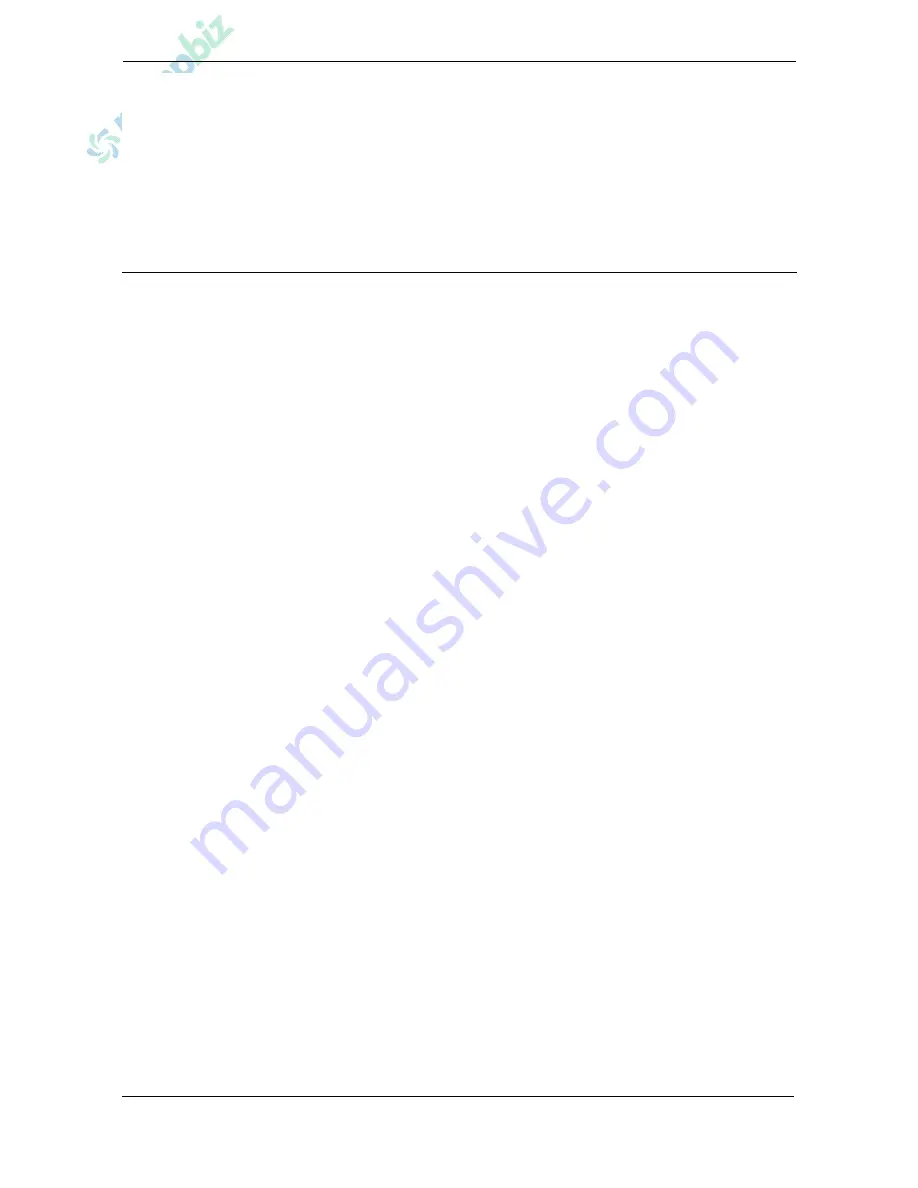
promised. Therefore, periodic
seal replacement is recom-
mended. Time interval
between replacements will
depend on abrasiveness of
liquid being pumped, tem-
perature, total accumulated
runtime, etc.
IMPORTANT:
Always replace
seal head (Ref. No. 18) and
both seal seats (Ref. Nos. 17
& 19) at same time to insure
proper mating of compo-
nents.
Refer to Figure 3.
1. Disassemble pump by fol-
lowing directions in both
“Power Cord
Replacement” and
“Impeller Inspection /
Replacement” sections.
2. With unit on it’s side and
wire cover, pump assem-
bly, and impeller
removed, lift shaft key
(Ref. No. 14) from
shaft/rotor (Ref. No. 13)
using a pliers.
3. Clean rust and buildup
from unit.
4. Drain oil from seal cavity
by removing drain plug
(Ref. No. 15) from motor
case (Ref. No. 16). Then
tip components overtop
of a catch pan until oil is
drained.
5. Remove three fasteners
(Ref. No. 22) which attach
casing (Ref. No. 21) to
motor case and pry two
components apart with
screwdriver.
6. Press on end of motor
shaft to separate from
motor case. Then careful-
ly guide upper end bell
(Ref. No. 12) along with
shaft/rotor and bearing
assembly out of motor
case. Shaft seal head will
now be free.
IMPORTANT:
Shaft seal head
(with spring) may have
unique ends, and two seal
seats may be different from
one another also. Be sure to
note size and color of each
before disassembly so that
new parts are installed in
proper orientation.
7. Remove upper seal seat
(Ref. No. 17) from motor
case by using a screwdriv-
er or dowel to press on
seal from rear. Do the
same for lower seal seat
(Ref. No. 19) in casing.
8. Clean seal seat cavities
before inserting new
seals.
9. Carefully wipe polished
surface of new seal seats
with a clean cloth.
10. Wet outside of rubber
portion of seal seats with
a light coating of soapy
water.
11. Press each new seal seat
squarely into cavity in
both motor case and cas-
ing. If seal seat does not
press squarely into cavity,
it can be adjusted into
place by pushing on it
carefully with a piece of
pipe or dowel. Always
use a piece of cardboard
between pipe and seal
seat to avoid scratching
seal seat. (This is a lapped
surface and must be han-
dled very carefully.)
12. After each seal seat is in
place, insure that it is
clean and has not been
marred.
13. Using a clean cloth, wipe
shaft and make certain
that it is perfectly clean.
14. Carefully guide motor
shaft through seal seat
and use a press to seat
bearing back into motor
case.
15. Apply a light coating of
soapy water to inside
rubber portion of seal
head and slide onto shaft
(be sure to start correct
end first).
16. Place casing back onto
motor housing being
careful to guide shaft
and avoid damage to seal
seat. Secure with
fasteners.
17. Press lip seal back in
place.
18. Refill cavity with oil
through fill hole and
reassemble in reverse
order.
Specifications Information and Repair Parts Manual
5780-98, 5790-95, 5792-95,
5800-99, 5810-99 and 5811-99
Submersible Pumps
Drainage / Sump Series
6
Maintenance
(Continued)