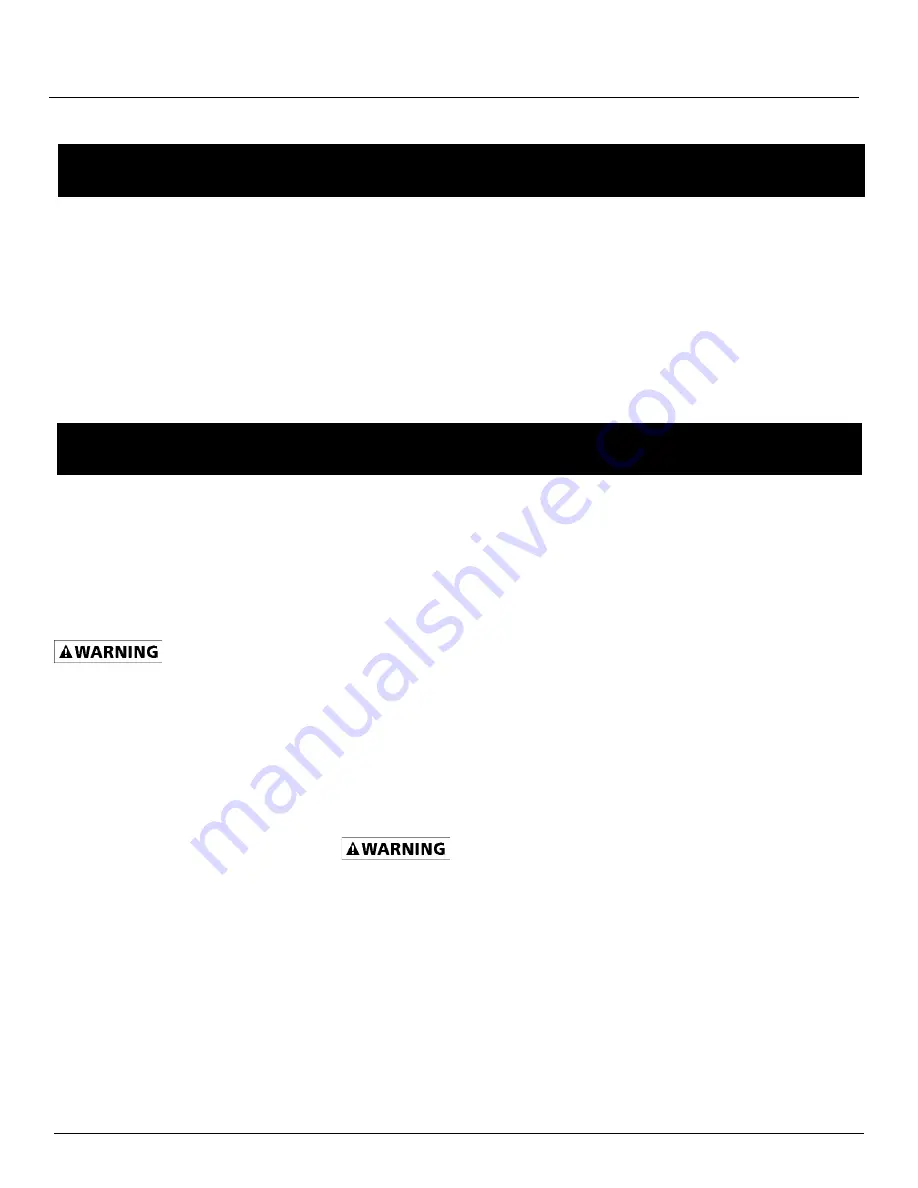
Specifications Information and Repair Parts Manual
5771-95, 5773-95, 5777-95, 577A-95,
Submersible Pumps Contractor Series
577B-95, 577D-95, 577E-95
Specifications
5771
2"
1.0
230VAC, 1 Phase
7.0
18 ft.
Cast Iron*
HCS
Buna N
5773
2"
2.0
230VAC, 1 Phase
10.9
32 ft.
Cast Iron*
HCS
Buna N
5777
3"
3.0
230VAC, 1 Phase
17.2
32 ft.
Cast Iron*
HCS
Buna N
577A
3"
5.0
230VAC, 3 Phase
13.9
32 ft.
Cast Iron*
HCS
Buna N
577B
3"
5.0
460VAC, 3 Phase
7.0
32 ft.
Cast Iron*
HCS
Buna N
577D
4"
7.5
230VAC, 3 Phase
19.5
32 ft.
Cast Iron*
HCS
Buna N
577E
4"
7.5
460VAC, 3 Phase
10.3
32 ft.
Cast Iron*
HCS
Buna N
NOTE:
Driver data is subject to change without notice, see label on driver for actual specifications.
(‡) Standard NPT (female) pipe thread
(HCS) High Chromium Steel
(*) With stainless steel and plastic components
Performance Chart
5771
---
85
62
20
--
--
48
5773
---
125
110
78
35
---
74
5777
---
210
182
120
42
---
68
577A/577B
---
234
215
168
102
30
88
577D/577E
---
440
410
325
190
---
78
(†) Shutoff; to convert to psi, divide by 2.31
(N/R) Not recommended
Maintenance
Make certain that
unit is
disconnected from power source
before attempting to service or
remove any component.
POWER CORD REPLACEMENT
Periodically inspect power cord and
replace whenever abrasion, cracking,
softening, or other signs of
deterioration are found.
Refer to Figures 2 and 3.
1. Place unit on workbench in upright
position.
2. Remove two fasteners (Ref. No.
39) which hold outer cord retainer
(Ref. No. 38).
3. Remove fasteners(s) (Ref. No. 5)
at handle (Reef. NO. 6) to free
wire loom (Ref. No. 2).
4. Remove three fasteners (Ref. No.
36) to detach handle and outer
shell (Ref. No. 37). Shell can now
be slid off towards top of pump.
5. Clean dirt and rust from around
wire cover (Ref. No. 7).
6. Remove two fasteners (Ref. No.
4) which hold inner cord retainer
(Ref. No. 3).
7. Remove four fasteners (Ref. No.
10) which hold wire cover in place.
8. Carefully pry cover from unit with
screwdriver.
IMPORTANT:
Be careful to keep rust
and other debris from falling into motor
housing during cover removal.
9. Take note of proper wire
configuration and connect new
power cord (Ref. No. 1) in
identical fashion.
If unsure about
above information
or wiring diagrams, consult an
electrician familiar with motor
wiring.
10. Clean sealing flanges if necessary
and reassemble pump in reverse
order.
IMPELLER INSPECTION /
REPLACEMENT
If pump develops poor performance
characteristics, impeller may be worn
or clogged.
IMPELLER INSPECTION
Refer to Figure 3.
1. Place unit on workbench in
horizontal position and clean rust
and buildup from around pump-to-
motor flange.
2. Remove four short fasteners (Ref.
No. 15) which attach base (Ref.
No. 30) to unit.
3. Pry base off with screwdriver. Rap
down on pump body with soft
mallet if necessary to separate
parts.
4. Inspect impeller (Ref. No. 26). If
clog is found, remove debris and
reassemble in reverse order. If
damage to impeller is found, such
as pitting, deep grooves, or
breakage, proceed to next section.
IMPELLER REPLACEMENT
5. Remove impeller fastener (Ref.
No. 28) by unscrewing in
counterclockwise direction.
NOTE:
To prevent motor shaft from
turning, wedge a screwdriver between
impeller vane and locknut (see Figure
2).
Discharge
Power Supply
Max.
Cord
Basic
Impeller
Model Outlet ‡
HP
@ 60 Hz
Amps
Length
Construction
Material
Seal
GPM AT TOTAL HEAD IN FEET *Max.
Model
5' 10' 20' 40' 60' 80' Head