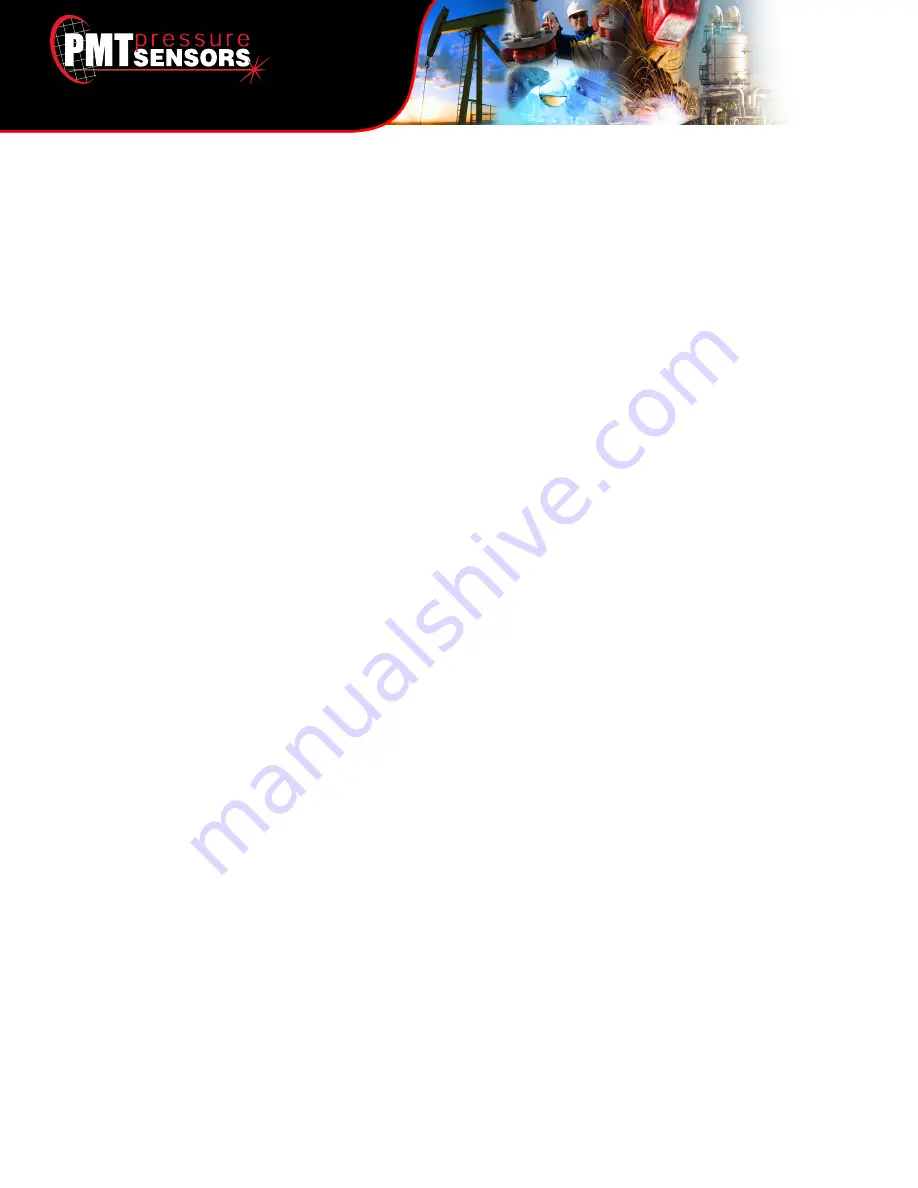
User Manual
9
will slowly increase. When output reaches mid-
span**, quickly turn reset dial counterclockwise
to stop. Output should hold at mid-span.
Instrument is now operating as a proportional
controller. Set red pointer to desired value.
Watch control operation. If controlled variable
cycles, widen proportional band in steps until
stable. Note period of oscillation of controlled
variable when red pointer is moved a small
amount up or down. The period is the time
between two maximum or minimum peaks. If
controlled variable is sluggish and wandering,
reduce proportional band setting in steps, until
controlled variable is jittery or cycles a bit. Note
period of cycling in minutes.
Increase proportional band to 2-21/2 times the
band setting which was obtained by preceding
method. Reset valve may be set for the same
time as the period of cycling.
The above settings are suggested values
and may be varied depending on the specific
requirements of the process. For more stability,
widen proportional band and/or increase the
reset time. If process is too sluggish, reduce
proportional band and/or reset time. Note that
a little less than optimum reset time may cause
cycling while even three to four times optimum
may make little difference. This is particularly true
for processes with slow load changes.
After process has stabilized, the red and black
pointer may not be coincident. To synchronize,
hold hex hub of red pointer with 0.25” wrench
and turn pointer, pushing it near its center to
avoid bending it.
If the process levels off too soon and approaches
the set point in steps, the rate action is
excessive. If there is an overshoot, more rate
action is needed. The final setting should be
a compromise between start-up and running
performance.
TUNING PROPOR RESET + RATE
CONTROLLER
With the rate valve fully open, proceed as
described in TUNING PROPORTIONAL
CONT RESET.
Now increase the rate time in steps watching the
process become more stable and finally unstable
again. Return to a value giving stability. In case
of uncertainly, try about 1/8 of the cycle time
noted above.
Repeat adjustment of proportional band, which
now may permit a somewhat narrower setting,
and then increase the rate time. Watch the
process long enough to be sure the adjustments
have sufficient margin of safety for normal
process upsets.
If the rate time has to be kept close to zero, either
the process does not need rate action or the
process or control system is not in condition to
tolerate rate action.
After process has stabilized, the red and black
pointer may not be coincident. To synchronize,
hold hex hub of red pointer with 0.25” wrench
and turn pointer, pushing it near its center to
avoid bending it.
* 20 psi (140 kPa) for 15 psi (100 kPa) output
35 psi (240 kPa) for 30 psi (200 kPa) output
65 psi (450 kPa) for 60 psi (400 kPa) output
** 9 psi (60 kPa) for 3-15 psi (20-100 kPa) controllers
18 psi (125 kPa) for 6-30 psi (40-200 kPa) controllers
36 psi (250 kPa) for 12-60 psi (80-400 kPa) controllers
MANUAL CONTROL AND START UP
Some processes must be brought up to control
point manually as the first overshoot on start
up may be well beyond permissible limits. In
addition, manual operation of process provides
a means of diagnosing difficulties in the process
which might ordinarily be attributed to the
controller.
FOR PROPORTIONAL CONTROLLERS
To start up manually
Note controller action
(direct or reverse). If direct acting, set red pointer
well below black pointer and desired value. If
reverse acting, set red pointer well above black
pointer and desired value. This will cause
controller to put out full output pressure. Adjust
diaphragm control valve opening by adjusting
supply regulator. When process is under control
at desired value, note output pressure.
To switch to automatic
Move red pointer back
toward desired value until output pressure just
drops. Restore supply pressure. To correct valve
adjust red pointer to be sure output pressure
is brought to exact value noted during manual
control.
Содержание PMT 40
Страница 1: ...Model 40 PNEUMATIC INDICATING CONTROLLER K796131 REV F 06 2021...
Страница 12: ...User Manual 7...
Страница 34: ...User Manual 29 12 K810805 Post Mounting Screw 8 Type F Self Thread 3 required 13 H 2025 WG New H074807 Gasket...
Страница 42: ...User Manual 37 MULTI MODE FEEDBACK ASSEMBLIES...
Страница 45: ...User Manual 40 REPLACEMENT PARTS KITS...
Страница 47: ...User Manual 42...
Страница 48: ...User Manual 43 INDICATING CONTROLLER OUTLINE DIMENSIONS...