2.
enable the safety function for the “STO” request (e.g. opening of the interlocked guard, emergency stop etc.);
3.
check that the inverter controls the motor during the deceleration time;
4.
check that the controls of the two channels XM1-20 and XM70-1 are disabled (0V) only when deceleration is over and with the
motor stopped;
5.
if the interlocked guard is provided with a locking device, make sure that it is released only with the motor stopped;
6.
in case of failure of any of the verifications listed in the two items above, check and adjust the automation sequence.
6A.6.5.2 Configuration according to category 3 EN 954-1:
Verification of the faulty restart
1.
Enable the “STO” request with the motor stopped;
2.
make sure that no control of the two channels (XM1-20 and XM70-1) is ON; otherwise, adjust wiring and the automation sequence
and repeat these steps from § 1;
3.
verify that the two feedback contacts between terminals XM1-2 and XM1-43 and between terminals XM70-3 and XM70-4 are both
closed: otherwise, replace the safety cards
, and repeat these steps from § 1;
4.
prepare the drive for motor rotation and make sure that the motor cannot be made revolve: otherwise, replace the safety cards
and repeat these steps from § 1;
5.
repeat the operations described above and enable only 1 channel at a time; make sure that the motor cannot be made revolve;
6.
disable the STO function by "increasing" both inputs;
7.
make sure that there are no short-circuits in the wiring of feedback contacts; otherwise, repair the fault and restart from § 1;
Failure simulations
8.
disable the “STO” request; both inputs shall be ”high”;
9.
cut-out the connection to the XM1-20 terminal of channel 2 “Drive Enable”;
10.
make sure that the control circuit detects the failure of channel 1 “STO”, enabling the “STO” alarm procedure in automatic mode and
inhibiting both channels, so that the operating sequence may not be restored up until the failure is removed; otherwise, check the
reasons for non-identification of the failure and proceed accordingly. Restart the verifications from § 1;
11.
disable the “STO” request, restore the connection to terminal XM1-20 and restore protection devices, if any;
12.
cut-out the connection to the XM70-1 terminal of channel 1 “STO”;
13.
make sure that the control circuit detects the failure of channel 2 “Drive Enable”, enabling the “STO” alarm procedure in automatic mode
and inhibiting both channels, so that the operating sequence may not be restored up until the failure is removed; otherwise, check
the reasons for non-identification of the failure and proceed accordingly. Restart the verifications from § 1;
14.
disable the “STO” request, restore the connection to terminal XM70-1 and restore protection devices, if any;
15.
cut-out the wiring on feed-back contacts’ terminals alternately, enable the “STO” function and check the automatic activation of the “STO”
alarm procedure, and inhibiting both channels, so that the operating sequence may not be restored up until the failure is removed;
otherwise, check the reasons for non-identification of the failure and proceed accordingly. Restart the verifications from § 1.
6A.6.5.3
CONFIGURATION ACCORDING TO CATEGORY 2 EN 954-1:
1.
Enable the “STO” request with the motor stopped;
2.
make sure that the control of the XM70-1 channel is OFF: otherwise, adjust wiring and the automation sequence, disable the “STO”
request and repeat these steps from § 1;
3.
make sure that the feedback contact between terminals XM70-3 and XM70-4 is closed: otherwise, replace the safety-related cards
and repeat these steps from § 1;
4.
make sure that the motor cannot be made revolve: otherwise, replace the safety-related cards
, and repeat these steps from § 1;
5.
disable the STO function by “increasing” the signal entering the XM70-1 terminal;
6.
make sure that there are no short-circuits in the wiring of the feedback contact; otherwise, repair the failure and restart from § 1;
Failure simulation
7.
disable the “STO” request;
8.
cut-out the conductor connection to the XM70-3 or XM70-4 terminal;
9.
enable the “STO” request;
3
According to the instructions mentioned in the relevant specification.
4
According to the instructions mentioned in the relevant specification.
9
According to the instructions mentioned in the relevant specification.
10
As above.
Содержание GT3000
Страница 1: ...GT3000 Hardware Software Manual www answerdrives com ...
Страница 2: ......
Страница 4: ......
Страница 8: ...Table Of Contents GT3000 iv IMGT30017EN ...
Страница 12: ...General Safety Precautions viii IMGT30017EN ...
Страница 25: ...GT3000 Technical Data IMGT30017EN 13 Frames IV V VIN SVGT045 166 IP20 ...
Страница 26: ...Technical Data GT3000 14 IMGT30017EN Frames IV V VIN SVGT045 166 IP54 ...
Страница 27: ...GT3000 Technical Data IMGT30017EN 15 Frames IV V IP20 NEMA1 SVGT105 170K J Peso 65Kg Weight 143Lbs ...
Страница 28: ...Technical Data GT3000 16 IMGT30017EN Frames VII VIII IP00 SVGT200 521K SVGT200 470F ...
Страница 29: ...GT3000 Technical Data IMGT30017EN 17 F series Frames 2xVII 2xVIII Parallel IP00 SVGT520 940M ...
Страница 30: ...Technical Data GT3000 18 IMGT30017EN K series Frames 2xVII 2xVIII Parallel IP00 SVGT580 960K ...
Страница 32: ...20 IMGT30017EN 3A 1 3 Lifting Frame VII VIII Figure 2A 1 Methods of Unloading and Lifting GT3000 Drives ...
Страница 36: ...Installation GT3000 24 IMGT30017EN 3A 2 1 4 Frames VII VIII Installatiion ...
Страница 58: ...GT3000 Installation 46 IMGT30004EN ...
Страница 107: ...GT3000 Terminal Boards and Power Schematics IMGT30017EN 95 ...
Страница 108: ...Terminal Boards and Power Schematics GT3000 96 IMGT30017EN SVGT200 260 320K J Motor earth connection Field bus ...
Страница 109: ...GT3000 Terminal Boards and Power Schematics IMGT30017EN 97 SVGT390 521K J Field bus Motor earth connection ...
Страница 110: ...Terminal Boards and Power Schematics GT3000 98 IMGT30017EN ...