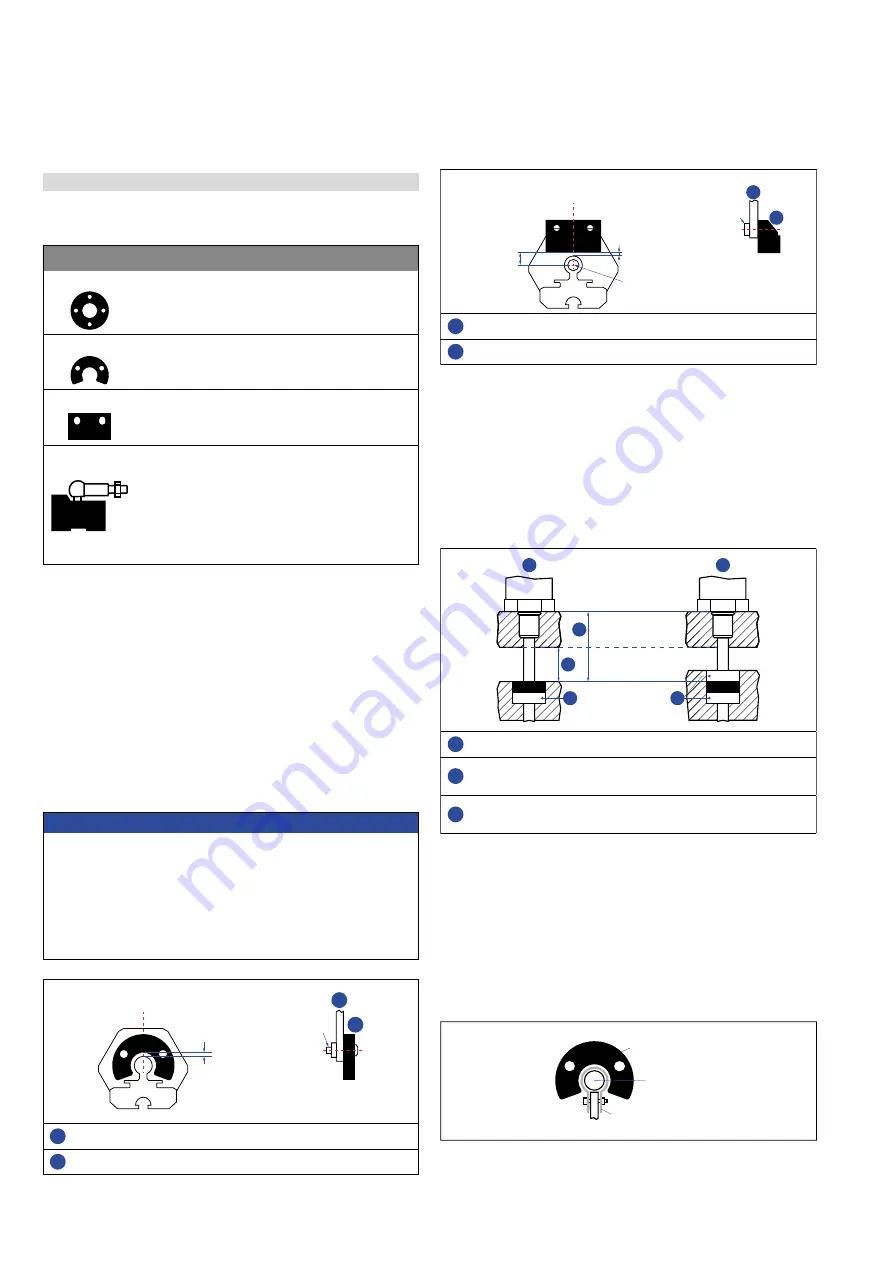
Temposonics
®
R-Series
V
Analog
Operation Manual
I 30 I
4.6 Magnet installation
Typical use of magnets
Rod sensors with stroke lengths ≥ 1 meter (3.3 ft.)
Support horizontally installed sensors with a stroke length of 1 meter
(3.3 ft.) and more mechanically at the rod end. Without using a support,
the sensor rod bends over and the rod and the position magnet may be
damaged. A false measurement result is also possible. Longer rod re-
quire evenly distributed mechanical support over the entire length (e.g.
part no. 561 481). Use an U-magnet (Fig. 35) for measurement.
NOTICE
• Mount ring magnets and U-magnets concentrically.
• Mount block magnets centrically over the sensor rod or the sensor
profile. The maximum permissible air gap must not be exceeded
(Fig. 32/Fig. 33).
• Take care to mount the primary sensor axis in parallel to the
magnet path in order to avoid damage to the carriage, magnet and
sensor rod/profile.
Controlling design dimensions are in millimeters and measurements in ( ) are in inches
Fig. 31: Typical use of magnets
Mounting ring magnets, U-magnets & block magnets
Install the magnet using non-magnetic material for mounting device,
screws, spacers etc.. The magnet must not grind on the sensor rod/
profile. Alignment errors are compensated via the air gap.
• Permissible surface pressure: Max. 40 N/mm
2
(only for ring
magnets and U-magnets)
• Fastening torque for M4 screws: 1 Nm; use washers, if necessary
• Minimum distance between position magnet and any magnetic
material has to be 15 mm (0.6 in.) (Fig. 34).
• If no other option exists and magnetic material is used,
observe the specified dimensions (Fig. 34).
Magnet mounting with magnetic material
When using magnetic material the dimensions of Fig. 34 must
be observed.
A.
If the position magnet aligns with the drilled piston rod
B.
If the position magnet is set further into the drilled piston rod,
install another non-magnetic spacer (e.g. part no. 400 633) above
the magnet.
Fig. 32: Mounting of U-magnet (part no. 251 416-2)
Fig. 33: Mounting of block magnet (part no. 403
448)
Fig. 34: Installation with magnetic material
Fig. 35: Example of sensor support (part no. 561 481)
M4
1
2
Air gap
Concentric mounting
of U-magnet
Part no. 251 416-2:
1.75 ±1 (0.07 ±0.04)
1
U-magnet
2
Non-magnetic mounting plate
Magnet
Typical sensors
Benefi ts
Ring magnets Rod model
(RH5, RFV, RDV)
• Rotationally symmetrical
magnetic fi eld
U-magnets
Profi le &
rod models
(RP5, RH5, RFV, RDV)
• Height tolerances can be
compensated
,
because the
magnet can be lifted off
Block magnets
Profi le &
rod models
(RP5, RH5, RFV, RDV)
• Height tolerances can be
compensated
,
because the
magnet can be lifted off
Magnet sliders
Profi le models
(RP5)
• The magnet is guided by
the profi le
• The distance between the
magnet and the waveguide
is strictly defi ned
• Easy coupling via the
ball joint
M4
2
1
8 ±2
(0.31 ±0.08)
Sensor element
Air gap:
3 ±2
(0.12 ±0.08)
Centered mounting
of block magnet
1
Block magnet
2
Non-magnetic mounting plate
Magnet
Magnet
1
2
3
A
B
Magnetic
material
3
1
Null zone, depends on sensor model
2
Distance between position magnet and any magnetic material
(≥ 15 mm (≥ 0.6 in.))
3
Non-magnetic spacer (≥ 5 mm (≥ 0.2 in.)) –
Recommendation: 8 mm (0.31 in.)
U-magnet
Sensor rod
Non-magnetic fixing clip