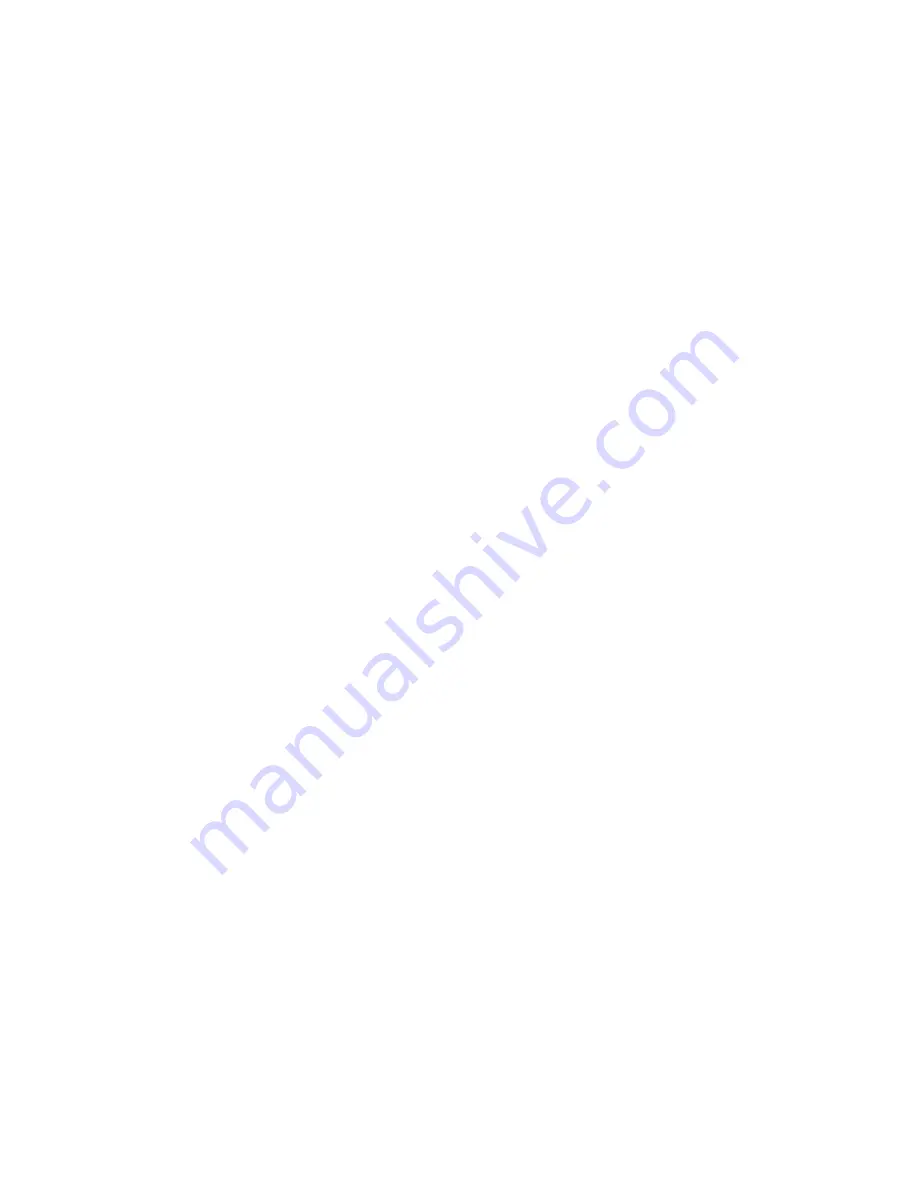
1.13: CONTROLLER BOARD
A single printed circuit board (PCB) contains all the digital and analog circuitry required to
operate the printer subsystems and to control the operational protocol. Interface correctors
are mounted to the PCB and are accessible via the rear of the printer. Connectors are also
provided for the motors, printhead, and sensors.
At the heart of the digital circuitry is an Intel 8085A microprocessor (MPU). The MPU,
along with several LSI peripheral devices and control circuits, utilizes a ROM-based
program which operates the electro-mechanical devices and handles communications
between the printer and host system.
1.14: RS-232C SERIAL INTERFACE
An RS-232C serial interface is provided and is capable of operating at BAUD rates from
110 to 19,200. Connection is via a standard 25-pin connector mounted on the PCB and is
accessible through a slot in the rear of the printer cover.
To allow operation at high BAUD rates, two handshaking, or restraint, protocols are
supported: XON-XOFF and DTR. Both are selectable by the operator as required.
XON-XOFF functions by sending an XOFF control code to the host when the FIFO buffer
fills to a “high water” mark, and then an XON when it empties to a “low water” mark. In
this manner, a host system win be able to communicate without any loss of data.
DTR functions by manipulating a hardware line to indicate the FIFO buffer status. When
the printer is able to receive more data, the line will be at a positive level. When the printer
is busy, the line is dropped to a negative level. This method of handshaking is preferred in
many systems since no decoding of serial data is required. DTR is available on pins 20 and
11 of the serial interface connector. See Table 1-1 for a complete description of the pin
configuration.
1-6
Содержание XL 300 SERIES
Страница 1: ...XL300 MAINTENANCE MANUAL Part No 105880 Rev A ...
Страница 15: ...1 10 ...
Страница 17: ...This page intentionally left blank 1 12 ...
Страница 24: ...3 2 ...
Страница 25: ...3 3 ...
Страница 26: ...3 4 ...
Страница 27: ...3 5 ...
Страница 28: ...3 6 ...
Страница 29: ...Figure 3 1 Controller Schematic Part No 105947 Sheets 1 8 PC Board 105601 3 6 ...
Страница 30: ...3 7 ...
Страница 31: ...3 8 ...
Страница 32: ...3 9 ...
Страница 33: ...3 10 ...
Страница 34: ...3 11 ...
Страница 35: ...3 12 ...
Страница 36: ...3 13 ...
Страница 37: ...3 14 ...
Страница 38: ...Figure 3 2 Controller Finished Assembly Component Layout Part No 105535 Sheets 1 and 2 PC Board 105601 3 15 ...
Страница 39: ...3 16 ...
Страница 40: ...3 17 ...
Страница 41: ...Figure 3 3 Power Supply PCB Schematic Part No 105623 PC Board 105622 3 18 ...
Страница 42: ...3 19 ...
Страница 43: ...Figure 3 4 Power Supply PCB Assembly Part No 105621 PC Board 105622 3 20 ...
Страница 44: ...3 20 ...
Страница 45: ...Figure 3 5 Operator Panel PCB Schematics Part No 105815 PC Board 105800 3 21 ...
Страница 46: ...3 22 ...
Страница 47: ...Figure 3 6 Operator Panel PCB Assembly Part No 105801 PC Board 105800 3 23 ...
Страница 48: ...3 24 ...
Страница 56: ...Figure 4 2 Electronic Module 4 8 ...
Страница 62: ...Figure 4 4 Ribbon Advance Mechanism 4 14 ...
Страница 65: ...Figure 4 7 Carriage Cable Replacement Figure 4 7 Carriage Cable Replacement 4 17 ...
Страница 74: ...Figure 4 12 Carriage Removal 4 27 ...
Страница 80: ...Figure 4 14 Paper Drive Idler Shaft 4 33 ...
Страница 84: ...Figure 4 16 Lower Paper Guide 4 37 ...
Страница 85: ...Figure 4 17 Lower Paper Guide Platen Alignment 4 38 ...
Страница 86: ...4 39 ...
Страница 87: ...4 40 ...
Страница 88: ...4 41 ...
Страница 89: ...4 42 ...
Страница 90: ...4 43 ...
Страница 91: ...4 44 ...
Страница 92: ...4 45 ...
Страница 93: ...4 45 ...
Страница 94: ...Figure 4 18 Illustrated Parts Breakdown 4 46 ...
Страница 95: ...4 47 ...
Страница 96: ...4 48 ...
Страница 97: ...4 49 ...
Страница 98: ...4 50 ...
Страница 99: ...4 51 ...
Страница 100: ...4 52 ...
Страница 101: ...4 53 ...
Страница 102: ...4 54 ...
Страница 103: ...4 55 ...
Страница 104: ...Figure 4 19 Illustrated Parts Breakdown DD 4 56 ...
Страница 106: ......
Страница 107: ...A 1 ...
Страница 108: ...A 2 ...
Страница 109: ...A 3 ...
Страница 110: ...A 4 ...
Страница 111: ...A 5 ...
Страница 112: ...A 6 ...
Страница 113: ...A 7 ...
Страница 114: ...A 8 ...
Страница 115: ...Figure A 2 Controller Board Assembly Part No 105768 Sheet 1 and 2 PC Board 105767 ...
Страница 116: ...A 9 ...
Страница 117: ...A 10 ...